The world of chip removal machining in the CNC era is like a journey through time, where ancient manufacturing techniques meet technological advancement. It is fascinating to see how this technique has evolved from the humble beginnings of manual lathes to the sophisticated field of CNC machining today.
In a sector where efficiency is a crucial factor, technological innovations are leading the way towards more efficient and sustainable production, as can be seen in the manufacturing of industrial valves. However, to achieve optimal efficiency, it is essential to ensure an exceptional level of precision at every step of the process. As we mentioned in our article “The Accuracy in CNC Machining,” precision is the cornerstone upon which efficiency in CNC machining is built. Every movement of the cutting tool, every parameter adjustment, and every programming decision must be executed with millimeter precision to maximize performance and minimize waste. Therefore, when optimizing efficiency in CNC machining in the era of chip removal, it is imperative to dedicate meticulous attention to ensuring precision in every aspect of the process.
Roots and Evolution of Chip Removal Machining
This method has its origins in traditional manufacturing practices dating back centuries. From early manual lathes and milling machines to today’s highly automated CNC machines, this process has undergone significant evolution. The introduction of CNC technology in the 1950s was a crucial milestone, enabling the automated control of cutting tools and leading to greater precision and efficiency in production. Since then, chip removal machining has continued to advance with more sophisticated tools, more precise control systems, and advanced programming techniques.
Advantages and Challenges of Chip Removal Machining
And what about the advantages offered by chip removal machining? There are many!
This method presents numerous crucial advantages for modern manufacturing. One of the main ones is its ability to produce parts with exceptional precision. Through precise control of CNC machining tools, very tight tolerances can be achieved, ensuring the quality and uniformity of manufactured parts. Additionally, it allows for a superior surface finish compared to other methods, reducing the need for subsequent finishing processes and improving efficiency.
Versatility is another key advantage of chip removal machining. This technique is applied to a wide variety of materials, from metals to plastics, ceramics, and composites, making it suitable for various industrial applications. Furthermore, it is highly scalable and can be adapted to produce parts of different sizes and geometries, from small and complex components to large and simple structures.
Of course, it’s not all sunshine and rainbows. There are challenges we must face to ensure its effectiveness and efficiency. One of the main challenges is controlling the heat generated during the cutting process, as increased temperature can cause deformations in the workpiece, premature tool wear, and changes in material properties. Therefore, it is crucial to implement effective cooling and lubrication strategies to keep the temperature under control and ensure the integrity of the manufactured parts.
Additionally, selecting the right cutting tools and optimizing machining parameters are crucial to maximizing process efficiency and minimizing production costs. This requires a deep understanding of the characteristics of the materials being machined, as well as the capabilities and limitations of the machine tools used. Furthermore, chip removal machining can generate large quantities of chips and waste, posing challenges in terms of waste management and workplace safety.
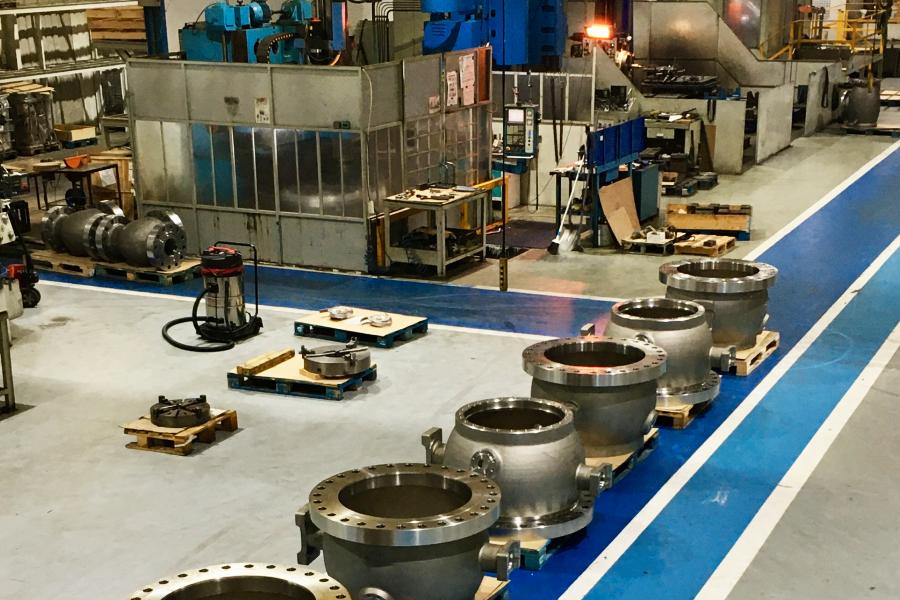
Emerging Technologies in Chip Removal Machining
Efficiency in chip removal machining has become a fundamental pillar for competitiveness and progress in the industry, as highlighted in our article on “Pump and Valve Manufacturing Transformation: CNC Machining detailed Applications.“
In addition to Industry 4.0, other emerging technologies are revolutionizing the manufacturing landscape. For example, high-speed machining uses significantly higher cutting speeds to reduce cycle times and increase productivity, while micromachining focuses on manufacturing microscopic-sized parts with extremely tight tolerances, essential in industries such as electronics and biotechnology. Furthermore, additive manufacturing, also known as 3D printing, is increasingly complementing chip removal machining by enabling the creation of complex geometries and custom internal structures.
In the context of chip removal machining in the CNC era, the constant pursuit of efficiency is closely linked to the precision required in the manufacturing of key industrial components, such as needle control valves. These valves play a fundamental role in numerous industrial processes, where precision in their operation is essential to ensure optimal flow control. As discussed in our article on “Needle Control Valves: Precision at the Heart of the Industry,” manufacturing these valves requires high-precision machining, which can be efficiently achieved through chip removal machining in the CNC era. By optimizing efficiency in the CNC machining process, the quality and precision necessary to manufacture reliable and accurate needle control valves are ensured.
Artificial intelligence (AI) and machine learning are revolutionizing chip removal machining by offering advanced optimization and analysis capabilities. AI systems can analyze large volumes of process data to identify patterns and trends, thus optimizing cutting parameters to maximize efficiency and quality. Additionally, machine learning enables early detection of issues and prediction of failures, reducing downtime and increasing productivity.
The pursuit of efficiency is a constant goal for advanced engineering companies like Asimer Group. A crucial element in this process is the choice and use of cutting-edge equipment, such as the Trevisan Machining Center. This machining center stands as a fundamental pillar in Asimer Group’s success strategy, enabling the implementation of advanced engineering solutions with precision and efficiency. The integration of innovative technologies into the Trevisan Machining Center not only optimizes efficiency in chip removal machining but also drives the company’s ability to deliver customized, high-quality solutions to its customers.
Environmental Considerations and Sustainability in Chip Removal Machining
As awareness of environmental sustainability increases, the chip removal machining industry is taking steps to reduce its impact on the environment. This includes implementing more efficient manufacturing practices that minimize energy and raw material consumption, as well as reducing waste generated during the machining process. Additionally, biodegradable and environmentally friendly cutting fluids are being developed and used, which are less harmful to the environment and safer for workers.
Another important consideration is waste management and the recyclability of materials used in the machining process. Companies are seeking ways to reduce the amount of waste generated and maximize the recycling and reuse of materials, which helps minimize the environmental impact of manufacturing. Furthermore, new machining technologies and processes that are more resource-efficient and generate less waste are being researched and developed, contributing to a more sustainable and responsible manufacturing industry.
Chip removal machining in the industry: specialized applications and versatility
Chip removal machining is a widely used technique in a variety of industries, each with specific requirements and challenges. From manufacturing critical components in the aerospace industry to producing high-precision medical devices and creating robust components for the automotive industry, this process plays a crucial role in the production of essential parts in various industrial areas.
- Aerospace Industry
Chip removal machining is used to manufacture crucial components of aircraft engines and structures, such as turbine blades, compressor casings, and fuselage structures. These parts require precise and reliable machining to ensure their performance under extreme flight conditions.
- Medical Industry
This process is used to produce implantable devices and high-precision surgical tools, such as orthopedic implants, dental prosthetics, and customized surgical instruments. The ability of chip removal machining to manufacture parts with complex geometries and tight tolerances is essential for the success of these medical devices.
- Automotive Industry
This method is applied in the manufacturing of a wide variety of components, from engines and transmissions to steering and suspension systems. Parts such as pistons, connecting rods, gears, and axles require exceptional precision and superior mechanical strength to ensure reliable performance under demanding operating conditions.
In addition to these mentioned industries, chip removal machining finds specialized applications in other key sectors.
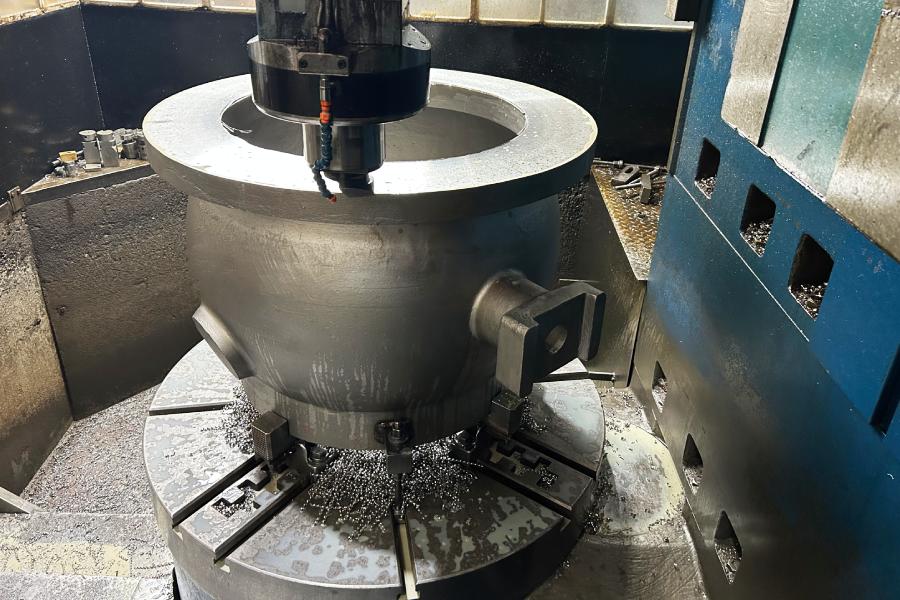
- Petrochemical Industry
For example, this process is essential in the manufacturing of components used in industrial valves, fittings, and processing equipment. These parts must meet rigorous standards of quality and strength to ensure safe operation in corrosive and high-pressure environments.
In the context of chip removal machining in the CNC era, the constant pursuit of efficiency is a primary goal driving competitiveness and success in the industry. A prominent application of this technology is found in the petrochemical industry, where efficiency and quality are crucial for the smooth operation of operations. In our article on “CNC Technology: Improving the Petrochemical Industry with Efficiency and Quality,” we explore how innovations in CNC technology are transforming this sector, enabling greater precision, shorter production times, and significant waste reduction. By harnessing the capabilities of chip removal machining in the CNC era, petrochemical companies can optimize their manufacturing processes, improve the quality of their products, and increase their competitiveness in the market.
Production in the petrochemical industry greatly benefits from the precision and reliability offered by chip removal machining, ensuring optimal equipment operation and increased safety in operations.
- Paper Mill Production
Chip removal machining plays an important role in the manufacturing of components for specialized machinery, such as rollers and blades, which are critical to the paper mill production process.
- Water and Wastewater Treatment
This process is used to manufacture a wide range of components and equipment used in water treatment plants and distribution systems, ensuring efficient and reliable operation in challenging environments.
- Naval Industry
Chip removal machining is crucial in the manufacturing of components used in shipbuilding, such as hulls, propellers, and propulsion systems, ensuring structural integrity and performance of vessels.
This process is employed in the manufacturing of critical components of equipment for the storage of cryogenic gases, ensuring their safe operation under extreme temperature conditions.
- Water Desalination
Chip removal machining is used to manufacture equipment and components used in desalination plants, ensuring efficient and reliable operation in corrosive and high-pressure environments.
- Oil & Gas Industry
This process is fundamental in the manufacturing of components used in drilling equipment, pipeline systems, and control valves, ensuring their safe operation in extremely demanding environments.
In summary, chip removal machining is a versatile technique that finds specialized applications in a wide variety of industries, playing a crucial role in the manufacturing of critical components with precision and reliability.
Future Perspectives of Chip Removal Machining in the Industry
Chip removal machining has a promising future in the manufacturing industry, with continuous innovations and technological advances transforming the way parts are made. The integration of emerging technologies such as artificial intelligence, machine learning, and additive manufacturing is expected to further drive efficiency and quality in the process.
Artificial intelligence and machine learning can optimize machining parameters in real-time, maximizing productivity and minimizing downtime. Meanwhile, additive manufacturing will complement chip removal machining by enabling the creation of complex geometries and customized internal structures that would be difficult or impossible to achieve with conventional manufacturing methods.
Additionally, the chip removal machining industry is expected to continue evolving towards greater sustainability and environmental responsibility. Companies are adopting more efficient and sustainable manufacturing practices that minimize the environmental impact of production and promote responsible use of natural resources. This includes the implementation of recycling technologies and materials reuse, as well as the development of more efficient and eco-friendly manufacturing processes. Ultimately, chip removal machining will remain a cornerstone of the manufacturing industry, providing an effective and cost-efficient way to produce high-quality parts with precision and consistency.
Conclusion
With a rich history and constant evolution, chip removal machining in the CNC era has evolved from a traditional technique to become the foundation of modern manufacturing. At Asimer Group, we take pride in being part of this journey at the forefront of machining and engineering technology.
Our commitment to excellence and innovation drives us to adopt the latest technologies and techniques in chip removal machining. With our expertise in the field of CNC and industrial pumps and valves welding, we strive to deliver top-class engineering solutions that exceed our customers’ expectations.
By embracing emerging technologies, we are positioned to further optimize our machining processes, ensuring greater efficiency and precision in the production of critical components. Additionally, our capability enables us to deliver customized, high-quality solutions for the most demanding needs of our customers.
At Asimer Group, we not only strive for technical excellence but also have a strong commitment to environmental sustainability. We are dedicated to implementing responsible manufacturing practices that minimize our impact on the environment, using technologies and processes that reduce energy consumption and waste generation.
As leaders in the CNC machining and engineering solutions sector, we are ready to face the challenges of the future and continue delivering products and services of the highest quality to our customers.
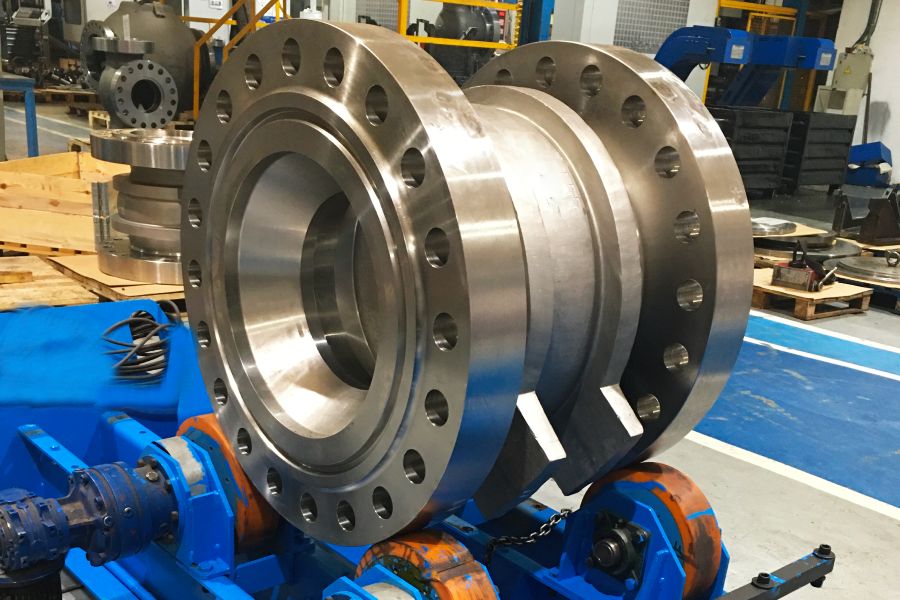