Flow control valves: characteristics and applications in the naval industry.
Flow control valves are used to limit and regulate the flow of liquids, gases or a mixture of both. In this article, we will delve into the function of the flow control valve and its applications in the naval industry.
What are flow control valves in the naval industry?
Flow control valves regulate the flow of liquids and gases in a system. Valves may be open or closed to allow or stop flow. In a wide variety of applications, flow control valves are used highlighting among others the naval industry.Globe valves, gate valves, ball valves, check valves and diaphragm valves are some of the different types of flow control valves. It is important to choose the right flow control valve for the application.
How do flow control valves work?
The main functions of the valves are to direct the flow of fluids, regulate the pressure and control the flow of fluids. Flow control valves work by regulating the opening and closing of an opening to allow or stop the flow of a fluid.
Flow control valves can open or close manually or automatically. Manual valves are opened or closed by a crank or lever, while automatic valves are opened or closed by a system controlled by an electronic or mechanical device, such as a solenoid valve or controller.
Directional control valve, pressure control valves and flow control valve are some of the different types of valves whose function is to regulate pressure and control fluid flow. In some cases, these flows need to be controlled to reduce the input of fluids to certain components. Then, in such cases, hydraulic flow control valves are used. Regulating the speed of the cutting tool, spindle, flat grinder, etc. are some of the applications of these valves. In addition, most agricultural constructions and heavy machinery use these hydraulic valves. Simple structure, simple operation and a wide range of adjustments are the advantages of flow control valves.
The main purpose of the flow control valve is to regulate the flow of fluids to various components in a hydraulic circuit. Other functions are to regulate the speed of linear and rotary actuators, regulate the availability of energy for the subcircuits, divide and regulate the flow of the pump, etc.
In general, flow control valves are a key component in many industrial and commercial systems, as they allow to regulate and control the flow of liquids and gases accurately and safely.
Characteristics of flow control valves.
There are a number of features that make flow control valves suitable. The most important features are listed.
- Materials: Flow control valves are available in different materials such as stainless steel, bronze, cast iron, duplex steel and plastics, among others. The choice of material will depend on the working conditions and chemical compatibility with the fluid being moved.
- Connection type: Flow control valves are available in different types of connections, such as flanges, threads, welding and related pipes, among others. The choice of connection type will depend on the size and type of pipe in which the valve will be installed.
- Opening and closing: Flow control valves can open and close manually or automatically. Manual valves are opened and closed by a crank or lever, while automatic valves are opened and closed by a system controlled by an electronic or mechanical device.
- Pressure and temperature: Flow control valves are available in different pressure and temperature ranges to suit different applications. It is important to select a valve that is suitable for working conditions to ensure long service life and optimal efficiency.
- Design: Flow control valves are available in different designs, such as ball valves, gate valves, globe valves and check valves, among others. Each design has specific features that make them suitable for different applications.
- Certification: Some flow control valves are certified to meet international standards, such as API, CE or ISO, among others. Certification can be important to ensure safety and quality in critical applications.
Types of flow control valves.
There are different types of flow control valves available on the market. Gate valve, globe valve, sleeve valves, diaphragm valves and check valves are some of the main categories.
- Gate Valve: Gate valves are compatible with a wide range of fluids and are suitable for high pressure and high temperature applications. These valves are used for strangulation-free opening/closing services that require a straight-line fluid flow with a minimum restriction of gate valves. However, these valves are not suitable for sludge and viscous fluids. Vibration and slow response characteristics are the drawbacks of gate valves.
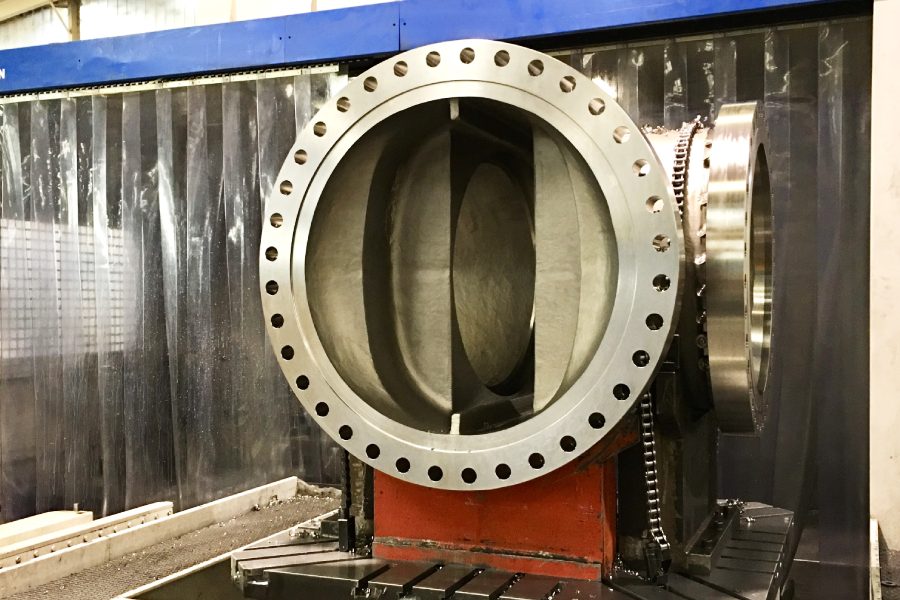
- Globe valve: Globe valves are linear motion valves to stop, start and regulate flow. These valves are used for opening/closing and regulating applications. The globe valve is a general purpose flow control valve that is used for high temperature applications. These valves are comparatively faster and more reliable with limited wear to the seat disc under partial opening conditions.
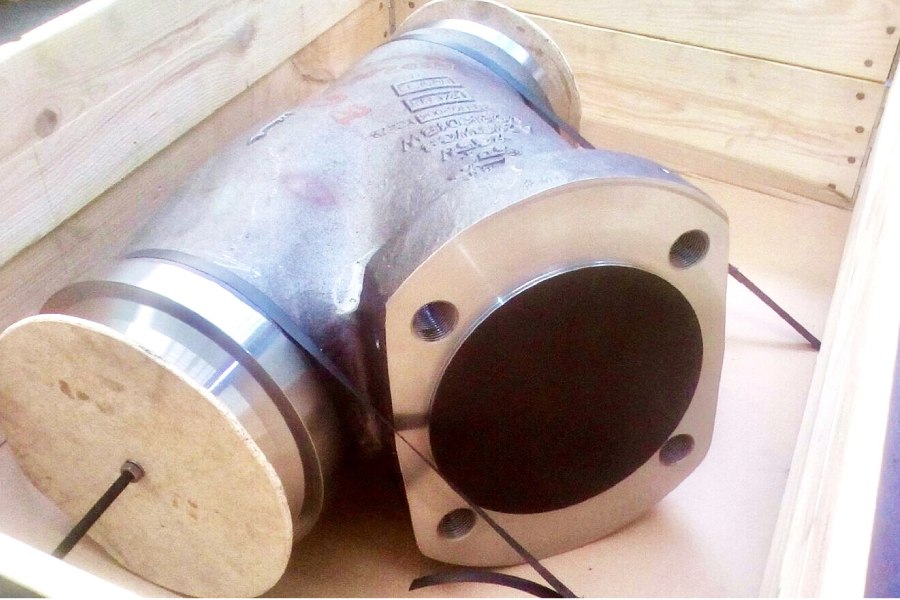
- Sleeve valve: Sleeve valves are low cost flow control valves suitable for slurries or liquids containing significant amounts of suspended solids. These valves provide 100% airtight closures and are used in the food, chemical, wastewater and beverage industries.
- Diaphragm valve: Diaphragm valves are an important category of flow control valves used for throttling services. These valves are suitable for applications using corrosive liquids at low temperature and pressure. Diaphragm valves have leak-proof seals that ensure tight seals. In addition, these valves are extremely clean and easy to maintain.
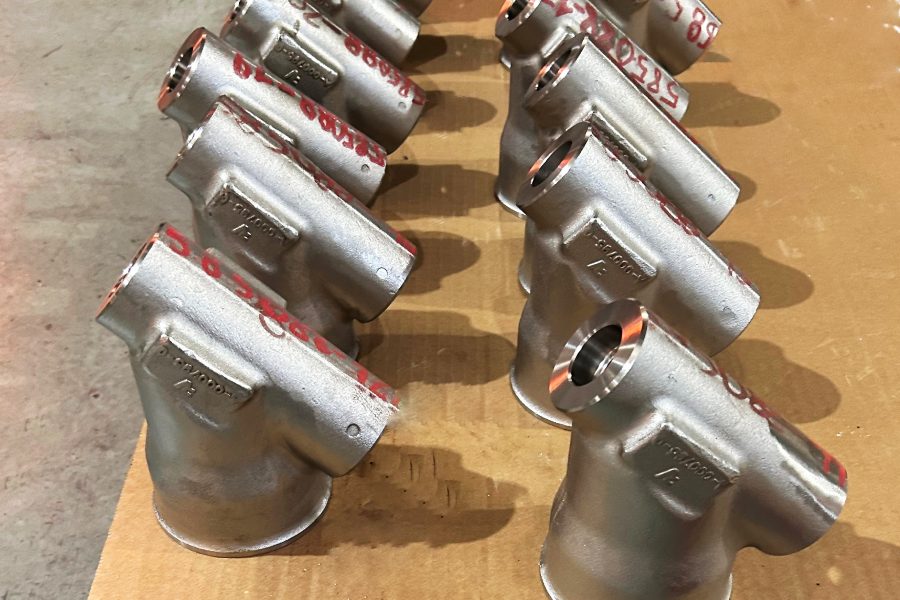
- Check valve: Check valves are unidirectional valves used in industrial pumps, aircraft hydraulics, sprinklers, etc. These valves contain two ports, for entering and unloading fluids. By preventing fluid reflux, these valves will protect the pumps and compressors in the system. Maintaining pressure and serving as a backup system are the important advantages of check valves.
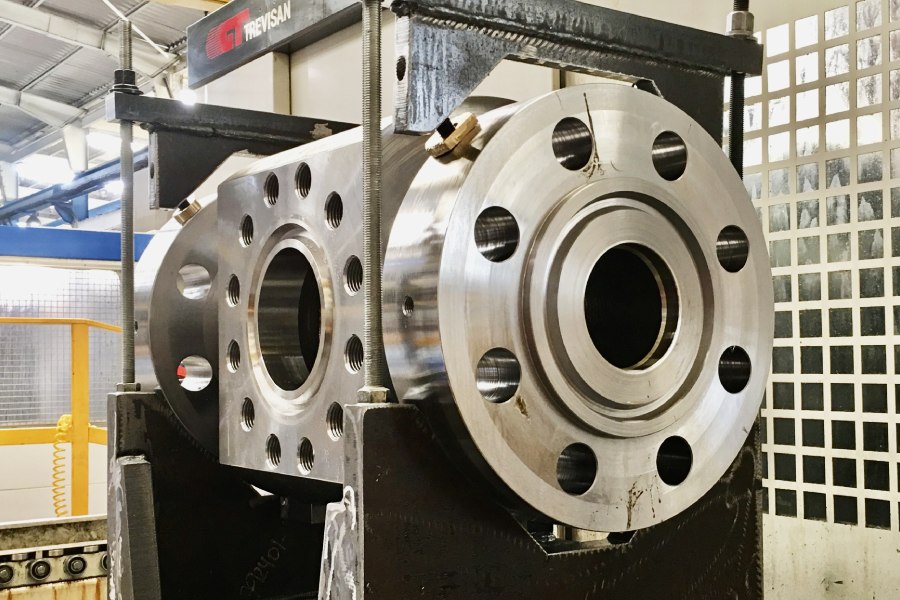
Applications of flow control valves in the naval industry.
Flow control valves are critical components in many naval industry systems, as they allow controlling and regulating the flow of fluids through pipelines and equipment. Some of the most common applications of flow control valves in the naval industry include:
- Cooling systems: Flow control valves are essential in ship and submarine cooling systems, where they are used to regulate the flow of coolant through heat exchangers and evaporators.
- Fuel systems: Flow control valves are important in ship and submarine fuel systems, where they are used to control and regulate the flow of fuel to engines and other equipment.
- Water systems: Flow control valves are critical in ship and submarine water systems, where they are used to regulate the flow of drinking water, bilge water and cooling water.
- Steam systems: Flow control valves are essential in ship and submarine steam systems, where they are used to control and regulate steam flow through heaters and other equipment.
- Lubrication systems: Flow control valves are important in ship and submarine lubrication systems, where they are used to regulate the flow of lubricant through equipment and engines.
- Compressed air systems: Flow control valves are critical in ship and submarine compressed air systems, where they are used to control and regulate compressed air flow to ventilation systems and other equipment.
In the naval industry, flow control valves play a crucial role in the safe and efficient operation of hydraulic and fluid systems aboard vessels. From controlling the flow of cooling water to regulating fuel, these valves ensure optimal performance in challenging maritime conditions. By connecting this article with “Chip Removal Machining in the CNC Era,” we can explore how precision CNC machining contributes to the reliability and durability of these valves in the naval environment.
In general, flow control valves are an essential part of naval industry systems, and their proper functioning is essential to ensure the safety, efficiency and optimum performance of ships and submarines.
In the naval industry, industrial valves are critical components that play an essential role in the precise regulation of the flow of liquids and gases through piping systems, enhancing efficiency and safety in such a demanding environment as the sea.
Advantages of using flow control valves in the naval industry.
Flow control valves are used in the naval industry for several reasons.
- Precise flow regulation: The amount of liquid or gas flowing through a piping system can be regulated with great precision with the help of flow control valves.
- Increased safety: Greater safety can be achieved by avoiding overpressures or low pressures that can damage equipment or cause leaks.
- Energy savings: By allowing more precise flow control, flow control valves can help reduce energy consumption and minimize operating costs.
- Increased durability: Flow control valves can be designed to be resistant to corrosive environments, which can extend the life of piping systems.
- Ease of maintenance: Flow control valves can be relatively easy to maintain and repair, which can minimize downtime and reduce maintenance costs.
Importance of flow control valves in the naval industry.
The naval industry uses flow control valves to regulate the flow of liquids and gases through the piping systems of ships and other vessels. These valves are important to ensure the safety and efficiency of piping systems. Flow control valves enable precise regulation of the flow of liquids or gases, helping to improve the performance and efficiency of piping systems.
This is especially important in the naval industry, where fuel efficiency and vessel speed are key factors in operation.
In addition, flow control valves can improve the safety of piping systems by preventing overpressure and underpressure that can damage equipment or cause leakage. In an environment as hostile as the sea, it is particularly important to ensure the safety and reliability of piping systems.
Another important advantage of flow control valves is that they can help reduce energy consumption and minimize operating costs. By allowing more precise flow control, flow control valves can minimize the amount of energy needed to operate piping systems, which can be a critical factor in ships’ profitability.
Flow control valves are essential components in the naval industry, where performance and reliability are paramount. The manufacturing of high-precision control valves is achieved through cutting-edge technology and the highest quality components. In this context, the Trevisan Machining Center plays a crucial role in supporting the production of these control valves, ensuring their precision and efficiency in critical applications in the naval industry.
In short, flow control valves are critical elements in the naval industry, helping to ensure the safety, efficiency and profitability of pipeline systems used on ships and other ships. Without these valves, it would be much more difficult to operate and maintain reliable and efficient piping systems in the hostile sea environment.
Flow control valves at Asimer Group.
Asimer Group has extensive experience in the field of processing flow control valves thanks to its development and continuous improvement in management means.
Over the last 14 years, Asimer Group has participated in the development of type valves: Gate, Globe, Ball, Check, Butterfly valves… together with the technical department of many of its most important customers, since this type of fluid control valves combine the improvement of efficiency and safety to cost reduction and process automation.
The machining of fluid control valves is a crucial process in the manufacture of these parts, which are essential in the regulation and control of fluids used in a wide variety of applications in industry, such as oil and gas, energy, chemistry and the naval industry. During this process, specialized machinery is used to shape and adjust valve dimensions, according to design specifications. At Asimer Group, we have high precision machining tools and computerized numerical control systems (CNC) resulting in highly precise and complex valves with very tight tolerances. In addition, the use of rigorous inspection and testing techniques helps ensure that valves meet the quality and safety standards necessary for use in critical environments.
This process includes removing excess material to produce a smooth and uniform surface, the drilling of precise holes to allow the passage of fluid and the creation of threads and other types of connections to facilitate the installation and connection of the valve in the system.
Based on our experience, our technical office is constantly looking for new solutions that can facilitate or improve existing ones, to offer our clients customized projects adapted to their needs.
In the context of the naval industry and the operation of flow control valves, it is crucial to highlight the significant impact of Industry 4.0 and the CNC Machining Revolution. These technological advancements are radically transforming the way valves are designed, manufactured, and utilized in the naval industry. From optimizing production processes to improving the precision and quality of components, the integration of Industry 4.0 and CNC Machining is redefining standards in the flow control valve industry.