What is meant by centrifugal pump?
A centrifugal pump is a mechanical device that uses centrifugal force acting on fluid to pump fluid using mechanical power (rotational energy).
The motor provides mechanical power in most cases. To pump fluids, a centrifugal pump employs centrifugal force. As a result, it is known as a centrifugal pump. Centrifugal power affects an object or material moving in a circular path by causing it to move away from the path’s central axis or centre point. This capability can be used to control pressure and movement within a pump unit.
In the universe of centrifugal pumps, CNC machining makes a difference by ensuring the precise manufacturing of each component. This translates into efficient and durable operation of centrifugal pumps, making CNC machining fundamental in the comprehensive understanding of this industrial equipment.
It is the most common form of hydraulic equipment used to transport fluids from low to high pressure areas in a wide range of industries and in many daily gadgets. It moves fluid from one place to another using an internal impeller.
In addition to centrifugal pumps, it is essential to have a complete understanding of the various categories of industrial pumps that drive the operation of different sectors. If you want to explore in depth the types, operation and applications of these vital engineering tools, we invite you to read our article dedicated to industrial pumps, everything you need to know: Types, operation and their applications. You’ll get a comprehensive view of how these pumps play a crucial role in a wide range of industries, from manufacturing to water systems and more.
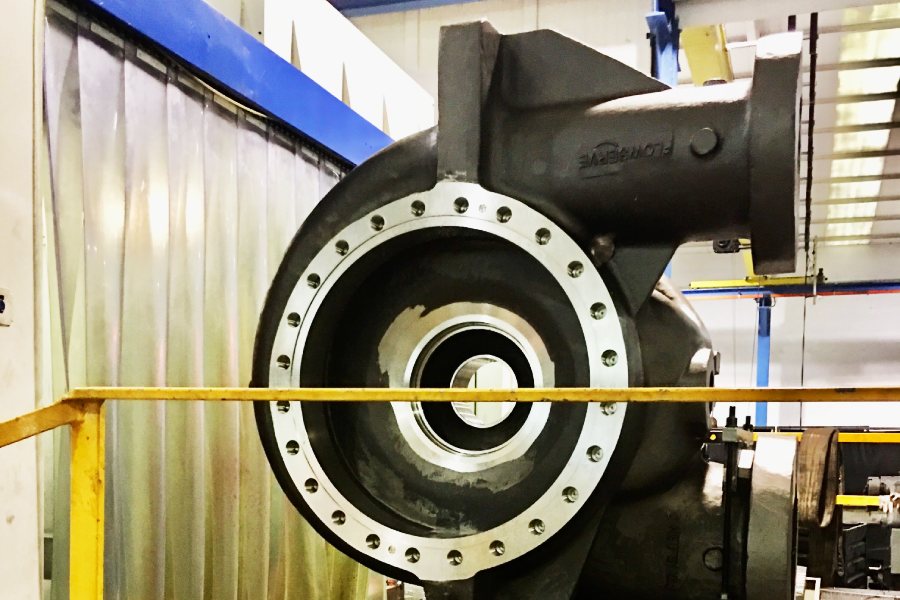
How do centrifugal pumps work?
Centrifugal pumps use one or more impellers, which are coupled and rotate with the pump axis. This provides the power to move the liquid through the pump and pressurizes the liquid to move it through the piping system. Therefore, the pump turns the mechanical energy of a motor to the energy of a moving fluid. A part of the energy becomes kinetic energy of the movement of the fluid, and another part to potential energy, represented by the pressure of the fluid or by its elevation, against gravity, to a greater height.
The transfer of energy from the mechanical rotation of the impeller to the movement and pressure of the fluid is often described in terms of centrifugal force. The exit pressure is a reflection of the pressure applied by centripetal power.
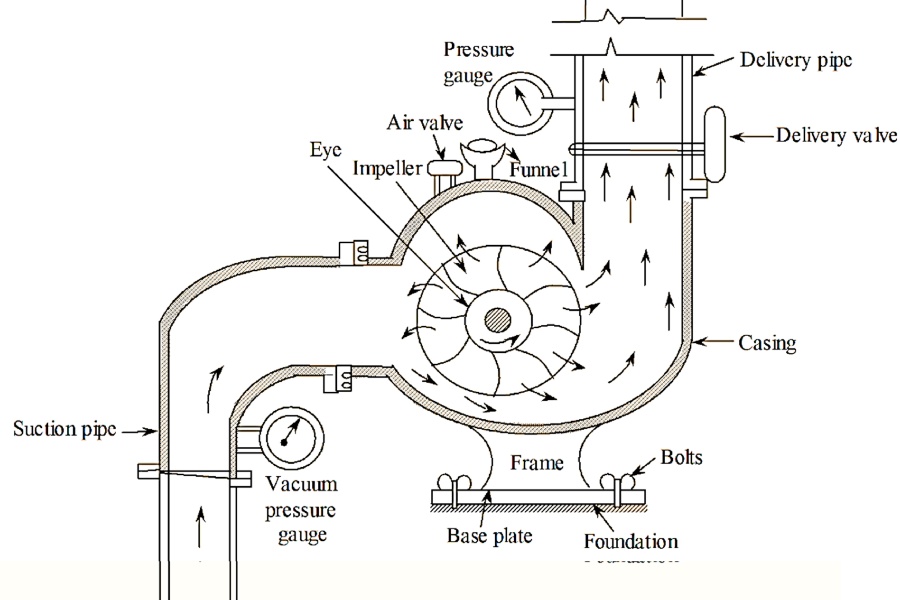
Different types of centrifugal pumps
There are four main centrifugal pumps classifications (the main distinction of each is the mechanism that operates the alternative diaphragm):
- Mechanically actuated
- Hydraulically actuated
- Solenoid and air actuated
- Double membrane pumps (AODD).
Materials of centrifugal pumps
There is a wide variety of construction materials, that go from various plastics and stamped cast iron or stainless steel for lighter duties, to bronzes, stainless steels, exotic alloys and specialty plastics for more corrosive, abrasive, hygienic or other difficult applications.
Uses and applications of centrifugal pumps
Typical applications for centrifugal pumps include:
- Liquids of all viscosities
- Chemical processes
- Foods
- Pressure lubrication
- Pressure painting
- Cooling systems
- Oil burner service
- Grease management
- Liquefied gasses (propane, butane, ammonium, freon, etc..)
https://www.asimergroup.com/en/cryogenic-valves-how-they-work-types-and-uses/As we have detailed in point number 6, centrifugal pumps are also widely used in cooling systems that require extremely low temperatures, such as in cryogenic applications. These cooling systems often involve handling cryogenic gases, such as liquid nitrogen or liquid helium, to cool critical components in scientific research, semiconductor production and medicine. Centrifugal pumps are essential in these systems as they allow the transfer of high purity cryogenic liquids and gases and ensure a consistent and uniform flow, helping to maintain the stability and accuracy of these critical cooling systems.
What are the main characteristics of a centrifugal pumps
There are two large families of pumps: centrifugal and positive displacement. Compared to the latter, centrifugal pumps are often specified for higher flow rates and to pump lower viscosity liquids. In some Chemical Plants, 90% of the pumps used are centrifugal. However, there are a number of applications for which positive displacement pumps are preferred.
What are the limitations of a centrifugal pump?
The centrifugal pump’s efficient working is based on the constant and high speed rotation of its impeller. Centrifugal pumps become increasingly inefficient with high viscosity feeds: there is a higher resistance and higher pressure is required to maintain a specific flow rate.
Sludge, such as sludge, or high viscosity oils can cause excessive erosion and overheating resulting damages and premature failures. Positive displacement pumps typically work at significant lower speeds and are less susceptible to these problems.
Another limitation is that, unlike a positive displacement pump, a centrifugal pump cannot suck dry: it must initially be primed with the pumped fluid. Therefore, centrifugal pumps are not suitable for any application where the supply is intermittent. Also, if the supply pressure is variable, a centrifugal pump produces a variable flow rate; a positive displacement pump is insensitive to pressure changes and will provide a constant output. Therefore, in applications where precise metering is required, a positive displacement pump is preferred.
Industry 4.0 and CNC Machining of Pumps
In the realm of centrifugal pumps, the synergy between Industry 4.0 and CNC machining emerges as a transformative catalyst. The precise manufacturing of each component, vital for the efficient and durable performance of centrifugal pumps, finds its forefront in CNC machining. This advanced technology not only ensures quality but also drives significant improvements in the design and functionality of these essential pumps. From their operation to their applications, this marriage between Industry 4.0 and CNC machining is shaping a new era in industrial engineering, marking a milestone in the evolution of these crucial hydraulic tools.
TIG Welding in Centrifugal Pump Manufacturing
Tungsten Inert Gas (TIG) welding has become an indispensable technique in centrifugal pump manufacturing. This welding technique, which utilizes a tungsten electrode to generate the arc and an inert gas to shield the welding area, offers exceptional precision and high quality in joints. With TIG welding, a wide variety of materials can be welded, from stainless steel to exotic alloys, ensuring optimal strength and durability in centrifugal pumps.
Centrifugal pumps are essential in a wide range of industries, and their manufacturing requires precise welding techniques to ensure efficiency and durability. TIG welding has become the cutting-edge solution for the manufacturing of industrial pumps and valves, ensuring exceptional quality standards and optimal performance.
TIG welding is used to join key components of centrifugal pumps, such as casings, impellers, and shafts, ensuring structural and functional integrity without compromise. Thanks to its ability to produce clean and defect-free welds, TIG welding greatly contributes to the efficiency and reliability of centrifugal pumps in a wide range of industrial applications.
Pumps at Asimer Group
Asimer Group has been collaborating with leading European pump and valve manufacturers for over 10 years, including names like FLOWSERVE, ANDRITZ, SULZER, among others. This extensive collaboration has allowed Asimer Group to delve into the world of industrial pumps. Over time, we have gained in-depth knowledge of centrifugal pumps and extensive experience in their development. This has led us to tackle increasingly complex challenges, such as advanced materials and growing quality demands. These demands primarily focus on dimensional tolerances, surface finishes, and non-destructive testing (NDT).
As we explore the fascinating world of centrifugal pumps, it is crucial to recognize the importance of having cutting-edge facilities, such as the Trevisan Machining Center, for the precise manufacturing of components that drive the optimal functioning of these pumps. The use of state-of-the-art equipment ensures quality and efficiency in the production of these key components, which play a fundamental role in various industrial applications. If you wish to obtain more information about how we accurately produce these components, we invite you to explore our article dedicated to the Trevisan Machining Center.
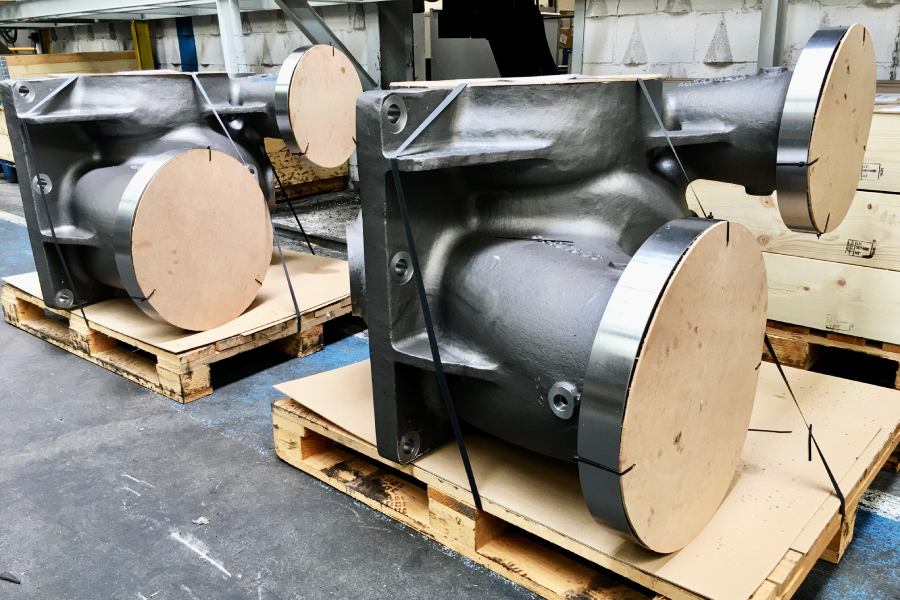