Technological innovations in the manufacturing of industrial valves are advancing, resulting in significant improvements in efficiency, reliability, and profitability across various industries. Industrial valves play a crucial role in a variety of industrial applications, from controlling the flow of liquids and gases to regulating critical processes. Among the various categories of valves, needle control valves stand out as a constant area of focus. These valves, known for their exceptional precision, play a fundamental role in the industry.
Emerging Technologies in Industrial Valve Manufacturing
3D Printing and Customized Valves
In the world of industrial valve manufacturing, one of the most exciting trends is the use of 3D printing. This has revolutionized the way valves are designed and produced, allowing for the creation of customized designs and complex parts with unparalleled precision. Companies can tailor valves to specific customer needs, which was previously unthinkable.
3D-printed industrial valves are not only more precise but also lighter and more durable. This reduces wear and maintenance, which is beneficial for a wide range of industrial applications.
Delving into the dynamic field of industrial valves, precision is essential. To ensure that these critical parts operate efficiently and safely, manufacturing companies have incorporated cutting-edge technologies into their processes. From conception to production, the metrology room has become a fundamental component in the pursuit of excellence. These state-of-the-art facilities allow for millimeter-precise measurements and ensure that every valve entering the market meets the strictest standards of quality and performance.
Another notable advancement in industrial valve manufacturing is the implementation of advanced measurement technologies. In this context, the measuring arm has become an invaluable tool. These precision devices accurately assess the dimensions and tolerances of valves, ensuring that each component conforms to the most rigorous specifications. The combination of 3D printing and the precision of measuring instruments has taken valve production to a new level of quality.
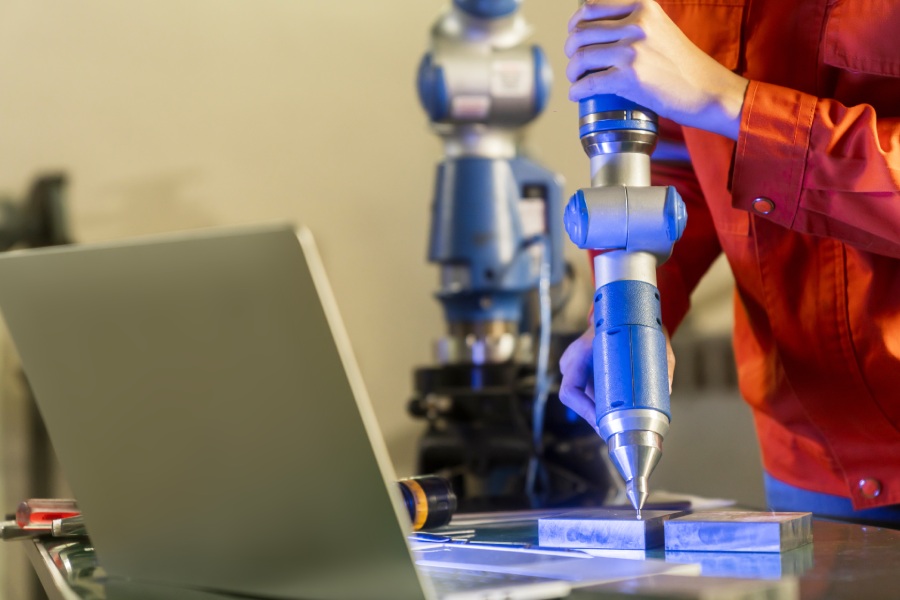
In the constant pursuit of excellence in industrial valve manufacturing, accuracy machining emerges as a cornerstone. The ability to precisely machine key components of these valves is essential for their optimal operation. This is where advanced technologies like 3D printing and IoT monitoring combine with precision machining to create valves that meet the highest standards of quality and performance. These technological innovations are driving efficiency and reliability in the industrial valve industry like never before.
Within the landscape of technological innovations in industrial valve manufacturing, non-destructive testing has gained a prominent place. These advanced techniques allow for the assessment of valve quality and integrity without causing physical damage. By using methods such as ultrasonics, radiography, and liquid penetrant testing, manufacturers can identify hidden defects and ensure that each valve meets the strictest safety and performance standards. The implementation of non-destructive testing is revolutionizing the quality and reliability in the manufacturing of industrial valves, providing invaluable peace of mind to end-users.
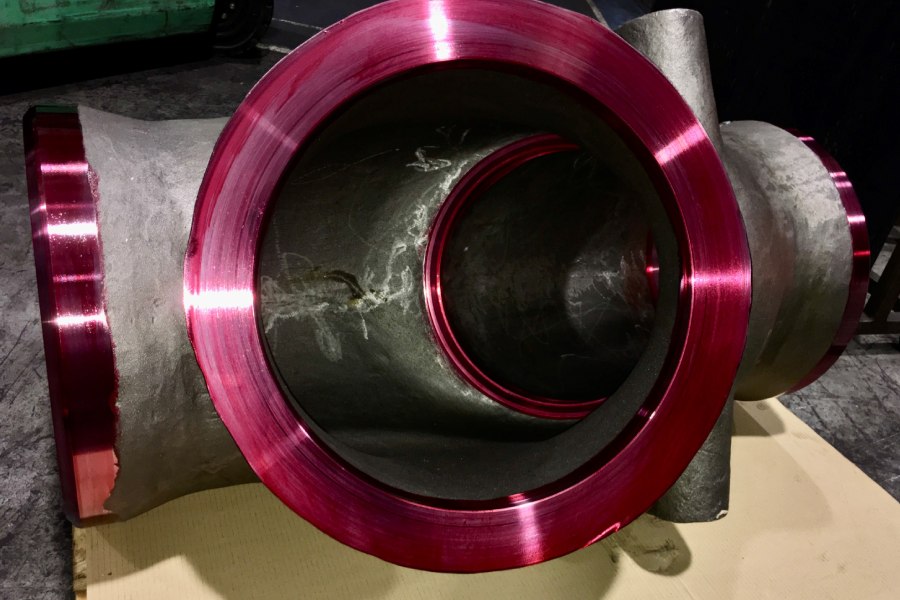
When exploring technological innovations in the fabricación of industrial valves, two key aspects stand out in the current landscape. On one hand, diaphragm valves have evolved to play a crucial role in applications where tightness and precision are imperative. With their unique design, diaphragm valves are ideal for controlling the flow of liquids and gases in critical environments. On the other hand, cryogenic valves have made significant advances, enabling safe and efficient handling of fluids at extremely low temperatures. These technological innovations are shaping the future of the industrial valve market, offering advanced solutions for a wide range of applications.
IoT and Advanced Valve Monitoring
IoT has entered the industrial valve industry. Now, valves can be connected to advanced monitoring systems that allow real-time tracking of performance and status. This is crucial for early detection of issues and data-driven decision-making.
These IoT systems not only enhance operational efficiency but can also significantly contribute to energy efficiency. Valves can adjust automatically based on changing conditions, resulting in reduced energy consumption.
Innovative Materials for Stronger Valves
The strength and durability of valves are crucial in demanding industrial environments. Innovations in materials have led to the development of stronger and more durable valves. Some materials, such as ceramic and metal composites, can withstand extreme conditions and corrosive chemicals.
Advancements in materials not only make valves more resilient but also reduce the need for frequent replacements, resulting in significant long-term savings for industrial companies.
Advantages of the Latest Innovations in Industrial Valves
Energy Efficiency and Smart Valves
The implementation of smart industrial valves, enabled by IoT, directly impacts energy efficiency. These valves can automatically adjust their opening and closing to maintain ideal conditions in a process, reducing energy waste.
Additionally, these valves can provide real-time data on energy consumption and performance, allowing companies to further optimize their processes and save costs.
Cost Reduction Through Automation
Automation is another area where the latest innovations in industrial valves are making a difference. Process automation, with the help of electronically controlled valves, enables greater precision and consistency in industrial operations.
This not only improves product quality but also reduces operating costs by minimizing human errors and reducing the need for labor in repetitive tasks.
Enhancements in Reliability and Predictive Maintenance
Reliability is essential in industrial environments. Modern industrial valves are equipped with sensors and advanced monitoring systems that enable predictive maintenance. This means that companies can schedule maintenance before costly problems occur.
This not only reduces unplanned downtime but also extends the life of valves and improves overall operational efficiency.
The Importance of Staying Up-to-Date with Market Trends
Technological innovations in the manufacturing of industrial valves are driving efficiency, reliability, and profitability in various industries. 3D printing, IoT, and advanced materials are opening new opportunities and enabling better control of industrial processes. Investment in these technologies can make a difference in your company’s competitiveness and long-term success.
The ongoing advancement in the manufacturing of industrial valves is a testament to the industry’s commitment to innovation and continuous improvement. These technological trends are not only transforming how valves are manufactured but also redefining how they are applied and maintained across a wide range of industrial sectors.
3D printing has proven to be a game-changer in terms of customization and precision. The ability to design and produce tailor-made valves according to customer needs is a noteworthy achievement. Previously, adapting valves to specific requirements was a costly and often impractical challenge. However, 3D printing has paved the way for the creation of unique and complex designs that enhance efficiency and effectiveness in a variety of industrial applications.
The implementation of advanced measurement and non-destructive testing technologies has raised the quality and reliability of industrial valves to unprecedented levels. Millimeter precision and the capability to identify hidden defects non-intrusively are advancements that not only ensure optimal performance but also provide invaluable safety to end-users. This translates into increased confidence in the integrity of valves and, consequently, a significant reduction in operational risks.
IoT connectivity has brought a new level of intelligence to industrial valves. The ability to monitor and adjust performance in real-time is essential for early issue detection and energy efficiency optimization. Automation, driven by electronically controlled valves, enhances precision and consistency in operations, reducing operational costs and minimizing human errors. Furthermore, the capability for predictive maintenance helps prevent costly downtime and extends the lifespan of valves.
Regarding innovative materials, advances in ceramic and metal composites have increased the strength and durability of valves in demanding industrial environments. This enhanced resilience not only results in more reliable operation but also reduces the need for frequent valve replacements, leading to substantial long-term cost savings.
In addition to the aforementioned technological innovations, the industrial valve industry is actively exploring the potential of artificial intelligence (AI) in the design and operation of valves. The integration of AI algorithms allows for a deeper analysis of valve performance data, leading to even greater optimization of operational efficiency and reliability. AI’s ability to identify patterns and anomalies in valve operation provides a significant advantage in early problem detection and informed decision-making to continually improve industrial processes.
In summary, the latest innovations in industrial valve manufacturing are revolutionizing how companies address energy efficiency, automation, reliability, and durability. To remain competitive in today’s market, companies must stay informed about these trends and be willing to adopt these cutting-edge technologies. Investment in the modernization of industrial valves is not only an investment in quality and performance but also in the future success and sustainability of your company. Staying informed and embracing these innovations is essential to thrive in the ever-changing industrial valve market.
