Industry 4.0, with its disruptive innovation, redefines our processes and positions CNC machining as the essential pillar of this industrial evolution. This advanced technology has not only transformed our methods at Asimer Group but has also laid the foundation for a new era of industrial efficiency and creativity.
At the heart of the CNC machining revolution in Industry 4.0, industrial pumps emerge as key players in the optimization and efficiency of processes. These devices, essential for the precise supply of coolant and lubricants in high-tech machining environments, have become the pulsating soul of modern CNC machinery. System interconnection, real-time monitoring, and automatic adjustment capabilities are essential features driven by digitization, enabling smarter and more effective management of industrial pumps. In this context, the synergy between Industry 4.0 and industrial pumps not only redefines manufacturing but also paves the way for a era of more sustainable and precise production.
In Asimer Group, where machining expertise, precision in welding industrial pumps and valves, and custom engineering solutions converge, we delve into the fascinating world of CNC machining. As we explore our approach further, we immerse ourselves in energy efficiency in industrial valves, a key differentiator to optimize industrial operations. In our specialized article on energy efficiency in industrial valves, we examine how these technologies not only enhance operational performance but also significantly reduce energy consumption.
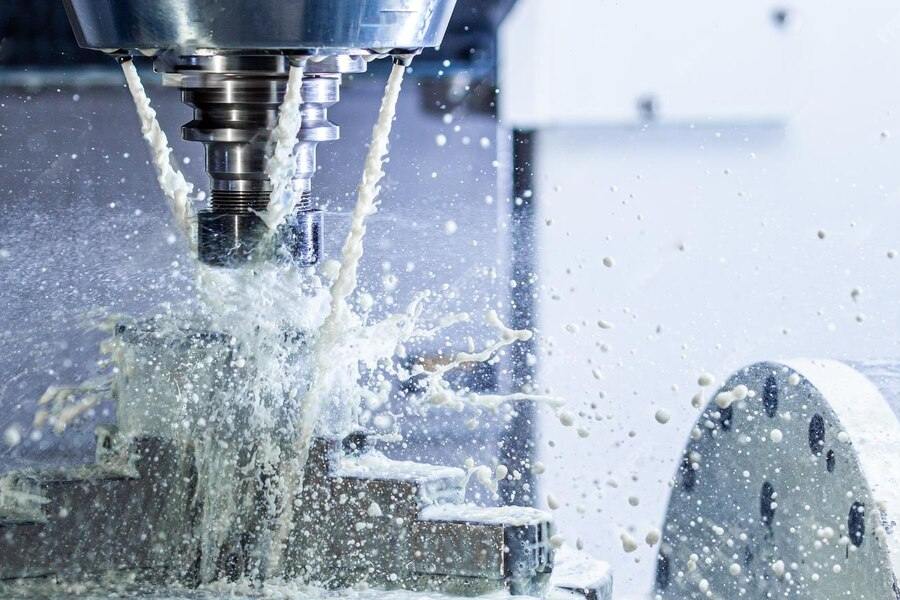
Defining Industry 4.0
Industry 4.0, a revolution redefining the way we conceive and execute industrial production, represents an era of interconnection and digitization. At Asimer Group, we recognize that the true essence of Industry 4.0 goes beyond the mere implementation of advanced technologies; it is about creating intelligent and efficient production ecosystems. In this context, connectivity and real-time data collection are crucial to optimizing processes and improving decision-making.
Industry 4.0 challenges us to integrate operations, from design and production to delivery and maintenance, in a continuous feedback cycle. By strategically implementing CNC machining in this environment, we have achieved a synergy that goes beyond operational efficiency; it is a cultural shift toward constant innovation and adaptability.
Integration in Key Sectors
In Asimer Group, the integration of CNC machining has not only revolutionized our operational capacity but has also left a significant mark in key sectors. From specialized applications in the Oil & Gas industry to solutions for desalination, petrochemicals, cryogenics, naval, paper pulp production, and water and wastewater treatment, our CNC machines have demonstrated exceptional versatility. This strategic approach enables us to offer customized, high-quality solutions in each of these sectors, positioning us as leaders not only in Industry 4.0 but also as drivers of innovation in various industrial areas.
In this context, the revolution of Industry 4.0 and CNC machining emerge as converging forces propelling our company towards a future of excellence and adaptability. By connecting this article with “Chip Removal Machining in the CNC Era,” we can explore how Asimer Group is embracing these technologies to further optimize its manufacturing processes and deliver products of the highest quality. Digitization, automation, and connectivity are the pillars supporting our transformation towards more efficient and precise manufacturing.
In the era of Industry 4.0, automation and digitization are transforming manufacturing, and at Asimer Group, the adoption of CNC technology is a clear example of how the company is embracing this revolution. By exploring how CNC technology is enhancing the petrochemical industry, we can better understand how Asimer Group is at the forefront of this transformation. Dive into this fascinating intersection between Industry 4.0 and petrochemical manufacturing in “CNC Technology: Enhancing the petrochemical industry with efficiency and quality“.
CNC Machining: Beyond Precision
In Asimer Group, we understand that CNC machining accuracy is much more than ensuring millimetric accuracy in every component we produce. It is the backbone of our ability to navigate and thrive in Industry 4.0. Beyond the mere execution of precise operations, our CNC machines act as intelligent nodes in our manufacturing network, providing essential data for strategic decision-making.
Comprehensive automation has become the norm in our production thanks to CNC machining. From computer-aided design (CAD) to quality inspection, each phase of our machining process integrates seamlessly. This not only reduces production times but also minimizes human errors, allowing us to consistently deliver the highest quality products.
Intelligent connectivity is a key component in the symbiotic relationship between CNC machining and Industry 4.0. Every CNC machine in our workshop communicates with each other, sharing real-time data on operation status, production efficiency, and any relevant key performance indicators. This connectivity not only improves operational efficiency but also provides us with a deep insight into our overall performance, allowing real-time adjustments to further optimize our processes.
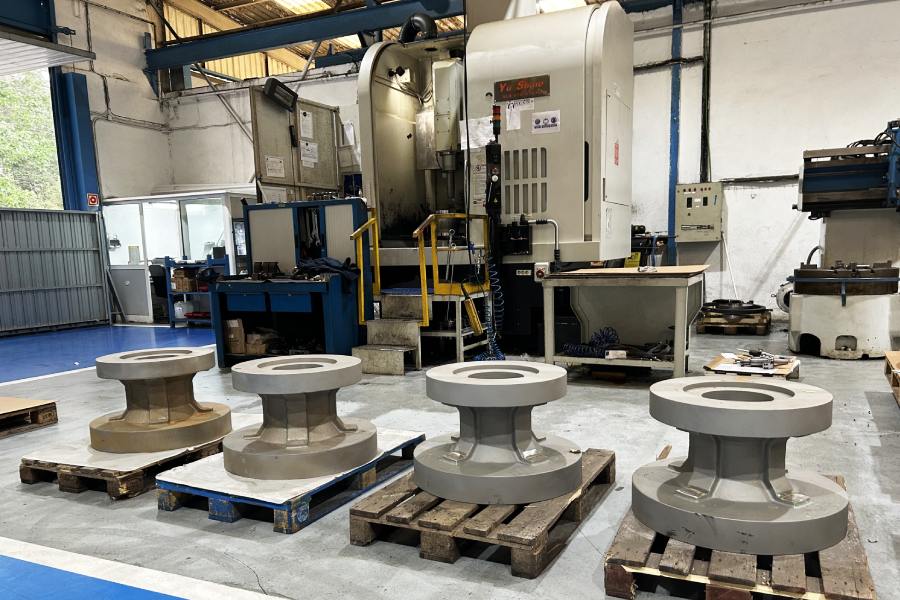
Comprehensive Automation
Comprehensive Automation, as the indisputable cornerstone of the Industry 4.0 Industrial Revolution, unfolds its transformative influence in every corner of our CNC machining operations. In a perfectly orchestrated symphony, from the initial moment of material loading to the meticulous quality control process, automation stands as the bastion that ensures a workflow not only uninterrupted but also endowed with unparalleled efficiency.
This synergistic mesh of automated processes becomes the backbone that supports operational excellence. The mastery of Industry 4.0 is reflected in the total integration of our operations, where each phase, each movement, is executed with millimeter precision thanks to automation. The material loading, far from being a mere initial act, becomes the harmonious prelude to efficient and uninterrupted production.
Quality control, the unyielding pillar in delivering top-rated products, finds in automation its most reliable ally. Each component, each end product, undergoes meticulous scrutiny facilitated by CNC technology and supported by an automated system that knows no rest or errors.
In this crucible of innovation, automation not only simplifies processes but also unleashes a symphony of efficiency that reverberates across the spectrum of our operations. From optimizing cycle times to minimizing waste, every aspect of our production is benefited by automation, culminating in a workflow that redefines the standards of industrial efficiency.
Thus, in this context, Comprehensive Automation is not merely a component but the guiding thread that weaves the fabric of excellence in our CNC machining operations. In its essence, it goes beyond task execution; it is the symphony that elevates our production to a level where efficiency and quality intertwine inextricably.
Intelligent Connectivity
Within the framework of Industry 4.0, where interconnection and digitization define the forefront, the requirement for Smart Connectivity stands as a fundamental imperative, and our CNC machines not only adapt to this demand but enthusiastically embrace it. The ability to monitor and adjust processes in real-time not only translates into a tangible improvement in operational efficiency but also becomes the catalyst for a revolution in decision-making.
The capability of our CNC machines to establish intelligent networking involves more than surface-level connectivity; rather, it is an intricate framework that permeates every aspect of our operations. From real-time data acquisition to instant feedback, each component of our machines contributes to a dynamically unfolding information ecosystem.
This level of connectivity is not merely a means to enhance efficiency but transforms into a key facilitator for informed decision-making. Real-time information from CNC machines becomes an invaluable resource, allowing us not only to react immediately to any deviation or change in the process but also to anticipate and proactively optimize our manufacturing methods.
Enhanced Operational Efficiency
Operational efficiency, the cornerstone and hallmark of Industry 4.0, manifests prominently at Asimer Group, where CNC machining stands as our primary catalyst towards this industrial revolution. Our commitment to process optimization not only redefines standards but also establishes new paradigms in operational excellence.
At the core of our CNC machining operations lies the meticulous reduction of cycle times. Every movement, every operation, is precisely synchronized to eliminate any unnecessary downtime. This synchronization not only streamlines production but also directly translates into time optimization, allowing us to achieve levels of efficiency that not only meet but surpass the expectations of Industry 4.0.
The minimization of waste becomes another fundamental pillar in our relentless pursuit of operational efficiency. Thanks to the precision and adaptability of our CNC machines, we minimize waste to the maximum, ensuring that each material is used optimally. This practice not only aligns with sustainable principles but also contributes to economic efficiency that directly translates into benefits for our clients.
Ensuring continuous production is not just an objective but an unwavering commitment. At Asimer Group, our CNC machining systems are designed to operate without interruption, providing a consistency and reliability that are crucial to meeting the demands of the current market.
Advanced Customization
Advanced Customization, powered by CNC machining, redefines the very concept of tailor-made adaptation at Asimer Group. In this dynamic environment, the capability for mass customization becomes a tangible reality, transforming each project into a unique expression of precision and adaptability.
Our CNC machines not only conform to the specifications of each project but do so with an instantaneous capability that sets a distinctive mark. Immediate adaptability to the exact characteristics of each component or design allows an unprecedented versatility, where every piece produced reflects meticulous attention to detail and a direct response to the specific needs of the customer.
This advanced approach to customization is not just an option but a commitment deeply rooted in our CNC machining process. Each machine becomes a precise tool to sculpt the unique vision of each project, offering customized solutions on a large scale that go beyond mere adaptation: they represent a seamless fusion of advanced technology and craftsmanship.
The synergy between technology and customization manifests at every stage of the process, from conceptualization to the final production. The ability of our CNC machines to address complexities and specific details with efficiency and precision not only ensures the delivery of customized products on a large scale but also raises the standards of excellence in manufacturing.
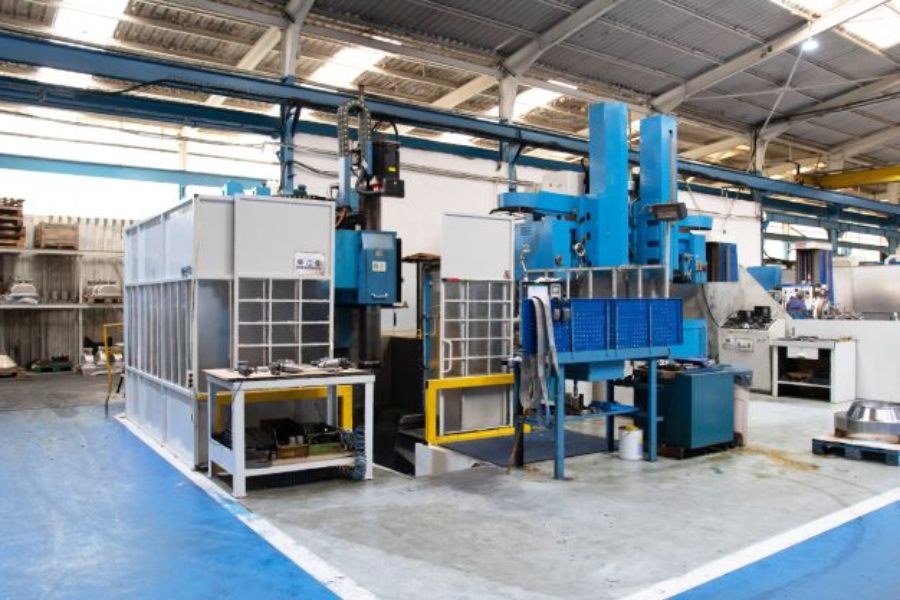
Strategic Investments
The full realization of Industry 4.0 entails not only operational transformation but also the execution of key strategic investments. At Asimer Group, this commitment is emphatically demonstrated through the allocation of substantial resources for the modernization and expansion of our CNC machining infrastructure. These investments are not merely a financial outlay; they represent a proactive vision that propels our adaptability and leadership in an ever-evolving industrial landscape.
The modernization of our CNC machining infrastructure is not just a response to present demands but a strategic anticipation of future needs. Each investment is meticulously directed toward cutting-edge technologies, more efficient systems, and innovative processes. This approach positions us not merely as observers but as active drivers of change, at the forefront of the industrial revolution.
The impact of these investments is directly reflected in a significant increase in production capacity and versatility. Our CNC machines, powered by the latest technologies, not only address current challenges but also anticipate emerging market demands. Adaptability and enhanced versatility are the tangible dividends of our strategic investments, solidifying our position as leaders in delivering advanced manufacturing solutions.
Technological Innovations in Industrial Valve Manufacturing: Discovering the Future at Asimer Group
At the forefront of Industry 4.0, Asimer Group has solidified its position as a leader in CNC machining but has also extended its influence towards key technological innovations in industrial valve manufacturing.
Diving into the fascinating world of CNC machining, we recognize that operational efficiency goes hand in hand with the constant evolution of valve technologies. In our specialized article, we explore how these innovations not only improve precision in each component but also open new perspectives in terms of sustainability and adaptability to current market demands.
Within this innovation context, we highlight needle control valves as the epitome of precision at the heart of the industry. Their role is not only crucial in the precise regulation of fluid flow but also in improving operational efficiency and quality in industrial production.
Sustainability and CNC Machining: Beyond Efficiency
On the path to Industry 4.0, sustainability is not an option; it is an imperative need. At Asimer Group, we recognize our environmental responsibility and view CNC machining as a powerful tool to advance towards more sustainable practices.
Improved operational efficiency through CNC machining not only results in shorter production times and higher quality products but also reduces our environmental impact. Process optimization decreases energy consumption and minimizes waste, aligning us with stricter sustainability standards.
The Trevisan Machining Center at Asimer Group stands as the fundamental pillar for advanced engineering solutions. Our CNC machining technology, backed by the Trevisan Machining Center, not only ensures millimetric precision in every component but also drives operational efficiency at the heart of Industry 4.0.
Additionally, we embark on specific initiatives to integrate sustainable practices into our CNC machining processes. This includes exploring more eco-friendly materials, adopting advanced recycling technologies, and continuously optimizing our production methods to minimize the carbon footprint.
In summary, sustainability in CNC machining goes beyond operational efficiency; it involves a comprehensive commitment to practices that preserve our environment. At Asimer Group, we are not only embracing Industry 4.0; we are leading the way towards a future where innovation and sustainability converge in every CNC machining operation.
Conclusions
At Asimer Group, CNC machining is not just a tool; it is the epicenter of our transformation towards Industry 4.0. Intelligent connectivity, comprehensive automation, and tangible benefits in production are testimonies to how this technology redefines our standards of efficiency and quality. As we move towards the future, we are committed to remaining leaders in the innovative adoption and application of CNC machining in our constant pursuit of industrial excellence.