What are industrial valves?
Industrial valves are a device that regulates the flow of a fluid (gasses, liquids, solids) by opening, closing or partially obstructing various passages. Industrial valves are used to handle high pressure, either fluid or gas, and to last years of use in hostile environments.
Valves are mechanical devices that control the flow and pressure within a system or process. They are essential components of a pipeline system that transports liquids, gases, vapors, sludge, etc. Outside the home, industrial valves are built to control processes. Most utilities, from water to oil & gas, would not be able to operate without high industrial resistance valves. In the broad field of industrial valves, it is crucial to understand the different types of valves and their applications in various industries. These valves play a key role in controlling fluid flow and preventing leakage in piping systems. However, to ensure safe and efficient operation, it is essential to consider the contribution of fittings in improving tightness. Fittings, combined with appropriate valves, help prevent leaks and maintain system integrity in the oil gas sector. Our article on “Types of industrial valves and their applications” provides a detailed overview of the different types of valves used in various industrial applications. For more information on how to prevent leaks and improve tightness thanks to fittings in the oil and gas sector, we invite you to read our full article. Well, now that we know the importance of industrial valves, we will know their different types, characteristics and applications.
Why are industrial valves important?
Industrial valves are critical components in a wide variety of industrial processes, and their importance lies in their ability to control the flow of fluids, gasses, and other materials in piping systems. These valves are essential to ensure the safe and efficient operation of a wide range of processes, from food and beverage production to oil and gas production, and many other applications in the chemical, pharmaceutical, and general manufacturing industries, including cryogenic applications. Industrial valves also help prevent leaks, reduce energy consumption, and protect critical equipment in production facilities, contributing to worker safety and environmental sustainability in industrial operations.
Impact of Industry 4.0 and the CNC Machining Revolution
Currently, Industry 4.0 and the CNC Machining Revolution are radically transforming the manufacturing of industrial valves. These technological advancements have enabled greater automation, precision, and efficiency in valve production, resulting in significant benefits for various industries. From optimizing manufacturing processes to product customization and reducing delivery times, the integration of Industry 4.0 and CNC Machining is revolutionizing the industrial landscape.
The incorporation of emerging technologies such as artificial intelligence and machine learning further enhances efficiency and precision in the manufacturing of industrial valves. With real-time monitoring systems and predictive analytics, companies can optimize production, anticipate potential failures, and enhance the reliability of their products.
This approach towards intelligent manufacturing not only promises to further revolutionize the industry but also opens new opportunities for innovation and global competitiveness, while addressing emerging challenges in sustainability and energy efficiency.
Types of Industrial Valves.
Fluid Control Valves.
- Globe valves
This type of valve is commonly used in flow and pressure regulation applications, as it allows the precise adjustment of the amount of liquid or gas flowing through it by opening or closing a shutter that moves up or down in a seat.
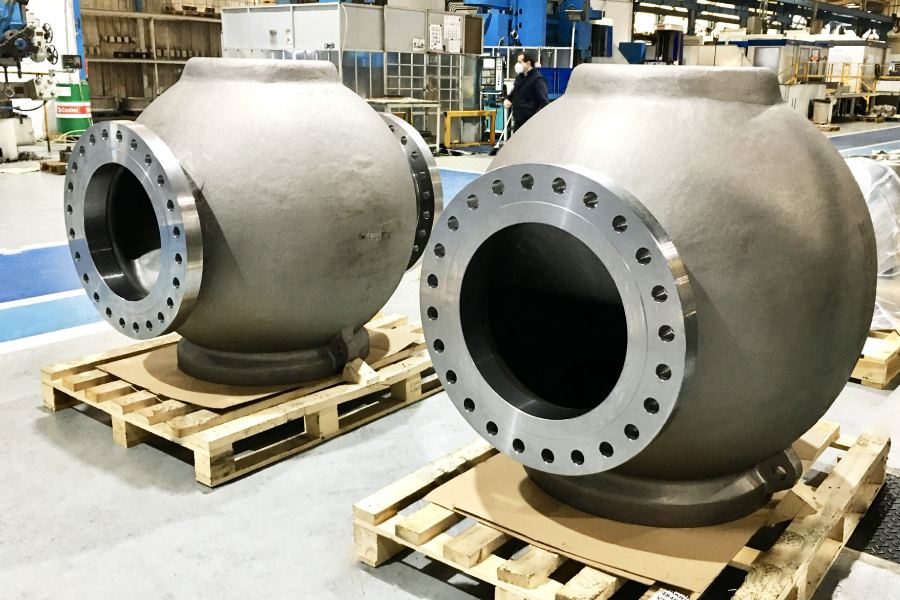
- Gate valves
These valves are used to control flow in large-diameter pipes and are ideal for on/off applications as they allow for full opening or complete shut off of flow.
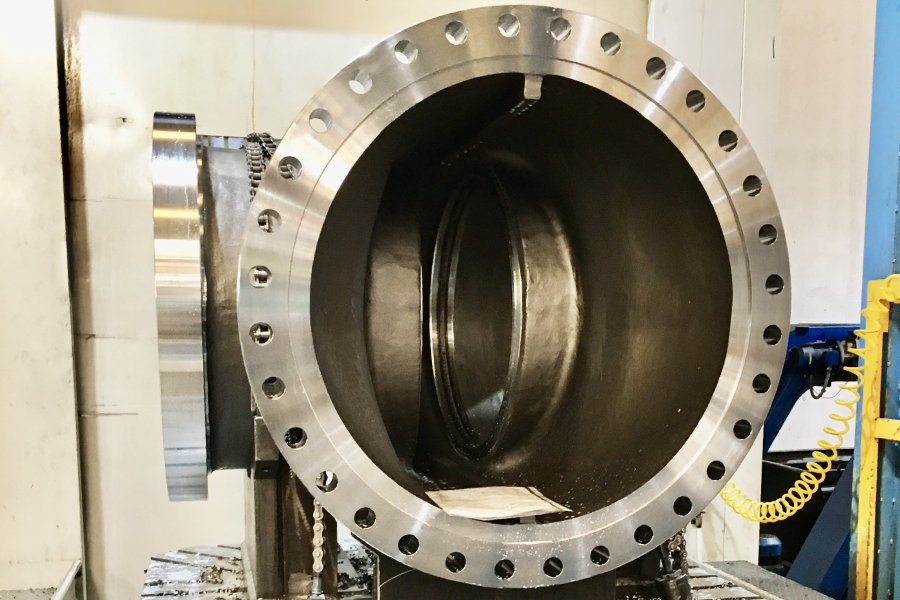
- Butterfly valves
Butterfly valves are a popular choice for bulk liquid flow control applications due to their simple and lightweight design, which allows them to operate with minimal pressure loss.
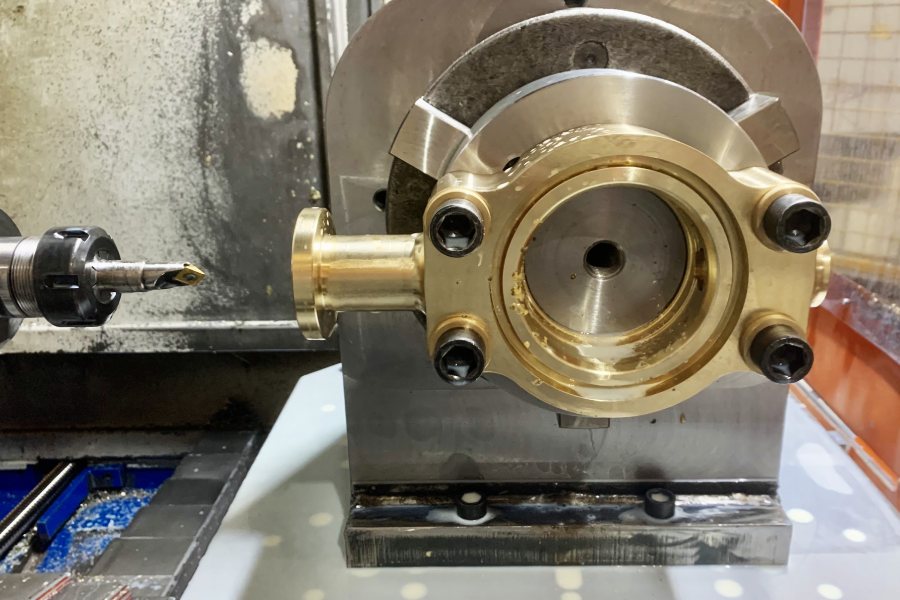
These valves use a flexible diaphragm to control flow. The diaphragm deforms when pressure is applied and recovers when the pressure is released, allowing flow.
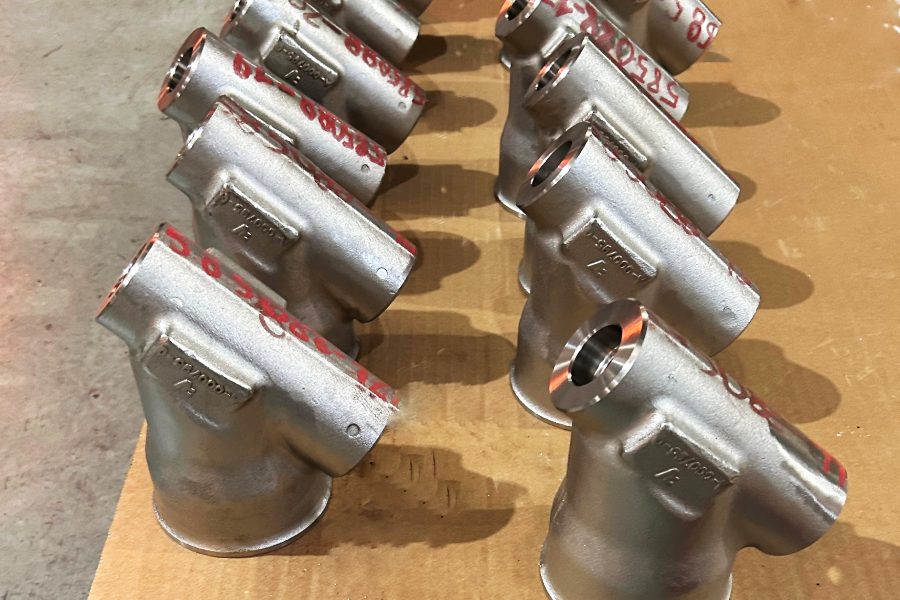
- Needle valves
Needle control valves are used for high precision applications where very precise flow control is needed. The valve shutter has a tapered tip that fits into a seat to allow precise flow control.
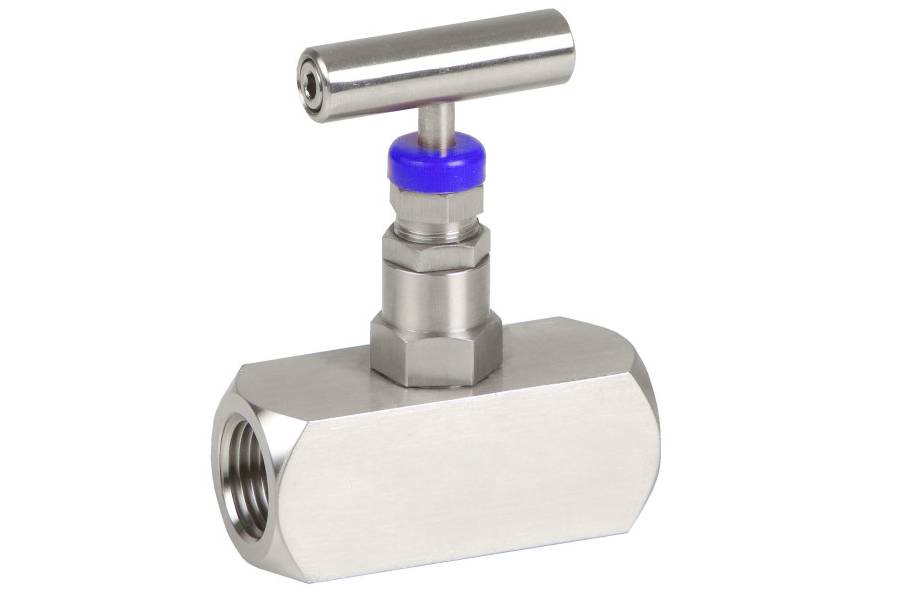
Check Valves.
The main check valves (also known as one-way valves) used in industrial applications are:
- Check valves with flap
This is the most common check valve. It is composed of a plate or flap that opens in one direction to allow flow and closes to prevent flow from returning in the opposite direction. They are used in low to medium pressure applications and are ideal for liquids and gasses.
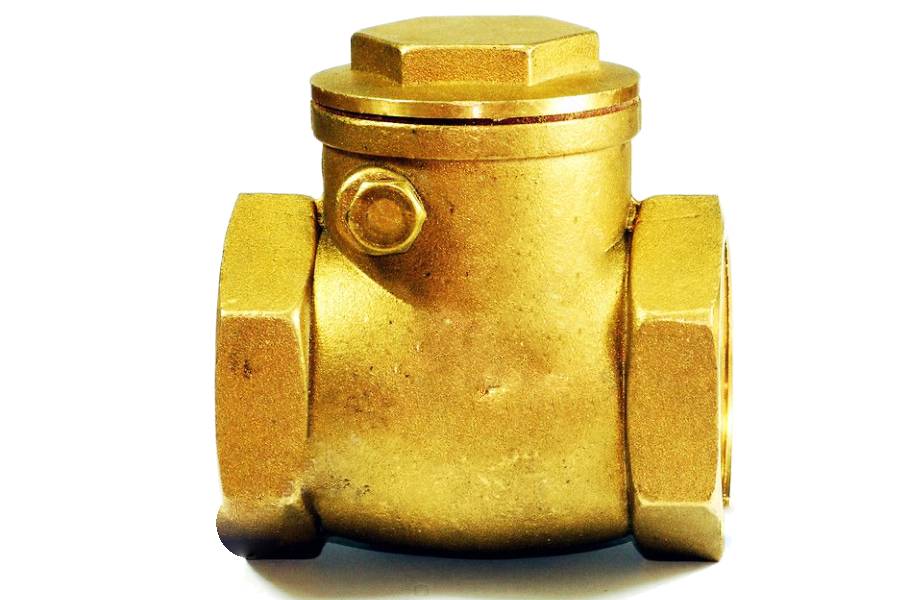
- Ball check valves
In this type of valve, a ball moves up and down in a seat to allow or prevent flow. When the flow is in the correct direction, the ball moves up and allows the liquid or gas to pass through the valve. If the flow changes direction, the ball drops into the seat and closes the valve.
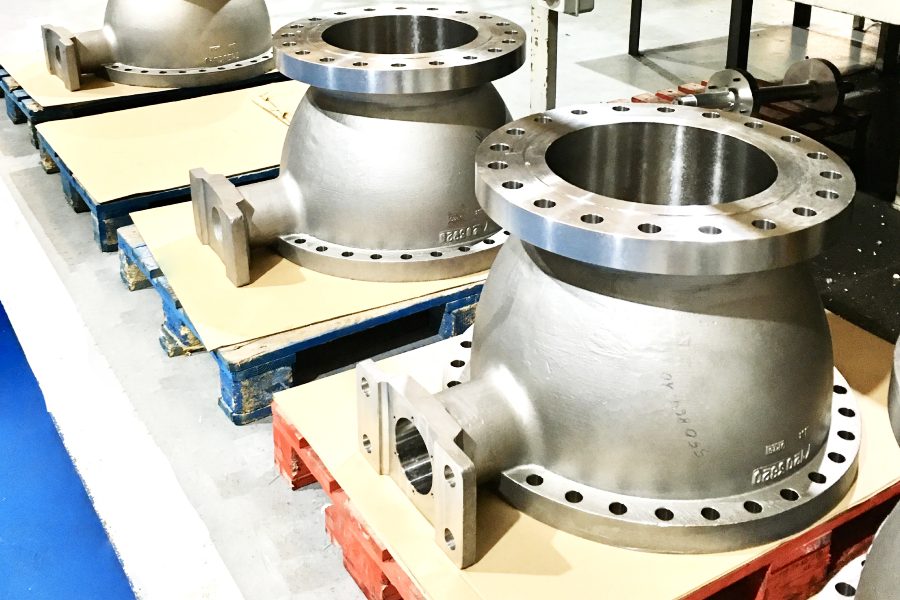
- Swing check valves
This type of valve uses a disc or flap suspended from a shaft to allow flow in one direction and prevent flow in the opposite direction. When flow is in the correct direction, the disc moves up and opens to allow fluid passage. When the flow changes direction, gravity causes the disc to close and seal the valve.
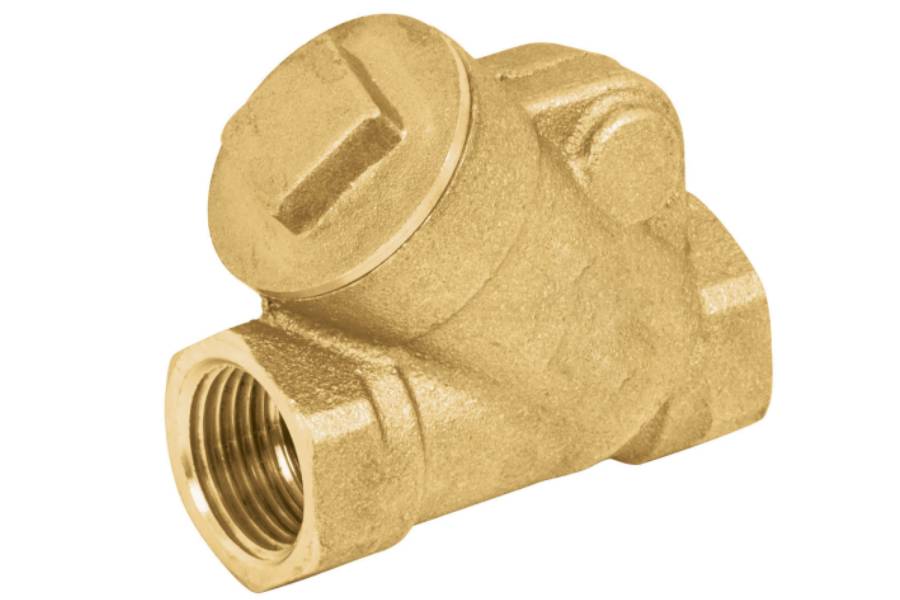
Relief Valves.
- Safety Valves
These valves are used to protect equipment and systems against overpressure. They automatically open when the fluid pressure exceeds a certain level, releasing excess pressure and protecting the equipment and pipes from possible damage.
- Pressure Relief Valves
This type of valve is used to control the pressure in a system and prevent it from exceeding a pre-established limit. If the pressure reaches a dangerous level, the valve opens and allows the excess pressure to escape.
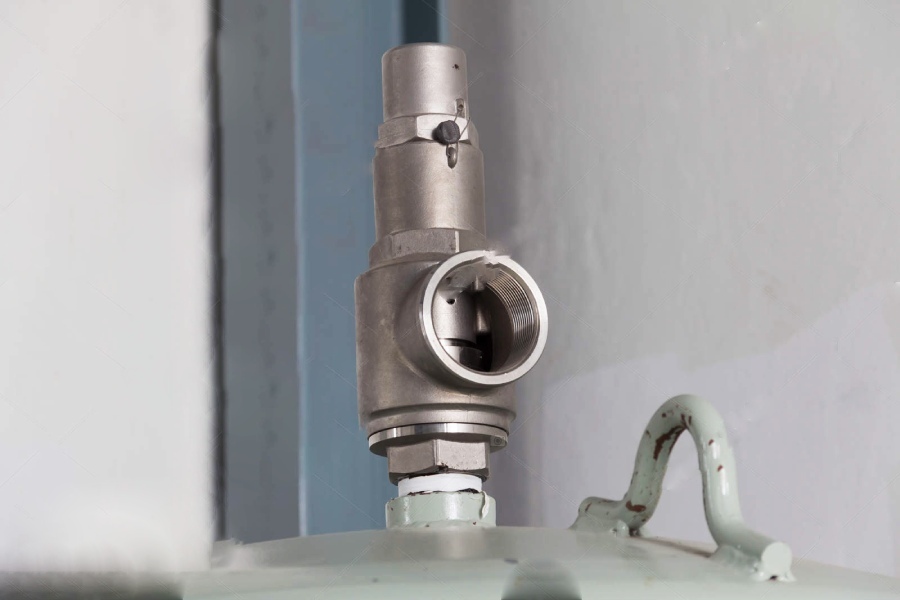
- Vacuum Relief Valves
These valves are used to prevent vacuum formation in a system. They automatically open to allow air to enter the system when the pressure drops below a certain level.
- Differential Pressure Relief Valves
This type of valve is used to control the differential pressure between two points in a system. If the differential pressure reaches a dangerous level, the valve opens to allow the excess pressure to be relieved.
It is important to note that the choice of the appropriate relief valve will depend on the specific application and operating conditions, such as pressure, fluid type, and temperature. In addition, it is crucial that relief valves are maintained and regularly tested to ensure their proper operation in case of emergency.
Applications of Industrial Valves.
Industrial valves are essential devices in a wide variety of applications in industry, including petrochemicals, food, pharmaceuticals, water and sanitation. In each of these industries, valves play an important role in process control and in preventing accidents and environmental risks.
Valves in the Petrochemical Industry.
In the petrochemical industry, industrial valves are used to control the flow of liquids and gasses in critical processes, such as oil refining and chemical production. Ball, gate, and globe valves are some of the most common in the petrochemical industry due to their ability to withstand high pressures and temperatures.
Valves in the Food Industry.
In the food industry, industrial valves are used to control the flow of ingredients and products, from liquids to gasses, in processes such as the production of beverages and packaged foods. Butterfly, ball, and diaphragm valves are some of the most common in the food industry due to their ability to withstand hygienic environments and resist corrosion.
Valves in the Pharmaceutical Industry.
In the pharmaceutical industry, industrial valves are used to control the flow of liquids and gasses in critical processes, such as the manufacture of medicines and biological products. Diaphragm, ball, and needle valves are some of the most common in the pharmaceutical industry due to their ability to withstand sterile environments and resist corrosion.
Valves in the Water and Wastewater Industry.
In the water and sanitation industry, industrial valves are essential for controlling pressure and flow in water supply and treatment systems, as well as in the treatment of wastewater. Gate, globe, and check valves are some of the most common in the water and sanitation industry due to their ability to withstand high pressures and resist corrosion.
In summary, industrial valves are essential in a wide variety of applications in industry, including petrochemicals, food, pharmaceuticals, water and sanitation. These valves play a crucial role in process control and in preventing accidents and environmental risks.
Types of Industrial Valves in Asimer Group.
Over the last 14 years, Asimer Group has worked with the technical department of its most important clients in the development of various types of fluid control valves, such as gate, globe, ball, check, plug, and butterfly valves. These valves have been designed to improve efficiency and safety, reduce costs, and automate processes. Thanks to our high-precision machining tools and computer numerical control (CNC) systems, we have been able to produce highly accurate valves and complexes with very tight tolerances. Additionally, our Machining Deparment use rigorous inspection and testing techniques to ensure that our valves meet the necessary quality and safety standards for use in critical environments.
Our technical office, backed by our experience, constantly seeks new solutions to facilitate and improve existing designs, allowing us to offer our customers customized projects tailored to their needs.
Asimer Group is also specialized in the machining of industrial pumps, such as cryogenic pumps or centrifugal pumps.