Small batches vs. large volume machining for industrial pumps is a strategic decision for manufacturers aiming to optimize costs, lead times, and reliability of critical components, such as components of centrifugal pumps: pump casings, covers, shafts, and impellers. In sectors like Oil & Gas, cryogenics, naval, or desalination, the precision and quality of these parts determine whether equipment will perform efficiently or suffer premature failure.
Asimer Group, leveraging its expertise in CNC machining, offers solutions tailored for both prototypes and small series as well as continuous production, always backed by rigorous quality control.
Want to optimize costs and lead times with a reliable CNC partner?
💡 Contact Asimer Group.
Contact Asimer GroupWhat are the key differences between small batches and large volume machining?
The main difference between small baches and large volumes in industrial pumps lies in the production approach, resource optimization, and cycle time management. However, both require CNC accuracy and stringent quality controls to ensure the performance of critical components such as casings, shafts, covers, or impellers.
Small batches
- Focused on prototypes, unique parts, or limited runs, usually ranging from 1 to 10 units.
- Typically used to validate a new design, customize components for extreme service conditions, or repair non-standard parts.
- Require maximum flexibility in CNC programming: unique machining toolpaths are created and manual adjustments are made to optimize each cut.
- Setup times are longer due to frequent changes in fixtures and tooling, as each part may differ.
- Dimensional verification is often performed piece by piece, using measuring instruments such as a portable measuring arm and equipment in the metrology room.
Large volumes
- Focus on repetitive production, optimized for dozens or hundreds of parts, with automated processes and standardized CNC routines.
- Use dedicated fixtures and predefined machining cycles to minimize setup times and ensure exact repeatability.
- Unit costs drop significantly due to cycle time optimization, the use of durable high-performance tools, and statistical process control (SPC).
- Metrology is performed through batch sampling, without compromising critical tolerances.
Materials and service conditions
In both scenarios, the machining of small batches vs large volumes in industrial pumps requires working with high-performance materials such as SuperDuplex, CD4MCu, WCB, and GGG40, chosen for their resistance to corrosion, high pressures, and extreme temperatures. The choice of material does not depend on the batch size, but on the working conditions of the component and its function within the industrial pump.
Key technical factors that define small batch vs. large volume machining
The success of industrial pump machining depends on key factors that determine precision, cost, and the efficiency of the production by machining. While many of these factors are common, the strategy shifts when handling unique prototypes versus repetitive runs.
1. Setup and programming time: Impact on production
Small batches:
- Require highly customized CAM programs tailored to unique geometries. Each part is programmed and simulated individually to optimize toolpaths, minimize material removal, and prevent deformation.
- Setup involves configuring dedicated fixtures and verifying part alignment, requiring close coordination between programming and inspection.
Large volumes:
- Standardization is crucial. Once a cycle is validated, repetitive routines are created to minimize changeover times.
- Modular fixtures and quick-reference systems enable continuous production with minimal deviations between parts.
- The goal is repeatability, not flexibility.
2. CNC tools and coatings: keys to efficiency
In both scenarios, CNC machining tools are selected based on the material (SuperDuplex, CD4MCu, GGG40, WCB) and part complexity.
- Small batches: Focus on multifunctional tools for quick changeovers and adaptability.
- Large volumes: Use dedicated long-life tools with advanced coatings that enhance wear resistance, thermal stability, and surface finish.
These choices are crucial when working with hard-to-machine materials, where cooling and cutting parameters must be fine-tuned to prevent overheating or microcracks.
3. Quality control and metrology: Common standards
Regardless of batch size, Asimer Group applies mandatory dimensional control and non-destructive testing (NDT):
- Inspections using measuring arms at every critical phase.
- Verifications in the metrology room to ensure concentricity, parallelism, and roughness.
- NDTs such as liquid penetrant testing (PT) and visual testing (VT) in sealing areas or critical welds.
- Compliance with tight tolerances to ensure flawless assembly and performance.
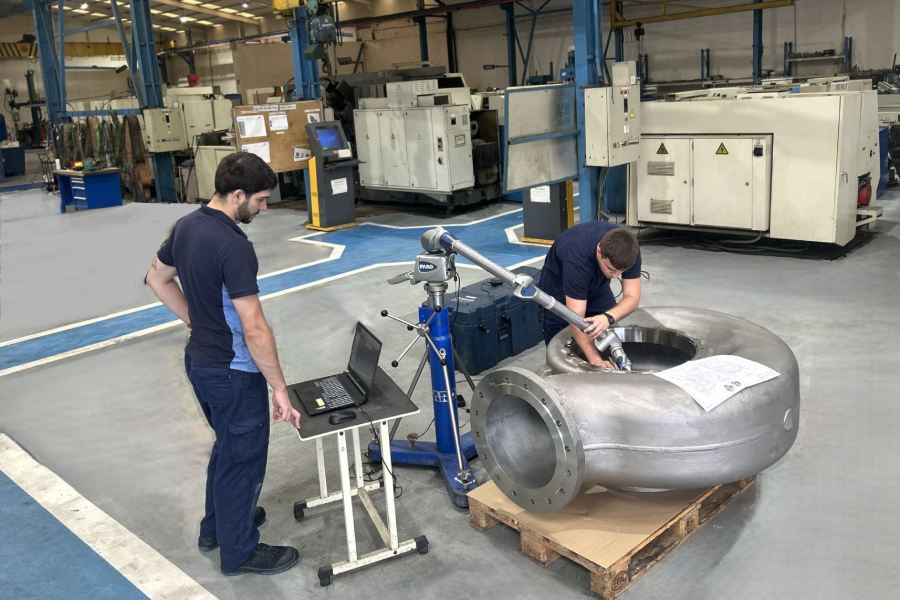
4. Cost and time optimization: winning strategies
Cost reduction in CNC machining is achieved through:
- Automating repetitive cycles with Trevisan machining centers, like the Trevisan DS300.
- Optimizing CNC toolpaths to minimize unnecessary material removal.
- Expertise in quick clamping systems and chip control to reduce downtime.
- Fine-tuning cutting parameters (speed, feed, cooling) to extend tool life and avoid rework.
Furthermore, Industry 4.0 technologies allow real-time process monitoring, cycle time optimization, and full traceability of each part.
- In small batches, the value lies in reducing validation and setup time.
- In large volumes, the focus is on maintaining stable unit costs without sacrificing quality.
Proper optimization of machining and cutting parameters also contributes to improved energy efficiency, not only in pumps but also in valves, where reducing friction and hydraulic losses is key to overall performance.
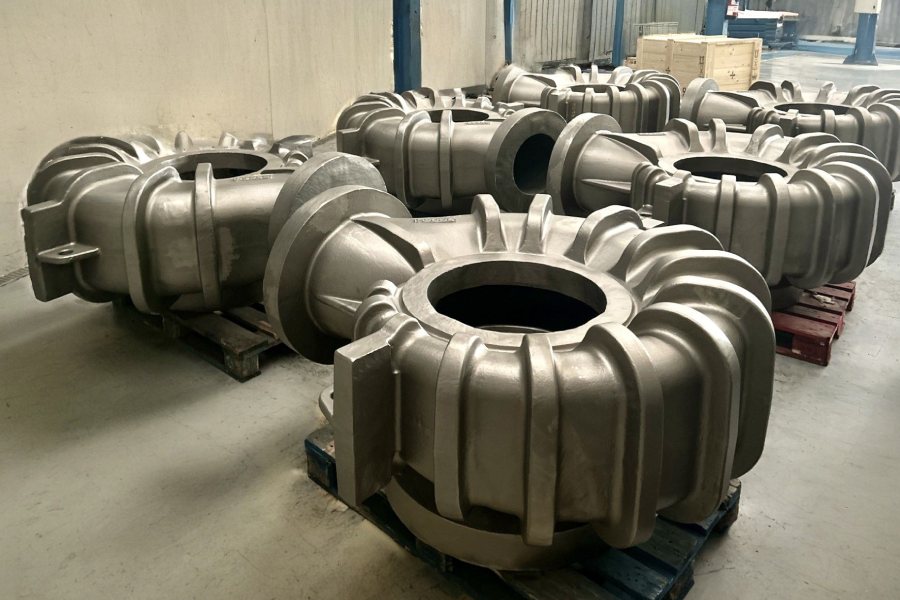
How Asimer Group adapts CNC machining to each batch size
The real difference lies in how we adapt our machining strategy depending on whether the project requires a few custom parts or continuous production.
Small batches: Prototypes and customization
- Each component is treated as a unique piece, with specific CAM programming for each geometry.
- We use versatile fixtures that facilitate assembly and adjustments at every stage.
- Specialized welding processes (TIG, PTA, or automatic MIG) are integrated when a component needs repair or coatings prior to final machining.
Large volumes: Efficiency and repeatability
- We design dedicated modular fixtures and optimize CNC toolpaths to minimize cycle times.
- We use dedicated long-life tools with advanced coatings to machine hard materials like SuperDuplex.
- Statistical Process Control (SPC) is combined with periodic checks in the metrology room to maintain batch quality.
Strategies to reduce costs and lead times in machining
In the industrial sector, outsourcing CNC machining is a proven way to optimize costs and meet deadlines without compromising quality. Asimer Group enables manufacturers to focus on what truly adds value: design, innovation, and engineering.
Advantages of outsourcing with Asimer Group
Eliminating CNC machinery investments (CAPEX):
- Multi-axis machining centers like the Trevisan DS300 require high investment and specialized maintenance.
- By outsourcing, manufacturers avoid expenses on equipment, tooling, CAM software, and upgrades, gaining immediate access to cutting-edge technology.
Savings in technical staff and training:
- Hiring, training, and maintaining a skilled CNC team involves high fixed costs.
- With Asimer Group, you have access to highly qualified programmers, engineers, and operators without the need for internal structures.
Shorter lead times:
- Our ability to handle production peaks and mixed batches (short or long runs) allows us to respond quickly to urgent demands.
- We rely on standardized processes that reduce setup times, optimize toolpaths, and minimize stoppages.
Outsourcing as a competitive advantage
Outsourcing the machining of centrifugal pumps allows manufacturers to:
- Free internal resources for R&D and product engineering.
- Ensure components are ready for assembly with non-destructive testing (PT, VT) and metrology room checks.
- Reduce failure risks thanks to our expertise in machining large-size valves and complex materials like SuperDuplex or CD4MCu.
Materials and sectors where CNC machining is critical
The CNC machining of industrial valves and pums requires materials capable of withstanding extreme conditions, and each sector demands specific characteristics of mechanical, chemical, or thermal resistance.
Key industrial sectors
Oil & Gas:
- We provide CNC machining and industrial welding outsourcing for the Oil & Gas sector, covering valves, pump casings, and components exposed to corrosive fluids, extreme pressures, and temperature changes.
- To extend the lifespan of these components, we apply advanced coatings, similar to those used in types of coatings for industrial valves in extreme environments, adapted to pumps exposed to critical conditions.
- We also integrate welding processes for corrosive environments to enhance resistance.
Naval:
- Components with superior resistance to saltwater corrosion and coatings designed for marine environments.
- We handle projects involving CNC machining of pumps and valves in stainless steel and other corrosion-resistant materials, with exhaustive quality checks to guarantee sealing and durability.
Cryogenics:
- Specialists in machining cryogenic pumps and cryogenic valves, where dimensional tolerances must be maintained even at -196 °C.
- We use high-precision machining for cryogenic applications, including pumps and valves. Cryogenics also plays a critical role in advanced sectors such as aerospace.
Water treatment and desalination:
- We machine components resistant to abrasion and constant exposure to salts and solid particles.
- We apply specific coatings to protect the interiors of casings and covers.
Common materials and machining challenges
At Asimer Group, we work with a wide range of challenging materials, including:
- SuperDuplex (A182 F55, F51): High resistance to corrosion and fatigue, but difficult to machine due to hardness.
- CD4MCu: Stainless steel casting with excellent abrasion resistance, used in impellers and pump casings.
- GGG40 (EN-GJS-400-15): Nodular cast iron commonly used in pump casings for its toughness and machinability.
- WCB: Cast carbon steel, widely used in valves and high-pressure pumps.
- 316/CF3M Stainless Steel: Ideal for corrosive environments in chemical and water plants.
For each material, we adjust cutting parameters, cooling, and tool selection to guarantee a flawless finish and compliance with customer specifications.
Real cases: CNC machining projects with proven results
Case study: Machining 6 centrifugal pump casings in EN-GJS-400-15 (GGG40)
We recently completed a key project for a French manufacturer of advanced-engineering pumps for the Oil & Gas sector.
The project included:
- Full final machining of 6 centrifugal pump casings.
- Non-destructive testing (PT) on sealing areas to ensure component integrity.
- Dimensional control using the metrology room and measuring arm to verify critical tolerances.
The material used, EN-GJS-400-15 (GGG40), is a nodular cast iron with a predominantly ferritic structure, known for excellent machinability, good impact resistance, and durability under heavy mechanical stress. These properties make GGG40 ideal for components like casings, covers, or parts under extreme loads.
Technical highlights of the project:
- Centralized assembly to allow thermal expansion without compromising shaft alignment.
- Optimized wear rings and balance holes to maximize seal and bearing life.
- Reinforced shafts to minimize deflection.
- Options for closed or semi-open impellers, depending on fluid conditions.
- Integration of heated or cooled stuffing boxes, as per customer requirements.
Main applications:
The centrifugal pumps machined in GGG40 are used in:
- Fractionation processes.
- LVGO and HVGO transport.
- Polyethylene (PE) and polypropylene (PP) production.
- Purified terephthalic acid (PTA) processes.
- Water injection systems in energy and Oil & Gas plants.
Asimer Group: Your expert CNC machining partner
At Asimer Group, we are not just machining components; we are a strategic partner for industrial pump and valve manufacturers seeking precision, reliability, and cost optimization.
What sets us apart?
Advanced CNC centers:
- Equipped with Trevisan DS300 machining centers and multi-axis equipment designed for complex geometries, both for small series and large production runs.
- This technology allows us to integrate multiple operations (turning, milling, drilling) in a single setup, reducing errors and downtime.
Full traceability:
- Every component is managed with complete traceability, from drawing reception to final delivery, documenting intermediate inspections and dimensional validations.
Integrated welding and coatings:
- We are specialists in critical welding (TIG, MIG, automatic MIG, and PTA), ideal for parts requiring wear-resistant or corrosion-resistant coatings.
- This allows us to deliver ready-to-assemble components without additional steps.
Rigorous quality control:
- We perform inspections with measuring arms, checks in our metrology room, and NDTs (PT, VT, PMI) to ensure each part meets the most demanding specifications.
Why trust Asimer Group?
- Experts in chip-removal machining of critical pump and valve parts.
- Proven experience with high-complexity materials such as SuperDuplex, CD4MCu, GGG40, and stainless steels.
- Trusted by industries with demanding requirements: Oil & Gas, marine, cryogenics, and desalination.
FAQs: Small batches vs. large volumes
What distinguishes a small batch from a large one?
Mainly the volume and process standardization, not the material or type of inspection.
Which materials are hardest to machine?
SuperDuplex, CD4MCu, and Inconel require highly specific cutting parameters and cooling strategies.
Are all parts inspected?
Yes, dimensional controls and NDTs are applied to every project.
Asimer Group: turning machining into your competitive advantage
Small batch vs. large volume machining for industrial pumps is not just about producing parts; it’s about advanced CNC technology, deep technical expertise, and rigorous quality controls at every stage.
At Asimer Group, we combine these factors with a strong focus on cost and lead time optimization, delivering solutions that enhance the reliability and performance of pumping equipment.
Our methodology focuses on:
- Listening to each client’s technical needs, adapting processes for unique projects or repetitive production.
- Integrating CNC machining with specialized welding and high-performance coatings to deliver ready-to-assemble parts.
- Ensuring full traceability and control with metrology room inspections and NDTs on critical areas.
The result? Faster projects, fewer risks, less rework, and greater added value.
Ready to optimize your machining?