Accuracy is key in CNC machining, and Industry 4.0 has taken this rigor to new levels. From the manufacturing of industrial parts to the engineering of key components, CNC technology has revolutionized the way precision is achieved. Exploring how CNC technology is transforming the petrochemical industry towards efficiency and quality is essential to understanding its impact on modern manufacturing.
In this article, we thoroughly explore the significance of accuracy at every stage of the process. From meticulous programming to millimetric execution, we highlight how CNC technology redefines manufacturing standards. With a meticulous focus on every detail, we unveil how precision is not only a requirement but a philosophy driving innovation in the industry. We invite you to join us in this research process, where meticulousness and excellence intertwine to forge the foundations of the future in the realm of CNC machining.
What is accuracy in CNC machining
Precision, vital in any engineering development, refers to the difference between the actual measurement and the measurement of your system. If the difference between the two is extremely small, the accuracy of that measurement is said to be high. It is also known as the degree of conformity.
In addition, this term defines the reliability of a machine tool. Basically, precision is a measure that defines the ability of a measurement system to return the same measurement over and over again. In addition to this, it is very important that a measurement system is accurate and accurate.
In the world of CNC machining, precision is a critical factor in ensuring component quality and performance. A particularly relevant aspect is the manufacture of fittings used in the oil gas sector. These fittings play a crucial role in preventing leaks and improving the tightness of piping systems. Precision in CNC machining becomes even more crucial when considering the tolerances and specifications required to ensure perfect fit and effective sealing. The ability to achieve accurate dimensions and high quality finishes in fittings through CNC machining is essential to prevent leaks and ensure safety in the oil gas sector. For more information on how to prevent leaks and improve tightness thanks to fittings in the oil gas sector we invite you to read our article on “How to avoid leaks and improve tightness thanks to fittings in the oil gas sector“.
Precision machining is a process that removes excess raw material from a workpiece, while maintaining critical tolerance finishes, to create a finished product. Simply put, it means molding large pieces of material into more precise parts, so they can meet very exact specifications. This process involves cutting, milling, turning (cutting processes by chip removal), and is usually performed using computer numerical control (CNC) equipment.
The machining industry today produces a large number of large and small objects that we use in everyday life.. From automotive production to surgical devices and aircraft parts, precision machining is present in all technologies, engineering and industries such as the petrochemical industry.
The importance of oil refining and its relation to welding and machining of industrial pumps and valves is essential to ensure the correct operation of the machines. In this process, it is essential to have high quality components, such as valves, that control the flow of liquids and gases in machines. If a valve does not work properly, it can affect machining accuracy and put the quality of the final product at risk. Therefore, it is essential that CNC machining manufacturers carefully select the right industrial valves and perform rigorous testing to make sure they are working properly. In this sense, the quality of oil refining is key for the production of high quality components in the machining industry.
Another critical component in the CNC machining process is the pump, which supplies the coolant to the cutting tool to prevent overheating and ensure machining accuracy. Choosing the right pump can significantly improve the efficiency of the machining process, reduce production time and improve the quality of the final product. It is important to select a pump that has the ability to supply the right amount of coolant, with the right pressure and flow rate, to avoid failures and ensure machining accuracy. In short, both valves and pumps are key components in CNC machining, and it is crucial to carefully select the right components to ensure the success of the machining process.
In the CNC machining process, precision is an indispensable quality, especially in the manufacturing of industrial pumps and valves. These essential components require not only exact dimensions but also impeccable structural integrity to ensure their optimal performance in demanding industrial applications. This is where TIG welding comes into play, a cutting-edge technique in metal joining that offers exceptional precision and unsurpassed quality. TIG welding ensures the structural integrity and tightness of industrial pumps and valves, providing a reliable and high-quality solution for manufacturing these critical components in industrial systems.
Moreover, precision machining requires the ability to follow extremely specific drawings made by computer-aided design (CAD) or computer-aided manufacturing (CAM). This CNC (Computer Numerical Control) machining technology creates 3D diagrams or contours needed to produce a machine, object or tool. Plans must be created in great detail to ensure quality and success.
CNC (Computerized Numerical Control) machine operators work with a variety of materials such as bronze, glass, graphite, plastics, steel and other metals. Depending on the size of the project and the materials involved, several quality control tools such as the measuring arm and different IMEs (Measuring and Testing Instruments) will be used, collected in the corresponding Metrology Room. In addition, sometimes it will be necessary the 3D Mapping (3D mapping software that allows you to create, analyze, visualize and share measurements with third parties).
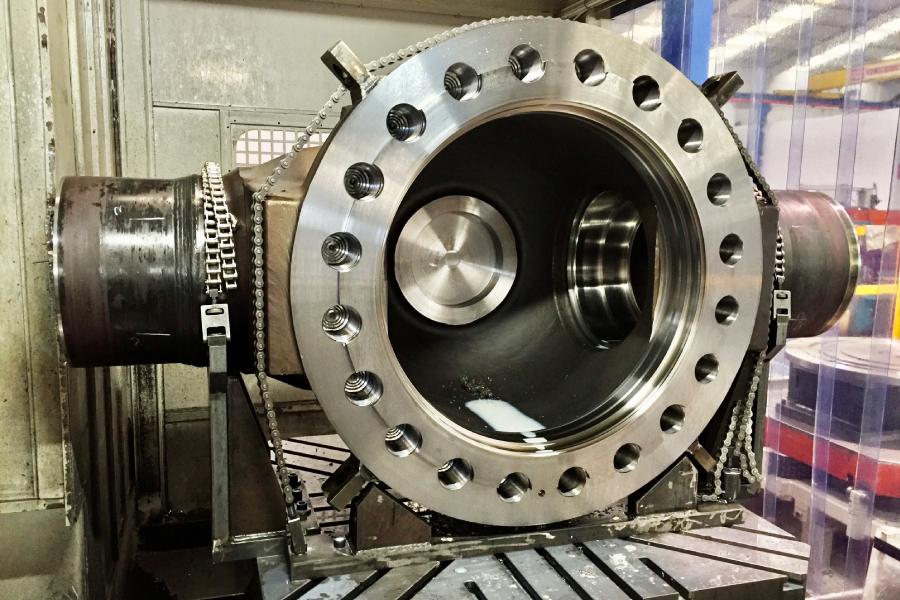
Impact of industry 4.0 on CNC machining accuracy
Industry 4.0 has profoundly transformed CNC machining, especially in terms of accuracy. Thanks to digital connectivity and real-time data usage, it is possible to adjust and control machining operations with unprecedented accuracy. IoT sensors integrated into CNC machines enable instant detection and correction of deviations during the machining process. This ensures that the final products meet exact specifications, minimizing dimensional errors. Additionally, continuous data collection helps predict and prevent issues before they affect precision, optimizing performance and reducing waste.
The role of automation in CNC machining accuracy
Automation plays a crucial role in CNC machining accuracy by removing human intervention in repetitive processes, thereby reducing the margin for error. Automated systems for tool adjustments, positioning, and part changes ensure that each stage of the machining process is performed uniformly and accurately. Automation allows for real-time micro-adjustments and reduces part-to-part variability, which is essential in sectors where tolerances must be tightly controlled, such as aerospace and automotive.
Strategies for improving dimensional tolerance in critical parts
When machining critical parts, maintaining tight dimensional tolerances is essential to ensure the parts meet their design specifications. To improve these tolerances, careful CNC programming is key, taking into account cutting speeds, tool temperature, and material type. The use of advanced clamping devices, specific cooling, and lubrication systems also helps reduce thermal and physical deformations, preventing dimensional changes during cutting. Another strategy is the implementation of post-machining techniques, such as precision polishing or grinding, to ensure final accuracy in parts that require extremely tight tolerances.
Advances in materials for high-accuracy CNC machining
The development of advanced materials, such as high-strength alloys, and hard coatings, has enabled higher-precision machining. These materials, more stable and wear-resistant, minimize deformation risk and improve cutting quality. For instance, cutting tools made with tungsten carbide or diamond coatings better withstand abrasion and maintain accuracy for longer periods. Additionally, the use of specific materials for particular applications, such as titanium in the aerospace sector, helps achieve high-quality finishes without compromising precision.
Quality control techniques to ensure accuracy in CNC machining
Quality control is essential to guarantee accuracy in CNC machining and is implemented through advanced techniques such as coordinate measuring machine (CMM) inspection, laser scanning, and computed tomography. These tools allow exact measurement of part dimensions and tolerances, comparing them with CAD designs. Additionally, in-process inspections help identify and correct deviations before they impact the final product, thus improving precision and consistency in each produced part.
The importance of CAD/CAM software in CNC accuracy
CAD/CAM software is the foundation of CNC machining accuracy as it enables the creation of 3D designs and programming of each step in the manufacturing process. Well-configured software helps optimize tool paths, adjust cutting speeds, and predict potential machining issues, increasing the final product’s precision. Furthermore, using simulations in CAD/CAM allows verification of the process feasibility before physical production, reducing the likelihood of errors and ensuring each part meets desired quality standards.
Tool life optimization to maintain accuracy in CNC machining
Maintaining precision in CNC machining largely depends on the durability and condition of cutting tools. Tool life optimization is achieved through proper maintenance, including regular inspection and sharpening. Additionally, advanced tool coatings, such as titanium nitride or diamond, enhance wear resistance and reduce friction, maintaining precision over extended periods. Real-time monitoring systems to measure tool wear and vibration also contribute to prolonging tool life and preventing misalignments that could affect precision.
Factors that take part in the machining precision
Physical factors
The influence of physical factors in the processing of parts is mainly manifested in two aspects:
On the processing side
Geometric accuracy requirements are very high. If there is an error in the geometric accuracy, it will directly cause the measurement obtained with the machining to be out of range.
Currently, most of the CNC machinery refers to combined equipment and the precision of the assembly between its mechanical components directly affects the degree of precision of the machining of the parts that are made, so there are certain hidden dangers in the process of machining.
The constant pursuit of maximum precision is an unavoidable task in the world of CNC machining. Every micrometer matters, and every step towards perfection is crucial. By exploring how chip removal machining in the CNC era can further enhance this precision, we immerse ourselves in a world where every machine movement translates into quality and efficiency.
At the same time, the aging of machinery will also reduce the accuracy of machined parts. If the CNC machinery is used for a long time, it will cause erosion and aging of its different internal components, especially if the preventive maintenance is not adequate.
The influence of human factors
The machinery must be controlled by staff. The incorrect or irregular operation of the employees will affect the final precision of the machined product.
Thermal deformation factors
When the machine is working, a large amount of heat is generated due to friction with each other, and the mechanical system will be deformed by heat, which will affect the accuracy.
Thermal deformation mainly involves the structure of the machine tool, the workpiece, the clamping device and the tool. First of all, the deformation of the machine tool includes the deformation of itself and the structure.
The long-term operation of the machine tool makes the temperature of the structure of the machine tool to increase linearly, which affects the fit between the various parts of the machine tool, and then the machining accuracy of the workpiece.
In addition, the machining process by chip removal also generates a large amount of heat, whose control is essential to obtain the required final machining precision. Due to this, today all CNC machines have internal cooling systems during the machining process, which mitigate the effects of the heat generated.
Force deformation factors
Within machining there are many factors that cause the system to be deformed. For example, machine tools, fixtures, and work pieces can generate various forces such as gravity, clamping force, and cutting force during operation.
In addition to bearing their own working pressure, the parts must also bear the forces generated by them and the friction between the equipment.
Certain elements such as tools (equipment to fix the part to be machined in the machine), clamps and tools are subject to high working pressures, and the components will move during the machining process. In addition, certain pressures between the components will cause different degrees of machining deformation, including changes in shape and position.
These deformations will affect the operation of the system and will have a certain impact in the machine´s lifetime, which will shorten its years of life and affect the accuracy of the parts.
As in the previous factor, correct preventive maintenance will increase the useful life of the CNC machine.
CNC programming factors
Scheduling properly can prevent machining errors, especially those caused by dimensional tolerance conversion.
Therefore, at the first stage of CNC programming, it is necessary to properly choose the programming origin. In addition, the programmed path cannot be ignored and its correct choice will improve the efficiency and the machining of the part. Otherwise, it will directly affect the precision of the machining.
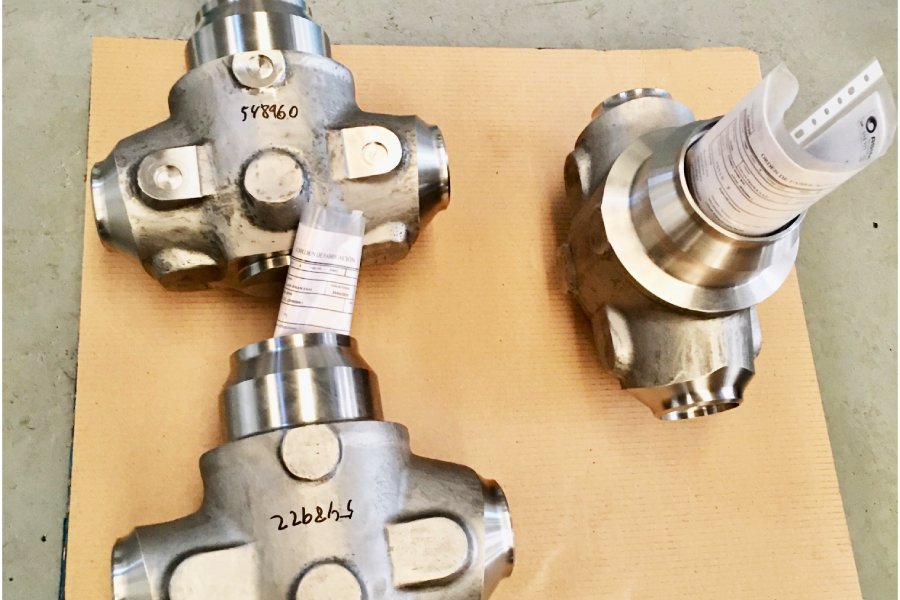
Internal factors
The internal factors that affect the precision of the pieces are manifested mainly in the irregular installation of machinery and in the precision errors of the machining systems. If the machine tool has many defects and deficiencies, the machine will produce parts with large errors in the production process.
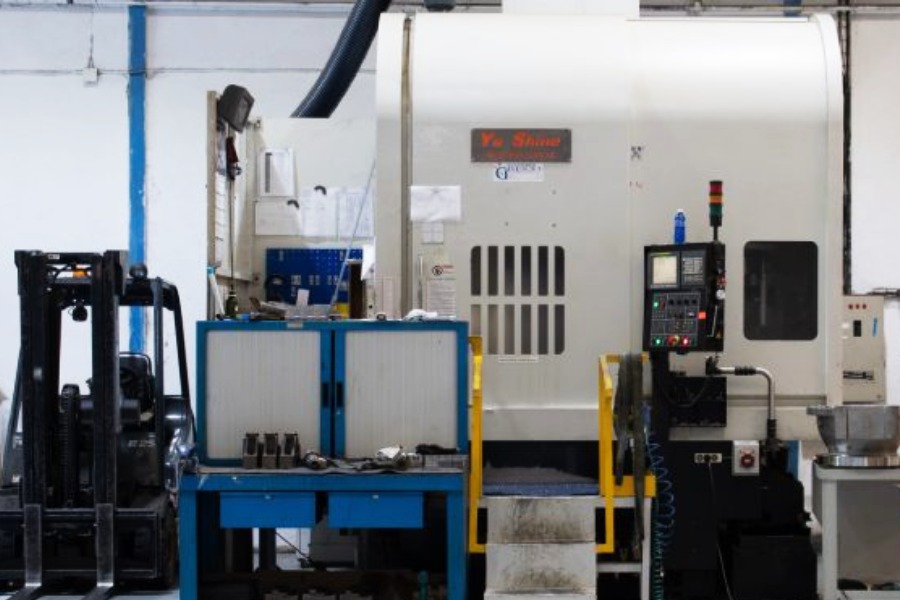
Machinery at Asimer Group
- Trevisan machining centers
- CNC vertical lathes
- CNC Horizontal Machining Centers
- CNC horizontal lathes
The Technical Department at Asimer Group collects the specifications and requirements of each customer and we evaluate the need or not of having external suppliers. Each phase of the project is negotiated and coordinated, and logistics is managed, guaranteeing maximum compliance with the desired technical requirements.