The pump and valve manufacturing transformation has become imperative in the industry, where the constant pursuit of efficiency and precision has found CNC machining (Computer Numerical Control) to be a fundamental tool for the evolution of key processes. Industrial valves and pumps, crucial elements in various processes, experience significant improvement in their precise and efficient production through the specific applications of CNC machining.
In the fascinating world of industrial pump and valve manufacturing transformation. through CNC machining, precision and quality are crucial elements that converge in the metrology and quality inspection room. In this room, meticulousness reaches its highest expression, where each component undergoes rigorous measurements and evaluations to ensure the most demanding standards.
In the dynamic world of pump and valve manufacturing, the transformation driven by engineering solutions has been remarkable, especially with the widespread use of CNC machining. This technological advancement has revolutionized the way various critical applications are addressed in diverse sectors such as oil and gas, petrochemicals, naval industry, water and wastewater treatment, paper mill production, cryogenics, and desalination.
It’s important to highlight that “Technological Innovations in Industrial Valve Manufacturing” are revolutionizing CNC machining processes. Discover how these innovations are redefining precision, quality, and efficiency in the production of vital components for the industry.
Axial flow check valves represent a notable innovation in the evolution of CNC machining applications in the field of pumps and valves. These valves, with their precise design and the ability to regulate flow in specific directions, have significantly transformed efficiency in a variety of sectors, from petrochemicals to the naval industry. Through CNC machining, precise production of intricate components essential for the optimal functioning of these valves in challenging environments is achieved. The application of this machining has allowed adapting axial flow check valves to various conditions, from handling corrosive liquids in the chemical industry to efficiently pumping viscous fluids in the petroleum sector. In the context of the technological revolution in pump and valve manufacturing, axial flow check valves stand out as a tangible example of how CNC machining is shaping specific solutions that enhance functionality and durability in critical applications.
This article delves further into these aspects, expanding the discussion to provide a more comprehensive view of the revolution that this technology has brought to pump and valve manufacturing.
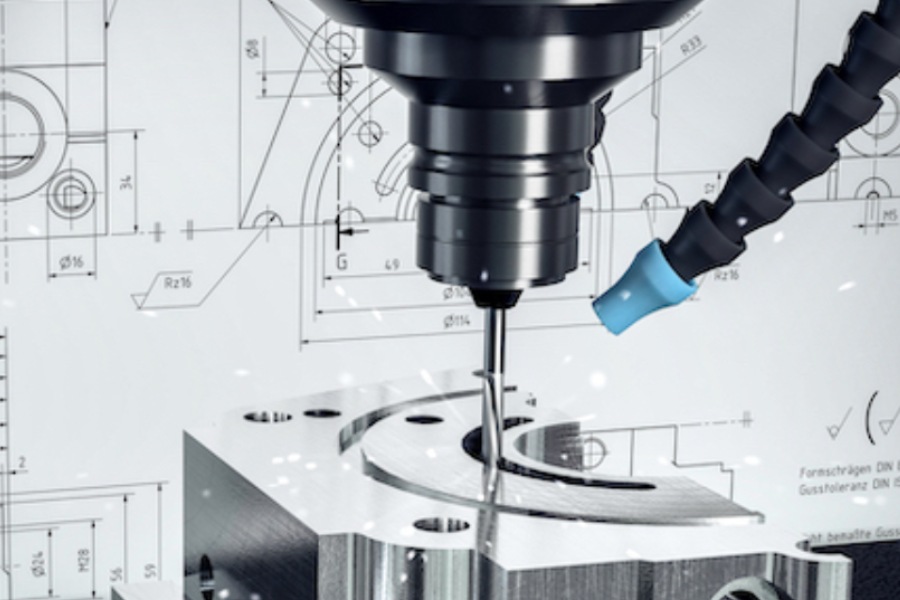
Applications of CNC Machining in Pumps and Valves: Specific Details
Critical Valve Components:
In the production of industrial valves, the precision of components is of utmost importance to ensure reliable performance. CNC machining stands out by enabling the creation of critical components with extremely tight tolerances. A prominent example is the manufacturing of flow control valves used in the chemical industry. These valves require millimeter precision to accurately regulate the flow of corrosive liquids. CNC machining allows the production of intricate parts with specific shapes, ensuring optimal performance and a long lifespan in challenging chemical environments.
Optimized Pumps Casing:
Optimizing pumps casing is essential to adapt to specific challenges in different industries. In the petroleum sector, for example, pumping viscous fluids presents unique challenges. CNC machining enables the creation of housings with more complex geometries to improve pumping efficiency. These optimized designs effectively confront the resistance of viscous fluids, thus enhancing the overall efficiency of the pumping system in critical petroleum environments.
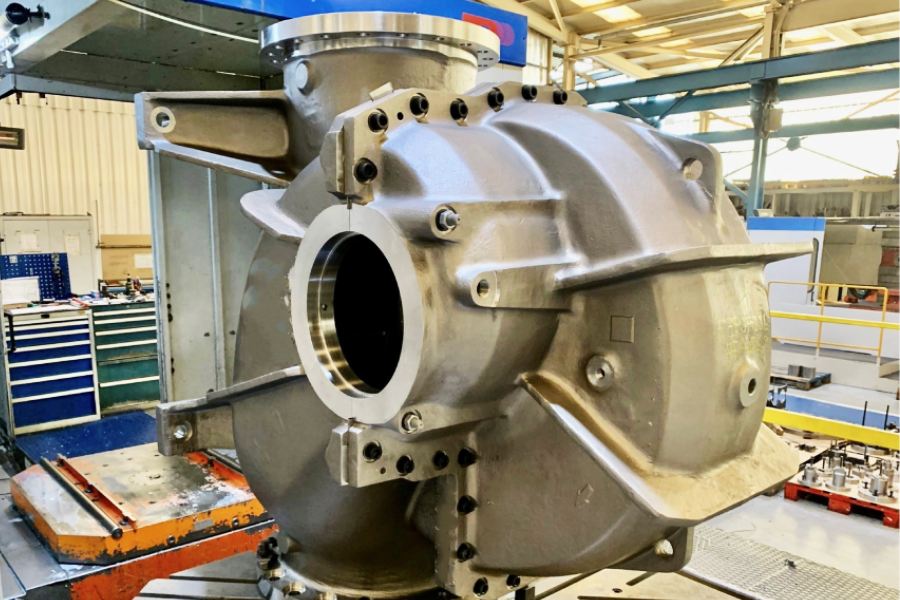
Precise Threading and Drilling Processes:
In the manufacturing of valves for high-pressure hydraulic systems, threading and drilling operations are crucial. Here, CNC machining plays a prominent role in ensuring extremely precise processes. Take, for example, valves used in aerospace hydraulic systems, where every thread and hole must meet rigorous tolerances. CNC machining offers the ability to perform these operations with micrometer precision, ensuring secure and efficient connections in critical environments where structural integrity is fundamental.
Rapid Prototyping for Continuous Innovation:
In the design of centrifugal pumps for specific industrial applications, rapid prototyping is essential for continuous innovation. Thanks to CNC machining, manufacturers can create prototypes in record time, accelerating the development process. For example, when designing a centrifugal pump for the efficient handling of corrosive fluids in the chemical industry, engineers can iterate quickly on different designs. This not only speeds up time to market but also allows for continuous optimization, improving the efficiency and reliability of the final product.
Unique Challenges and Benefits of CNC Machining in Pumps and Valves
The implementation of CNC machining in pump and valve manufacturing presents a series of challenges and benefits that are crucial to understanding how this technology truly transforms these industrial processes. Below are some specific aspects that illustrate the challenges overcome and tangible benefits provided by CNC machining.
Challenges Overcome: Manufacturing Intricate Components for Industrial Cooling Gear Pumps
The manufacturing of gear pumps used in industrial cooling systems presents significant challenges due to the complexity of designs and intricate shapes of components. CNC machining has overcome this challenge by enabling the production of gears, rotors, and other parts with highly complex shapes.
Practical examples include the precise creation of toothed rotors that ensure efficient coolant flow and optimal cooling in critical industrial environments.
Tangible Benefits: Reduction of Errors in the Production of Ball Valves for Cryogenic Applications
In the production of ball valves for cryogenic applications, where extremely low temperatures are encountered, precision is crucial to avoid leaks and ensure reliable performance.
CNC machining has demonstrated tangible benefits by significantly reducing errors in production. In a specific case study, the implementation of CNC machining in the production of cryogenic valves resulted in a 30% decrease in surface imperfections, improving the quality and efficiency of the production process.
In the world of industrial pumps and valves, precision and reliability are fundamental. CNC machining has revolutionized the way these components are manufactured, allowing for greater precision and efficiency at every step of the process. By connecting this article with “Chip Removal Machining in the CNC Era,” we can explore how this technology is transforming the manufacturing of pumps and valves, optimizing their performance and durability in a variety of industrial applications.
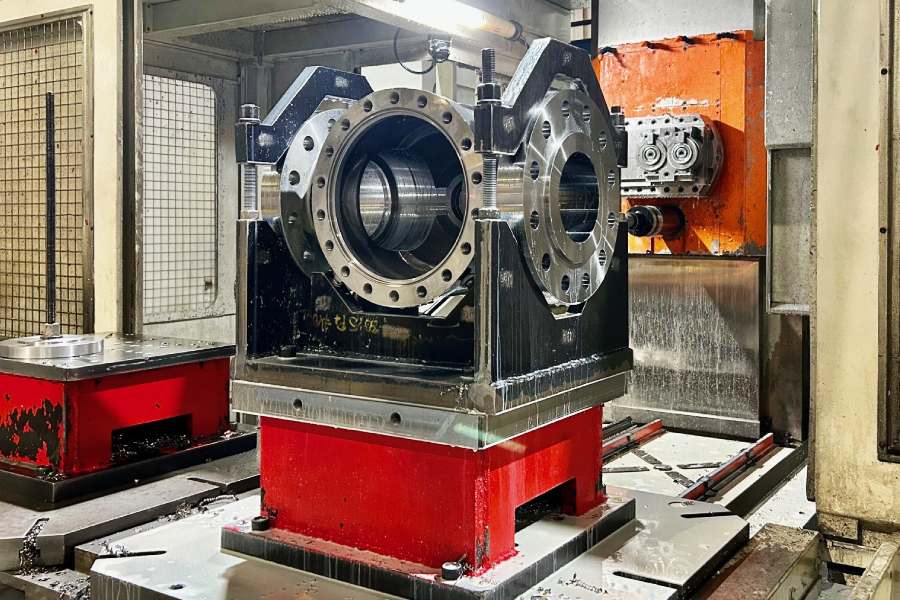
Additional Innovations with CNC Machining
Integrated Monitoring Systems: Improving Consistency in Chemical Dosing for Metering Pumps
The integration of advanced monitoring systems has reached new heights in the manufacturing of metering pumps. This innovation has already transformed operational efficiency. In a chemical processing plant, the implementation of real-time monitoring systems has revolutionized the precise dosing of chemicals. Sensors connected to CNC machines continuously monitor the amount of dosed chemicals, automatically adjusting parameters to maintain exceptional consistency. This practical application has drastically reduced dosing errors, improving product quality and reducing waste.
Application of Advanced Materials: The Revolution of Titanium Alloys in Valves for Highly Corrosive Environments
The use of advanced materials, such as titanium alloys, is essential in highly corrosive environments. CNC machining facilitates the application of these alloys in valve manufacturing to ensure exceptional corrosion resistance.
For example, in the production of valves for chemical plants, CNC machining has allowed the creation of titanium components with tight tolerances, enhancing chemical resistance and prolonging the life of valves in corrosive environments.
Environmental Impact of Modern Pump and Valve Manufacturing
Today, sustainability has become imperative in modern manufacturing, and CNC machining plays a prominent role in contributing to more eco-friendly practices.
Accuracy in CNC machining has led to a notable reduction in waste, thanks to the increased accuracy achieved in the production process. In a centrifugal pump manufacturing plant, the implementation of CNC machines has allowed the carving of components with tight tolerances, minimizing discarded materials. This directly translates into a decrease in waste, promoting more sustainable practices and reducing the negative environmental impact associated with traditional manufacturing.
Additionally, CNC machining’s ability to work with a wide range of materials has fostered the efficient use of resources. In the manufacturing of valves for industrial applications, where strength and durability are crucial, CNC allows the precise use of advanced materials. For example, the adoption of lightweight yet strong alloys in valve manufacturing has led to a significant reduction in material consumption compared to conventional manufacturing methods.
Environmentally friendly practices also extend to the energy used in CNC machining processes. Efficient programming and tool optimization enable a reduction in energy consumption. In a high-efficiency pump factory, smart CNC machine programming has resulted in a 15% decrease in total energy consumption during production. These efficiencies not only result in economic savings but also reflect a commitment to environmental sustainability.
In summary, CNC machining has not only transformed manufacturing in terms of precision and efficiency but has also paved the way for more sustainable practices that are making a positive impact on the environment, marking a significant step toward a more sustainable future in the pump and valve industry.
Future Perspectives: Automation and Digitalized Manufacturing
In the dynamic landscape of Pump and Valve Manufacturing Transformation through CNC Machining, a key adoption is the implementation of Industry 4.0 and the CNC machining revolution. Industrial engineering, a leader in this field, has fully embraced Industry 4.0 technologies, incorporating intelligent systems, advanced data analytics, and automation into its CNC machining approach.
The constant evolution of CNC machining is manifested in trends that clearly point towards automation and digitalized manufacturing in pump and valve production. Specific developments, such as additive manufacturing and the integration of robots into CNC machining processes, are shaping both the present and the future of this sector.
Currently, additive manufacturing is no longer a mere future promise but a tangible reality. In the production of components for high-efficiency pumps, 3D printing has merged with CNC machining to create complex structures and optimized geometries. This not only provides greater flexibility in design but also reduces production times and minimizes material waste by printing only what is necessary.
The integration of robots into CNC machining processes has evolved from being a vision to a common practice in many manufacturing facilities. For example, in the precision valve production, collaborative robots work together with CNC machines for specific tasks, such as loading and unloading parts. This approach has improved operational efficiency while freeing human operators for more specialized tasks, creating a more agile and cost-effective manufacturing environment.
Digital connectivity is also transforming manufacturing, allowing remote monitoring and real-time adjustment of CNC machining processes. In a smart pump factory, digitalized manufacturing involves the use of sensors connected to the network to collect real-time data on the performance of CNC machines. This facilitates early identification of potential problems and allows instant adjustments to optimize production and reduce downtime.
Current perspectives on automation and digitalized manufacturing are palpably transforming the pump and valve industry. Concrete examples demonstrate that these trends are more than mere future concepts, outlining a present where the combination of CNC machining, additive manufacturing, and robotics is shaping an innovative and efficient landscape in industrial manufacturing.
Conclusions and Current Perspectives for the Pump and Valve Industry
Upon concluding this extensive analysis, it is clear that CNC machining already plays a central and transformative role in the current manufacturing of pumps and valves.
- Transformation Driven by CNC Machining and Advances in Industrial Valve Manufacturing
The transformation driven by CNC machining is already underway in the pump and valve industry. In this dynamic scenario, technological innovations in industrial valve manufacturing play a central role in the ongoing evolution of key processes.
- Technological Innovations in Industrial Valve Manufacturing: Advances Redefining Efficiency and Reliability
These innovations, supported by advances such as CNC machining and the integration of Industry 4.0 technologies, are revolutionizing the efficiency, precision, and versatility of valves in various industries. From the implementation of advanced materials to the application of integrated monitoring systems, industrial valve manufacturing is undergoing a transformation led by cutting-edge engineering.
- Future Trends and Widespread Adoption of Advanced Technologies in the Industry
Global perspectives indicate a continued path toward the widespread adoption of advanced technologies in the industry. In the manufacturing of pumps for renewable energy systems, the current trend is towards the use of lighter and more efficient materials. The combination of computer-aided design (CAD) with CNC machining has allowed the creation of more aerodynamic and robust components, contributing directly to the transition to more sustainable energy sources.
- Adaptation to Technological Changes in Leading Companies
The need to adapt to technological changes is evident in leading companies that have implemented remote monitoring and real-time data analytics systems. In a smart pump factory, the ability to collect and analyze real-time operational data has allowed proactive adjustments, improving efficiency and reducing maintenance costs.
- General Conclusion
In summary, current conclusions reflect that the transformation driven by CNC machining is already underway in the pump and valve industry. Companies that adopt and leverage these advanced technologies not only enhance their current competitiveness but also lay the foundation for a sustainable and efficient future in industrial manufacturing.