The valve is an essential component in a wide range of industrial applications. It is responsible for regulating the flow of liquids, gases, and other mediums in critical systems. However, to ensure its proper operation and safety in processes, rigorous testing is essential. This is especially relevant in the case of needle control valves, where precision and reliability are crucial in the industry.
The importance of valve testing lies in the safety and efficiency of the process, and CNC machining plays a vital role in the creation of high-quality valves. This process ensures that each valve is machined with precision, optimizing its performance and reliability.
In the intriguing universe of industrial valves, where precision and efficiency are like the pulsating heart, it is essential to understand how technology is turning every corner of our industry. Industry 4.0 and the CNC Machining Revolution are like a breath of fresh air that not only redefines the way we manufacture but also leaves its mark on the quality and performance of valves. Imagine a scenario where valve testing is more than simple processes; it is part of a revolution. In this context, the influence of Industry 4.0 and the CNC Machining Revolution emerges as a significant milestone, marking a shift towards excellence in the manufacturing and testing of these essential components that pulse at the heart of industrial engineering.
What is a valve and where are valves used in industry?
A valve is an application/product that controls the movement of a fluid or gas.It manages the direction and/or controls the flow of a fluid or gas by opening and closing one or more steps.
Valves play a vital role in most industries involving pipelines or other applications, including the cryogenic sector. In the cryogenic sector, cryogenic applications are used for the production and handling of gases at very low temperatures, and cryogenic valves are crucial for the proper functioning of equipment in this industry. In addition, other industrial sectors such as the Oil & Gas Sector, the Petrochemical Sector, the Naval Sector and the Desalination Sector also use industrial valves in their operations. These sectors recognize the importance of valves to control the flow of fluids in pipelines and ensure safe and efficient operation of systems. In the oil and gas sector, for example, valves play a key role in preventing leakage and improving tightness. For more information on how to prevent leaks and improve tightness thanks to fittings in the oil and gas sector, we invite you to read our article dedicated to this topic. Click here for the full article on “How to prevent leaks and improve tightness thanks to fittings in the oil and gas sector“.
Types of industrial valves
There are six main types of valves used in industrial applications: globe valves, gate valves, ball valves, butterfly valves, check valves, and plug valves. Each has a specific design tailored to flow, pressure, and fluid type requirements, which determines its suitability for sectors such as petrochemicals, energy, marine, or water treatment.
In demanding industrial environments, such as Oil & Gas or power generation, robust components manufactured with tight tolerances are required. The machining of large-size valves becomes a key process to ensure operational reliability, leak-tightness, and precise integration into complex systems. This is one of Asimer Group’s specialties, with the technology and expertise needed to meet the technical challenges of this type of valve.
What are the main parts of a valve and how do they work?
Valves are fundamental components in fluid handling systems, as they allow for the regulation, opening, closing, or diversion of liquid and gas flow according to the process requirements. To understand how they work, it’s essential to know their main structural elements.
- Body
This is the main housing of the valve and constitutes its external structure. It withstands system pressure and connects to the pipeline. It can have different configurations depending on the valve type (spherical, cylindrical, angular, etc.) and is usually made of carbon steel, stainless steel, bronze, or other materials depending on the working environment. - Obturator or Disc
This is the movable component that regulates the fluid flow. Its design varies depending on the valve type: it can be a ball (ball valve), a cone (globe valve), a flat gate (gate valve), or a rotating disc (butterfly valve). The disc is actuated by a rod or shaft, and its movement allows the flow to be modulated, blocked, or permitted. - Seat
This is the surface on which the disc rests when the valve is closed. It must ensure tight sealing and resist wear caused by fluid friction. Seats can be metallic, soft (Teflon, EPDM), or coated, depending on the service type. - Stem or Shaft
It transmits motion from the actuation mechanism (manual, pneumatic, hydraulic, or electric) to the disc. It can be rising or non-rising and must ensure smooth and precise movement. - Bonnet
This is the upper part of the body, allowing access to the valve interior for maintenance. It seals the assembly using packing or O-rings and may include a gland follower. - Gaskets and Seals
These ensure sealing between the different parts of the valve, preventing both external and internal leaks. Their material and design must be compatible with the fluid and the operating conditions (pressure, temperature, and chemical composition).
It’s important to note that the configuration and number of components may vary depending on the valve type and its specific industrial application.
For example, the operation of a butterfly valve is based on a rotating disc that turns around a central axis. By rotating 90 degrees, this disc becomes either parallel or perpendicular to the flow, allowing the fluid to pass or be blocked. Its compact design, low cost, and ease of maintenance make it a widely used option in water networks, compressed air systems, chemical processes, and ventilation systems.
the efficiency and safety of the system in which they are used.
Valves machined and tested by Asimer Group
Thanks to its extensive experience in the industrial sector, Asimer Group works with a wide range of valves tailored to different processes and industries. Among the most common types are:
- Gate valves
- Globe valves
- Ball valves
- Check valves
- Plug valves
- Butterfly valves
- Axial flow valves
Each valve type meets specific technical requirements depending on flow rate, pressure, fluid type, and operating environment. This multi-technology approach allows Asimer to support a wide variety of sectors, from water treatment to power generation.
Valves used in the Oil & Gas sector require not only advanced materials but also high-precision machining processes for the Oil & Gas industry, ensuring tight tolerances, leak-tightness, and reliability under extreme pressure and temperature conditions. Asimer Group is equipped with state-of-the-art machining centers and specialized technical staff to meet these demands with precision and efficiency.
In addition, thanks to its production capacity and optimized management, the company can optimize costs in the machining of pumps and valves without compromising quality or technical standards. This efficiency is essential in large-scale projects, where deadlines and traceability are critical.
It is also worth noting that some of the sectors served require large-size valves, such as the naval, petrochemical, or steam generation industries. Supporting sectors that use large valves involves mastering complex processes of manufacturing, handling, and dimensional verification—an area in which Asimer excels.
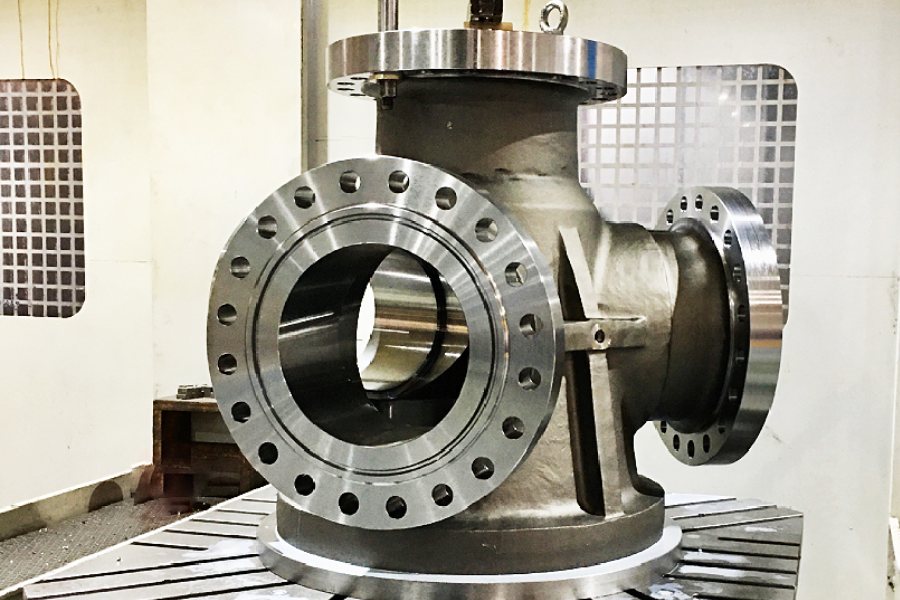
Why valve testing matters in industrial systems
In the field of industrial valves, it is essential for these components to operate safely, reliably, and precisely, ensuring effective pressure regulation without leaks. In high-pressure systems, a failure can lead to critical leaks, explosions, or unexpected shutdowns—posing operational risks and causing significant economic losses. For this reason, maintaining the functional integrity of valves is a top priority in any industrial environment.
To ensure such reliability, various types of non-destructive testing (NDT) are applied, such as industrial radiography, ultrasound, magnetic particle inspection, or liquid penetrant testing. These techniques help identify internal or surface defects without compromising the valve’s structure, ensuring the component can safely operate under real service conditions. In particular, liquid penetrant testing is a key tool for detecting cracks or porosity on critical metallic surfaces, such as seats or welded areas.
Pressure testing is also part of the standard protocol to validate a valve’s performance. Whether through hydrostatic or pneumatic testing, the resistance of the body and the tightness of the seals are evaluated under extreme conditions.
In this process, collaboration with specialized technical centers—such as the Trevisan Machining Center—enables high-precision verification using automated test benches and CNC systems. These tools ensure repeatable and reliable measurements, adding value to quality control and component traceability.
Another key aspect is the energy efficiency of valves, closely linked to their internal design and maintenance. Efficiency tests analyze parameters such as pressure drop or energy consumption associated with fluid flow. Integrating energy efficiency criteria from design to functional testing contributes directly to more sustainable systems and an effective reduction in operating costs.
It is also important to note that other hydraulic equipment, such as centrifugal pumps, also require rigorous controls. The industrial applications of centrifugal pumps include the transportation of corrosive, abrasive, or high-pressure fluids, making their reliability just as critical as that of valves. The systematic implementation of technical testing on both types of components ensures continuous, safe, and long-lasting operation in any industrial environment
Valve maintenance and pressure testing explained
Maintenance and pressure testing of valves are essential to ensure safety, energy efficiency, and operational continuity in industrial systems. These procedures allow for the verification of component condition, early detection of wear, and validation of performance under real operating conditions.
Pressure testing, also known as hydrostatic or pneumatic testing, is carried out to check the structural strength of the valve body and the tightness of seats and seals. A valve test machine enables the execution of tests such as:
- Body leak test
- Seat and seal test (to verify closure tightness)
- Internal and external leakage detection
- Testing with fluids or gases, depending on the final application
These tests help detect failures related to excessive friction, cavitation, internal erosion, blockages, or pressure loss, all of which impact system performance.
In the case of butterfly valve maintenance, for example, it typically includes inspection of the disc and seat, gasket checks, cleaning of accumulated sediments, and verification of manual or automated actuation. Its simple design facilitates technical intervention and reduces downtime.
In line with Industry 4.0 trends, more and more industries are adopting data-driven approaches to optimize performance and reduce costs. In this regard, the predictive vs corrective maintenance strategy represents a key evolution: through sensors and trend analysis, failures can be anticipated before they occur, minimizing the risk of unexpected shutdowns. This methodology is especially valuable for critical valves in petrochemical, pharmaceutical, or power generation plants.
Finally, having certified personnel in non-destructive testing (NDT) ensures that inspections are conducted in accordance with international standards. This not only improves the quality and reliability of the verification process but also strengthens component traceability and helps raise global standards in industrial manufacturing.
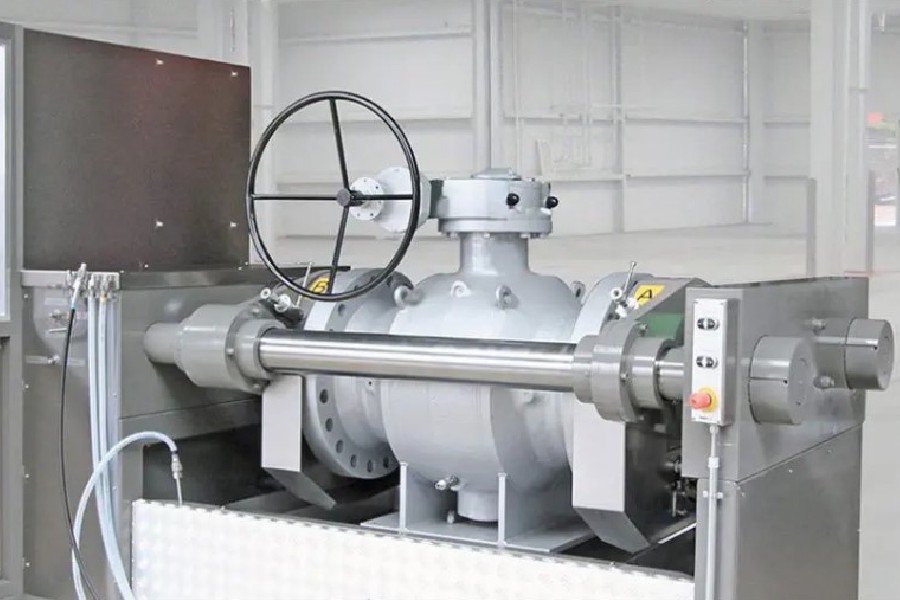
Valve corrosion: causes, prevention and materials
Industrial valves are in constant contact with fluids that may be corrosive, abrasive, or toxic, creating a high risk of structural degradation if the right materials are not selected or if appropriate protection techniques are not applied. Corrosion can lead to issues ranging from partial blockages to severe failures such as leaks or ruptures.
Technically, valve corrosion is defined as damage to metallic materials due to chemical or electrochemical reactions with the surrounding environment. This phenomenon occurs spontaneously and progressively, affecting the entire system: valve, pipelines, connections, and fittings. Prevention is mainly based on isolating the metal from the aggressive environment, or using alternative non-metallic materials.
Some of the main strategies for preventing corrosion include:
- Electrochemical protection (such as sacrificial anodes or impressed current)
- Use of corrosion-resistant non-metallic materials
- Surface treatments such as galvanizing or anodizing
- Selection of special alloys based on the medium (acids, salts, humidity, etc.)
- Application of coatings via thermal spraying or industrial paint
- Use of chemical inhibitors in the process fluid
- Environmental control (temperature, humidity, pH)
- Improved design and manufacturing to avoid accumulation points or turbulence
One of the most effective methods for protecting valves in harsh environments is the use of advanced coatings. There are various types of coatings for industrial valves in extreme environments, such as epoxies, PTFE, ceramic, or metallic coatings, which offer resistance to abrasion, chemical attack, and high temperatures, significantly extending the component’s service life.
Another key aspect in corrosion prevention is the joining technique used during valve manufacturing or repair. Welding for corrosive environments requires specific processes and filler materials that are resistant to aggressive chemical agents, such as duplex stainless steels or special alloys. Poor welding can become a critical point for localized corrosion, whereas proper execution ensures the structural integrity of the component even in highly hostile environments.
In short, many metals are not immune to corrosion, but some can form passive films—such as chromium oxide in stainless steel—that protect them from external aggression. Understanding the interaction between materials and environments is crucial to ensuring valve durability.
Likewise, just like valves, other equipment such as centrifugal pumps are exposed to aggressive environments. The industrial applications of centrifugal pumps range from handling corrosive fluids to high-pressure processes, which is why they also require rigorous inspections and proper material selection to prevent critical failures in operation.
In this regard, selecting suitable materials, applying specific coatings, and conducting periodic maintenance not only helps prevent corrosion, but also contributes to reducing the carbon footprint in industrial pumps and valves, by extending their service life and avoiding premature replacements that involve higher energy and resource consumption.
How often should you pressure test industrial valves?
The frequency at which pressure testing should be performed on a valve depends on several factors: the type of valve, operating pressure, type of fluid handled, system criticality, and industry regulations. In demanding industrial applications—such as chemical processes or high-pressure steam lines—testing may be required quarterly or semi-annually. In less critical cases, an annual inspection may be sufficient.
These tests are typically conducted using liquid media (hydrostatic test) or gases (pneumatic test) to verify the strength of the valve body and the tightness of the sealing components. Their purpose is to ensure the valve can withstand working conditions without leaks or deformation.
Pressure testing is especially relevant when dealing with valves and pumps made of stainless steel, a material widely used in industries that demand high corrosion resistance and maximum reliability, such as pharmaceutical, food, and chemical sectors. The machining of stainless steel valves and pumps must meet strict tolerances and controlled surface finishes to ensure each unit can endure real operating conditions without failure and successfully pass pressure tests without compromising its structural integrity.