Outsourcing the machining of centrifugal pumps has become a key strategy for manufacturers seeking to reduce costs, meet tight deadlines, and ensure dimensional accuracy in critical components such as casings, covers, impellers, and shafts.
By delegating these processes to a specialized partner like Asimer Group, manufacturers gain access to advanced high-accuracy CNC machining solutions, specialized welding for critical industrial components, and quality control — without the need to invest in machinery, training, or technical staff. This outsourcing not only improves the performance of pumping systems but also enhances operational reliability and process traceability — essential in sectors such as Oil & Gas, naval, cryogenics, and water treatment.
Why outsource the machining of centrifugal pumps?
Reduction in structural and capital equipment costs
Outsourcing machining eliminates the need to maintain in-house production lines, reducing costs related to CNC machinery, technical staff, continuous training, maintenance, and industrial space. This approach enables manufacturers to redirect resources toward hydraulic design, prototype validation, or functional improvements — and to optimize costs in the machining of pumps and valves without compromising final product quality.
Immediate access to advanced CNC technology without CAPEX
Partnering with a company like Asimer Group provides direct access to multi-axis machining centers, vertical and horizontal lathes, and integrated CNC-based solutions — all without capital investment. This infrastructure — powered by Industry 4.0 and the use of CNC machining tools adapted to each geometry — ensures strict tolerances, repeatability in series production, and the ability to machine even large-scale casings and covers.
Focus on core business: Design, engineering, and quality control
By outsourcing the machining of key components such as impellers, shafts, or pump casings, internal teams can focus on their core activities: product development, innovation, and technical supervision. This increases time-to-market responsiveness without compromising pumping reliability or the precision required in [centrifugal pump components].
Technical benefits of outsourcing the machining of centrifugal pumps
High precision in critical components: impellers, shafts, casings
Machining components like casings, covers, impellers, and shafts requires tight tolerances to ensure proper alignment and optimal hydraulic performance.
Asimer Group guarantees these precision levels through dimensional verification in its metrology room, supported by advanced measuring systems such as a portable measuring arm and other high-resolution measuring instruments. This metrology ensures [sealing performance], volumetric efficiency, and extended service life — even under extreme pressure and temperature conditions.
Multi-axis CNC machining for complex geometries
Impellers with curved vanes, volute casings, asymmetrical covers, or special inserts — some of the most demanding centrifugal pump parts — require multi-axis machining with high rigidity and simultaneous interpolation capabilities.
Asimer operates with Trevisan machining centers and other state-of-the-art CNC systems, designed to work precisely with non-standard geometries in stainless steel or super duplex materials. This allows the company to handle machining of large-dimension valves and tailor solutions for harsh environments such as Oil & Gas or desalination plants.
Integration with welding and technical coatings
In many cases, components must be hardened, repaired, or adapted before final machining. Asimer applies TIG welding, MIG welding, plasma transferred arc welding, and automatic MIG welding for cladding, repair, or assembly.
The treated surfaces are then machined with precision, respecting tolerances and surface finishes. This hybrid process expertise enables Asimer to work on technical coatings for industrial valves in extreme environments and on high-precision machining for cryogenic applications in industrial pumps and valves.
Real cases: machining of casings in corrosion-resistant alloys
Machining small series or unique components in high-demand materials — such as super duplex, CF3M, F51, or CD4MCu — requires not only advanced CNC technology applied to petrochemical-grade components, but also experience in cooling strategies, tool selection, and precise dimensional control.
Asimer Group applies tailored [production by machining] strategies to work with these alloys, ensuring critical tolerances, suitable surface finishes, and full compliance with industry standards — even for components destined for corrosive or abrasive environments.
🛠️ Real Example: Machining CD4MCu Casings for Oil & Gas
Asimer recently completed a project for an Italian client specialized in advanced engineering pumps for the Oil & Gas industry.
The project included full machining of 4 centrifugal pump casings in CD4MCu, including:
- Pre-machining stages
- Application of non-destructive testing using liquid penetrant inspection in sealing areas
- Final machining operations
- Final [visual inspections (VT)] conducted by certified Level II operators
CD4MCu is a cast duplex stainless steel known for its excellent resistance to corrosion and wear, ideal for critical service with aggressive fluids.
This type of component requires tightly controlled chip removal machining, expertise in surface treatments, and sequential planning to avoid distortions or geometric defects.
This project illustrates how Asimer delivers real value to manufacturers that require components ready to perform in extreme environments — while complying with the highest quality standards.
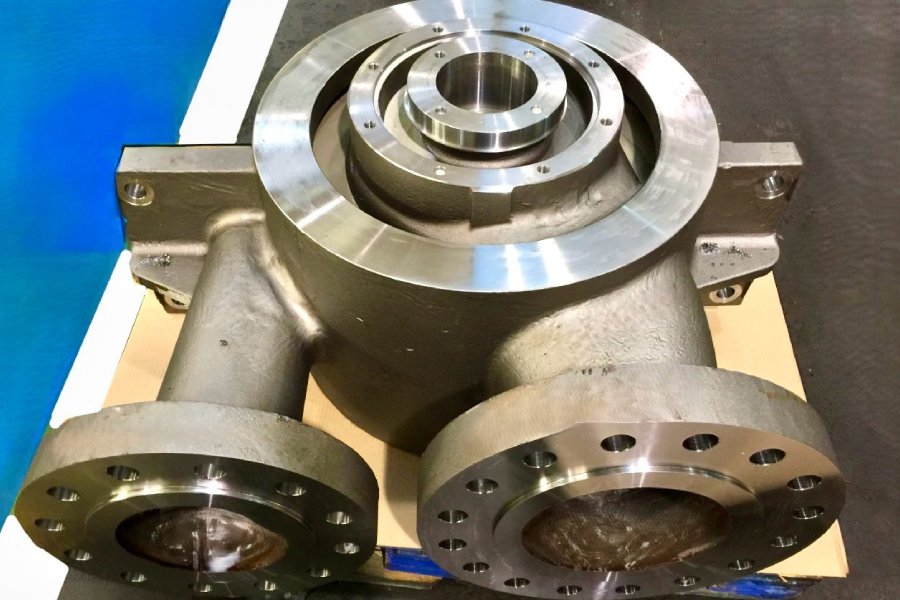
Machining in predictive maintenance of centrifugal pumps
In demanding industrial environments, scheduled shutdowns are a critical opportunity to inspect and replace components that could jeopardize operational continuity. For centrifugal pump components such as covers, shafts, rings, or impellers… all of which require high-precision machining and tight turnaround times.
Asimer Group applies chip removal machining methodologies specifically adapted to [predictive maintenance]. It uses databases of component drawings, reverse engineering based on worn parts, and 3D scanning techniques when technical documentation is unavailable. This allows fast intervention — even on pumps with decades of service or lacking standard spare parts.
Thanks to a combination of multi-axis CNC systems, next-gen CNC machining tools, and optimized industrial planning, Asimer delivers components ready for assembly with critical tolerances and complex geometries — minimizing misalignment or vibration risks.
Traceability is ensured through measuring arm inspections, verifications in the metrology room, and non-destructive testing like liquid penetrant inspections, guaranteeing functional reliability after intervention.
This service is especially valuable in sectors where pump reliability is essential to keep production running safely, such as Oil & Gas, water treatment, or power generation.
Demanding sectors: oil & gas, naval, water and desalination
Asimer Group works in critical industries that demand maximum reliability, mechanical strength, and tight tolerances. Its expertise in machining components for cryogenic applications — such as cryogenic valves and cryogenic pumps — reinforces its position as a trusted partner in critical pumping projects.
It also executes machining of valves and pumps in stainless steel and high-precision machining for the Oil & Gas sector, applying technical coatings, welding for corrosive environments, and stringent dimensional control systems.
In industries like [Oil & Gas], desalination plants, offshore stations, or naval applications, operational reliability directly depends on the precision machining of the casing, covers, shafts, and impellers. While this article focuses on pumps, we’ve also explored how energy efficiency in industrial valves contributes to performance and sustainability in critical systems. That’s why [extreme-duty coatings for industrial valves] are applied to extend service life, ensure energy efficiency, and reduce failures in centrifugal pumps.
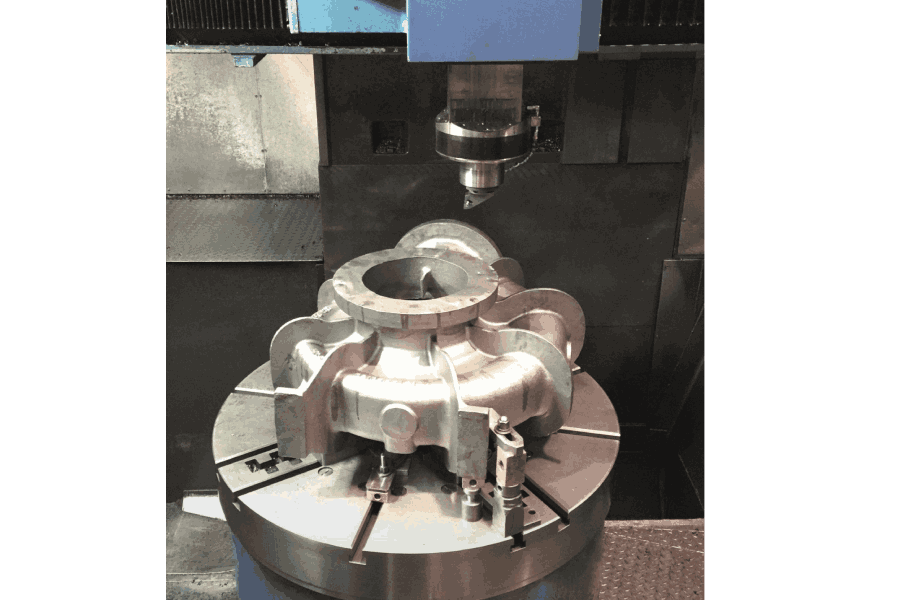
What should a specialized machining partner offer?
Dimensional control with advanced technology
Asimer uses a high-precision portable measuring arm and a metrology room with ISO conditions to inspect concentricity, flatness, roughness, and alignment.
This is complemented by non-destructive testing, including liquid penetrants and other types of NDT for welded or machined zones. These ensure sealing performance and precise assembly without deviations.
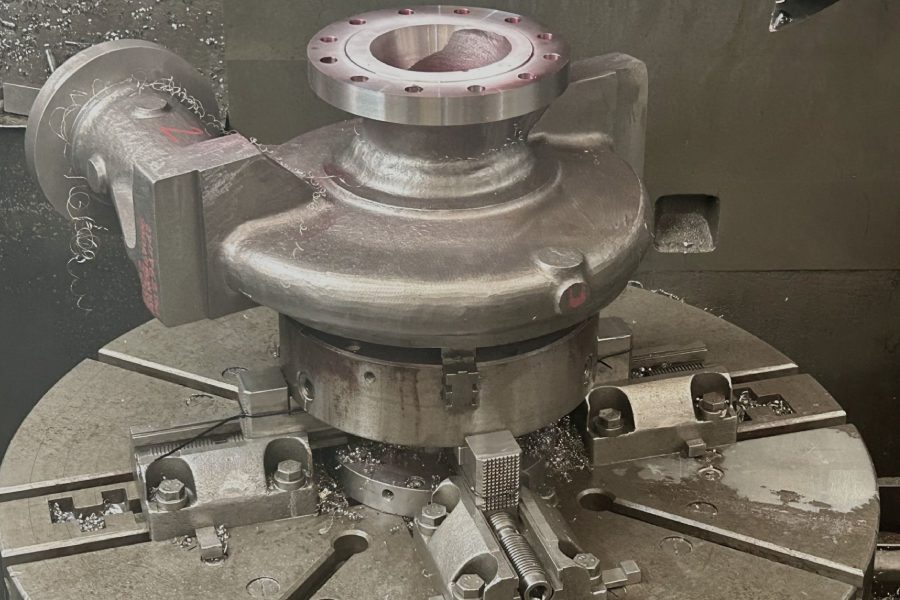
Expertise in demanding materials and critical requirements
From needle control valves to diaphragm valves or axial flow check valves, Asimer works with stainless steels, CF3, F51, and super duplex alloys, applying specific CNC machining tools and optimized cooling strategies.
Surface preparation and tight dimensional tolerances are also controlled, always aiming to reduce hydraulic losses, increase energy efficiency, and minimize failures in centrifugal pumps.
In extreme environments, Asimer follows validated processes in accordance with API and ISO standards, ensuring traceability and certified quality — especially for high-precision machining for the Oil & Gas sector or cryogenic applications.
Comparison: in-house vs outsourced machining
Hidden operational costs
In-house machining requires investment in machinery, training, maintenance, and carries a higher risk of errors. It also demands expertise in clamping, programming, and machining hard materials. Outsourcing to Asimer gives access to multi-axis equipment, validated processes, and certified dimensional inspection.
Scalable production without additional investment
Outsourcing allows manufacturers to handle production peaks or new series without expanding facilities or hiring staff. Asimer offers agile and flexible machining production, with consistent quality and on-time delivery.
Reliable deliveries
With multisectoral experience, advanced planning, and redundant systems, Asimer ensures on-time deliveries without improvisation. This applies to both chip removal machining and parts requiring pre-welding — offering peace of mind to manufacturers.
When should you outsource centrifugal pump machining?
Outsourcing is recommended in situations such as:
- Capacity expansion
- Development of new models
- Special series for severe environments
- Projects involving large components or complex materials
- Predictive or corrective maintenance services
All this without compromising quality, traceability, or reliability — while also helping reduce the carbon footprint in pumps and valves through optimized and controlled processes.
Why choose asimer group as your partner?
Asimer is more than just a supplier — it is a technical ally capable of:
- Executing chip removal machining on complex centrifugal pump components
- Integrating [specialized welding for critical industrial components]
- Developing solutions in outsourcing of machining and industrial welding for Oil & Gas, naval, water, or cryogenic sectors
🔧 Looking for a reliable partner to machine key components in your centrifugal pumps?
💡 Contact Asimer Group and discover how to reduce risks, lead times, and costs with an expert supplier who understands your industry.
I want to contact Asimer GroupFrequently asked questions
What are the advantages of outsourcing versus in-house machining?
It helps reduce costs, eliminate CAPEX, and ensure precision in components such as shafts or casings — through machining experts.
Which components can be outsourced?
All centrifugal pump components: casings, covers, shafts, impellers. All require high precision to ensure sealing performance.
Which sectors outsource this service?
Oil & Gas, water treatment, desalination, cryogenics, naval, and other industries involving corrosive fluids.
How do I choose a reliable machining partner?
They should offer dimensional control, CNC technology, a measuring arm, certified traceability, and experience with demanding materials such as super duplex.
Is it viable for small or urgent series?
Yes. Well-planned outsourcing provides [scalable flexibility without additional investment], adapting to tight deadlines and limited production runs.