What is MIG welding? Components, benefits and applications in machining and welding of pumps, industrial valves and compressors
What is MIG welding? Components, benefits and applications in machining and welding of pumps, industrial valves and compressors
What is MIG welding
MIG welding (Metal Inert Gas) is a fundamental technique for the machining and welding industry of critical industrial components, such as, industrial pumps, valves, and compressors. At Asimer Group, we utilize MIG welding to ensure maximum efficiency, precision, and durability in every project, whether in the manufacturing of new components or the repair of equipment operating in challenging environments.
MIG welding, also known as GMAW (Gas Metal Arc Welding), employs a continuous electrode wire and a shielding gas to create an electric arc that melts the wire and base metals, forming a strong and reliable joint. At Asimer Group, this process is crucial for performing long and continuous welds, which are essential in the production and repair of industrial pumps and valves that must withstand high pressure and temperature conditions. Additionally, we also work with TIG welding and advise our clients on the differences between TIG and MIG welding to help them choose the most suitable technique based on their specific needs.
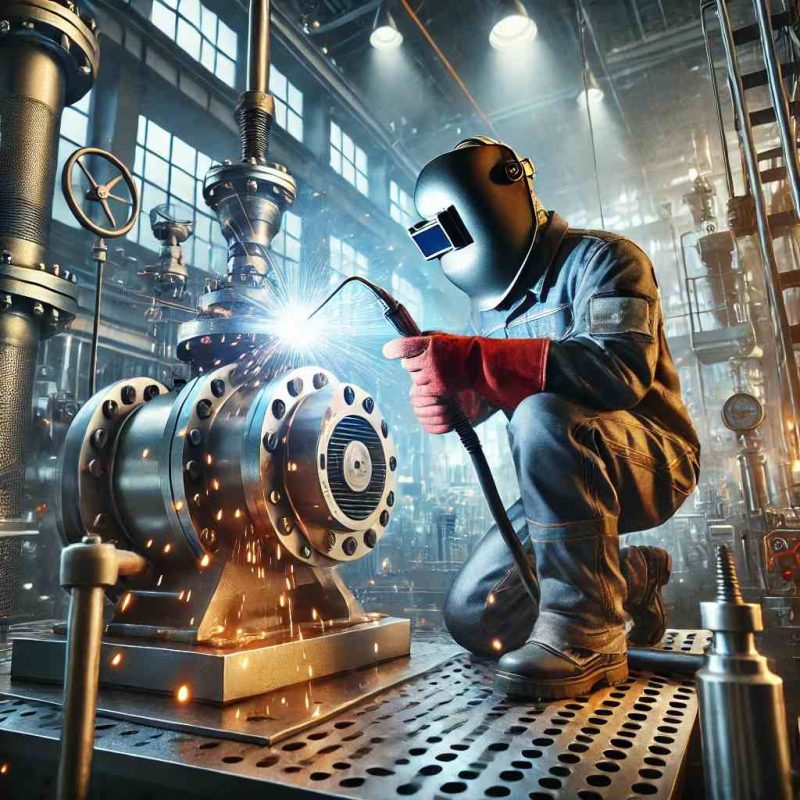
What is MIG welding
MIG Welding (Metal Inert Gas) is a fundamental technique for the machining and welding industry of critical industrial components, such as industrial pumps, valves, and compressors. At Asimer Group, we use MIG welding to ensure maximum efficiency, precision, and durability in every project, whether in the manufacturing of new components or the repair of equipment operating in challenging environments.
MIG welding, also known as GMAW (Gas Metal Arc Welding), employs a continuous electrode wire and a shielding gas to create an electric arc that melts the wire and base metals, forming a strong and reliable joint. At Asimer Group, this process is essential for performing long and continuous welds, which are crucial in the production and repair of industrial pumps and valves that must withstand high pressure and temperature conditions.
Additionally, we also work with TIG welding and provide expert guidance to our clients on the differences between TIG and MIG welding, helping them choose the most suitable technique based on their specific needs.
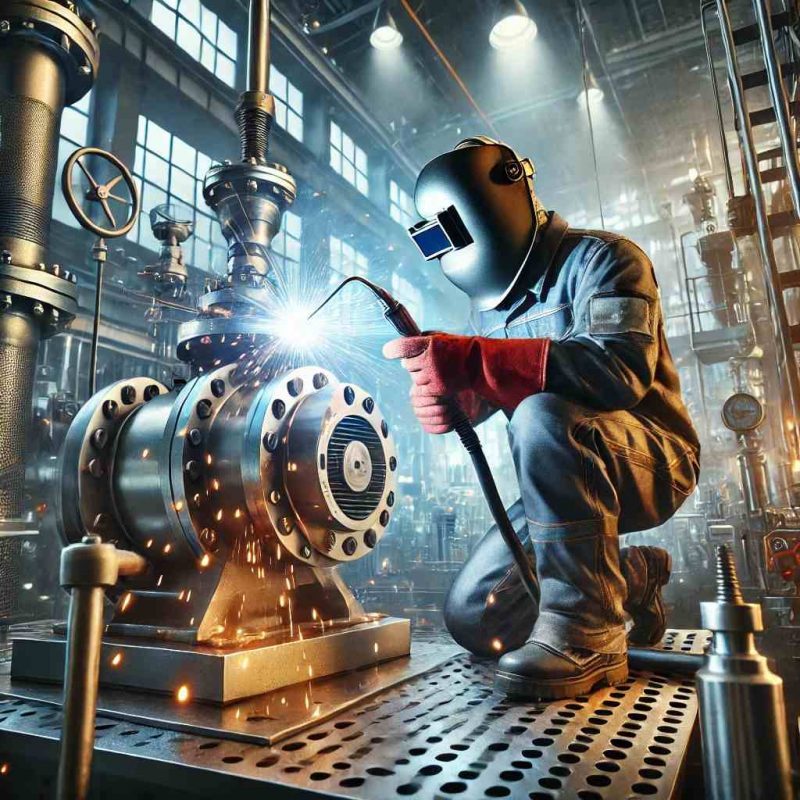
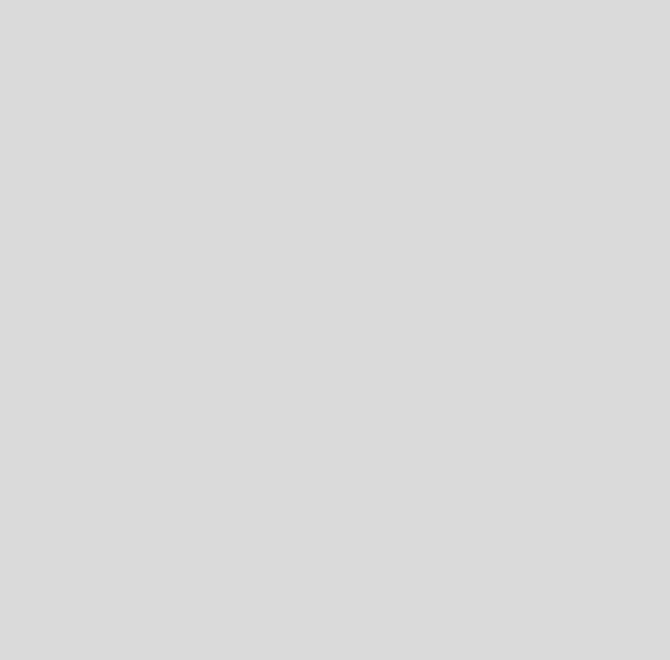
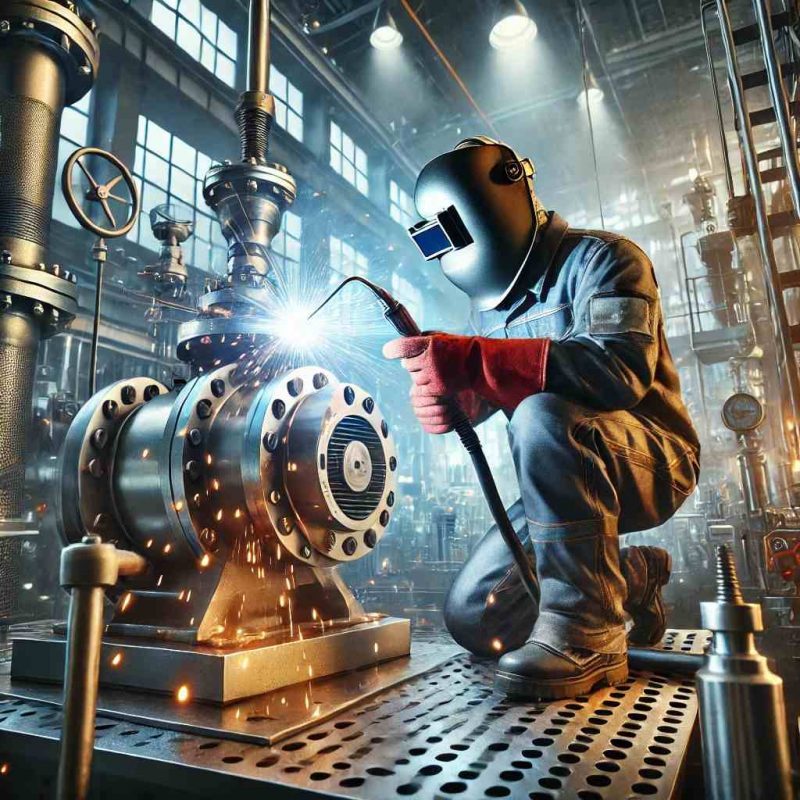
Key components of MIG welding
Key components of MIG welding
Key components of MIG welding
Power
supply
At Asimer Group, our power supplies are precisely calibrated to adjust the required voltage and current, ensuring quality and consistency in every weld.
MIG welding
wire
We select welding wire that perfectly matches the specifications of the materials we use, ensuring optimal performance in the joining of critical components.
Gas
protection
We use argon and CO2 mixtures, among other inert gases, to shield the welding area from atmospheric contaminants, ensuring clean and durable welds on materials such as stainless steel and special alloys.
Benefits of MIG welding in industrial pumps and valves
At Asimer Group, we leverage the advantages of MIG welding to:
- Maximize Productivity: The high deposition rate allows us to complete projects faster without compromising quality, a crucial factor in the manufacturing and repair of pumps, industrial valves, and compressors.
- Ensure Precision and Control: Our experts use MIG welding to achieve precise and secure joints, ensuring that each component meets the highest quality standards, including leak-tightness in critical valves.
- Adapt to Various Metals: With our ability to work with a wide range of materials, including carbon steels, stainless steels, and corrosion-resistant alloys, we offer versatile solutions tailored to the specific needs of our clients in sectors such as oil & gas, water treatment, cryogenics, petrochemicals, desalination, and naval industries.
Common applications of MIG welding at Asimer Group
Welding of Pump and Valve Casings:
We perform strong and reliable joints that are essential for the structural integrity of pump and valve casings, ensuring their performance in high-pressure environments, including centrifugal pump components and other centrifugal pump applications.
Repair of Worn Components:
Our expertise in MIG welding allows us to restore components damaged by wear or corrosion, extending the service life of our clients’ industrial equipment.
Modifications and Customizations:
We adapt components to specific requirements, such as adding fittings in the oil and gas industry or making adjustments to casings to meet the most demanding technical specifications.
Practical tips for optimizing MIG welding at Asimer Group
At Asimer Group, we apply a series of good practices to ensure excellence in each MiG welding project:
Selection
of shielding gas
We use material-specific gas mixtures, such as pure argon for stainless steels and sensitive alloys. This ensures optimal fusion and stable arc, crucial for the quality of our welds.
Preparation and cleaning of surfaces:
Our technicians perform a thorough cleaning of the surfaces to be welded using wire brushes, degreasing agents and specialized sandpaper, removing any contaminant that could compromise the integrity of the welded joint.
Setting parameters:
 
At Asimer Group, we adjust the welding wire speed, current and voltage according to project specifications and metal type. This allows us to obtain consistent, high quality welds, minimizing defects and rework.
Practical tips to optimize MIG welding at Asimer Group
At Asimer Group, we apply a series of good practices to ensure excellence in each MiG welding project:
Selection of the shielding gas
We use material-specific gas mixtures, such as pure argon for stainless steels and sensitive alloys. This ensures optimal fusion and stable arc, crucial for the quality of our welds.
Preparación y limpieza de las superficies:
Our technicians perform a thorough cleaning of the surfaces to be welded using wire brushes, degreasing agents and specialized sandpaper, removing any contaminant that could compromise the integrity of the welded joint.
Setting parameters:
 
At Asimer Group, we adjust the welding wire speed, current and voltage according to project specifications and metal type. This allows us to obtain consistent, high quality welds, minimizing defects and rework.
Recommendations for application and maintenance in MIG welding processes
To ensure that our welding processes remain in optimal condition, Asimer Group follows strict application and maintenance recommendations.
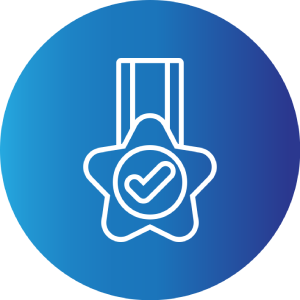
Quality Supervision and
  Control
Quality Supervision and
  Control
We conduct periodic inspections and apply non-destructive testing, including liquid penetrant testing, to verify the quality of our welds. This ensures that all components manufactured or repaired at Asimer Group comply with technical specifications and industry standards.
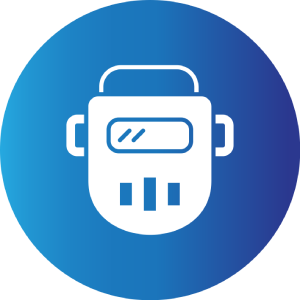
equipment maintenance
equipment maintenance
continuous Staff training
Continuous Staff Training
At Asimer Group, we invest in the continuous training of our team of welders and technicians in advanced TIG and MIG welding techniques, CNC technology, and CNC machining, as well as ensuring accuracy in CNC machining. We also train our personnel in the use of advanced measuring instruments such as the measuring arm and our metrology room.
Innovation in MIG welding materials and techniques
At Asimer Group, we are committed to constant innovation. We not only employ MIG welding in a conventional manner; we also invest in developing new techniques that maximize energy efficiency and Industry 4.0. This approach includes the use of Plasma Transferred Arc (PTA) welding and automated welding systems such as automatic MIG welding, as well as the development of chip removal machining processes for specialized parts. Additionally, we have Horizontal machining centers, which ensure the manufacturing of complex parts with high precision and durability, ideal for valve components and other industrial equipment.
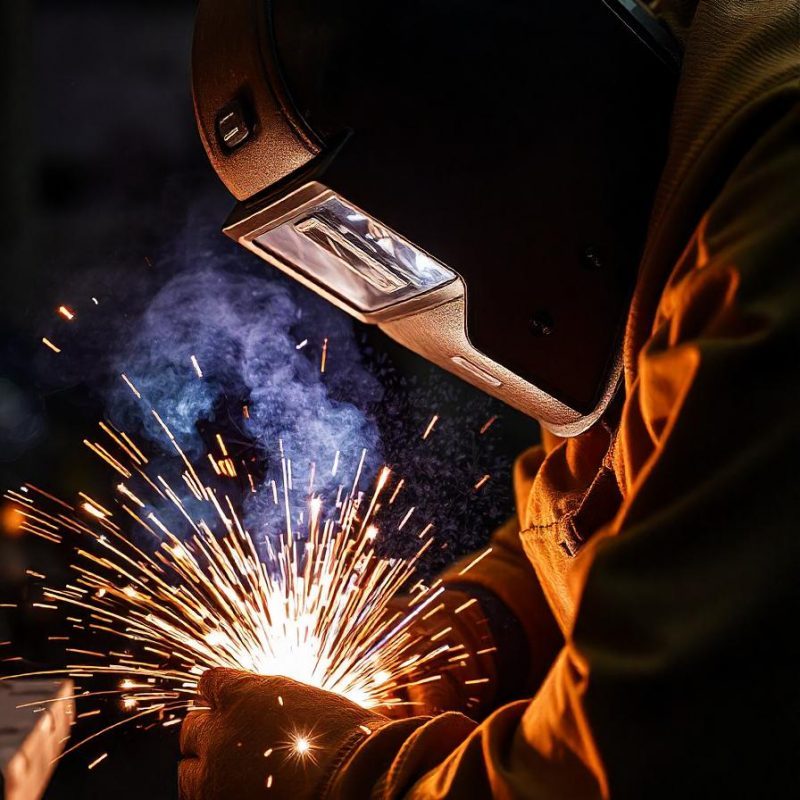
Innovation in MIG welding materials and techniques
At Asimer Group, we are committed to continuous innovation. We not only employ MIG welding in a conventional way but also invest in developing new techniques that maximize energy efficiency and Industry 4.0. This approach includes the use of Plasma Transferred Arc (PTA) welding and automated welding systems such as automatic MIG welding, as well as the development of chip removal machining processes for specialized parts. Additionally, we have horizontal machining centers that ensure the manufacturing of complex components with high precision and durability, making them ideal for valve components and other industrial equipment.
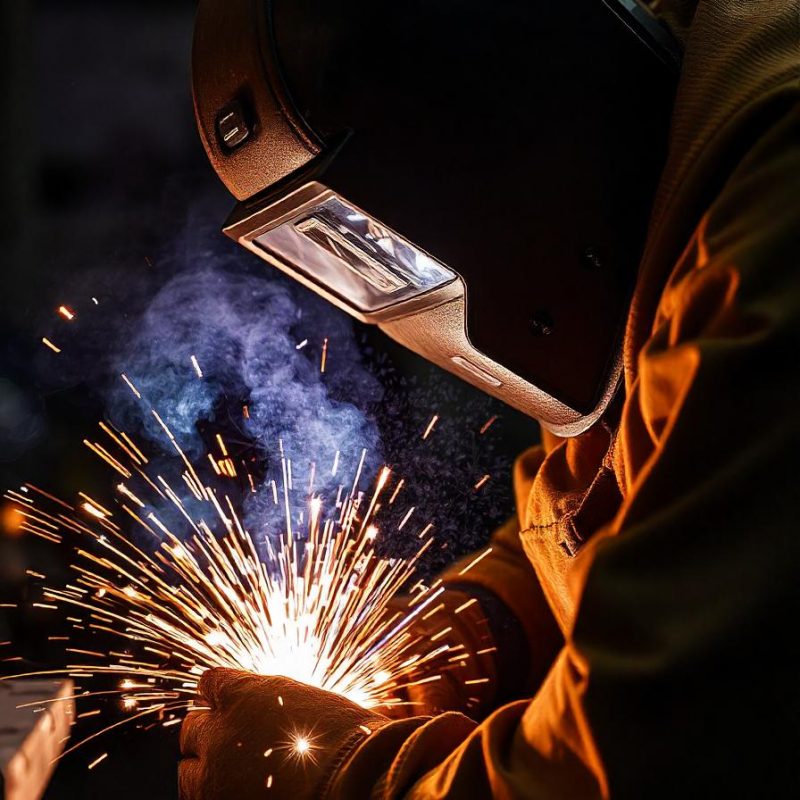
Customizing MIG welding services according to customer needs
We understand that each client and project is unique, which is why at Asimer Group we offer a personalized approach. From selecting the type of wire and shielding gas to making specific adjustments in welding parameters, we adapt our services to meet the exact specifications of each application. This customization not only improves the quality of the welds but also ensures that the manufactured or repaired components function optimally in their respective operating environments, such as in cryogenic applications, oil refining, and the manufacturing of industrial valve types like butterfly valves.
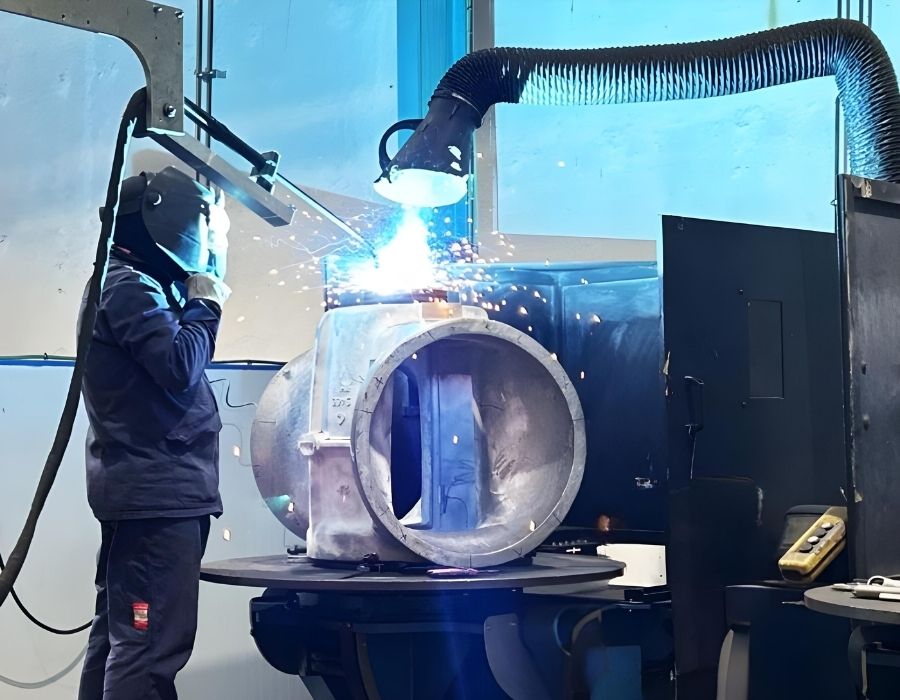
Automatic MIG welding integration
To maximize precision and reduce cycle time in complex projects, Asimer Group has integrated automation and robotics technology into our MIG welding processes. This not only allows us to perform repetitive welds with high precision, but also ensures consistent quality in large production volumes. Our automated systems are designed to handle projects that require high levels of repeatability and control, which is essential in the manufacturing of critical parts for pumps, industrial valves, and compressors, especially in the machining of large-scale valves.
Contact us for customized welding solutions
If you are looking for a company that combines experience, innovation, and a personalized approach to welding pumps, industrial valves, and compressors, Asimer Group is your ideal partner. We take pride in offering solutions that not only meet the highest quality standards but are also designed to exceed our clients’ expectations. Do not hesitate to contact us to discuss your project and explore how we can help you optimize the reliability and performance of your industrial equipment.
Contact us for customized welding solutions
If you’re looking for a company that combines experience, innovation, and a personalized approach in welding pumps, industrial valves, and compressors, Asimer Group is your ideal partner. We take pride in offering solutions that not only meet the most demanding quality standards but are also designed to exceed our clients’ expectations. Don’t hesitate to contact us to discuss your project and explore how we can help you optimize the reliability and performance of your industrial equipment.

Experience

Innovation

Customized approach
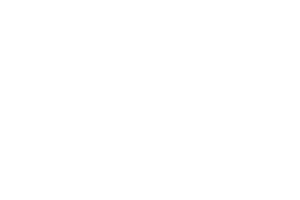
Experience
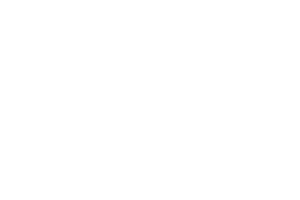
Innovation
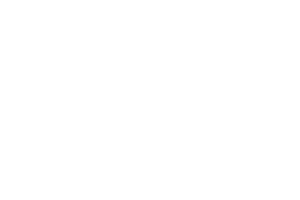