Machining and welding for predictive industrial maintenance is key to ensuring reliability and extending the service life of pumps, valves and compressors. In sectors such as Oil & Gas, cryogenics or water treatment, these solutions allow you to anticipate failures, optimize costs and reduce the risk of unplanned shutdowns.
These solutions may include the machining of large-dimension valves, particularly for critical components exposed to high pressure and temperature.
Similarly, to ensure durability in demanding environments, welding techniques for corrosive environments are applied to parts exposed to aggressive agents.
At ASIMER Group, we provide value as a specialized technical partner, combining high-precision CNC machining, specialized welding, and advanced coatings to deliver solutions aligned with the most demanding international standards.
Our expertise also includes the machining of stainless steel valves and pumps, which is especially useful in industries such as petrochemicals and cryogenics.
These capabilities allow manufacturers and industrial operators to strengthen the reliability of their equipment, optimize costs, and reduce the risk of unplanned downtime.
Additionally, we promote the adoption of solutions that help reduce the carbon footprint of industrial pumps and valves, aligning with our clients’ sustainability objectives.
Why does a specialized partner in machining and welding solutions for predictive maintenance make a difference?
Having a specialized industrial partner like ASIMER makes a difference in any predictive maintenance strategy, as it provides comprehensive technical support tailored to the demands of each sector. This ensures that critical components—pumps, valves, compressors—operate optimally for longer, reducing unplanned downtime costs and minimizing operational risks.
This is key in high-precision machining for the Oil & Gas sector, where maximum reliability is required for parts subjected to extreme conditions.
In this context, ASIMER stands out by offering industrial machining for predictive maintenance, with comprehensive solutions that enhance equipment reliability.
Key advantages of a partner like ASIMER include:
🔹 High-precision CNC machining tailored to each part and application.
To optimize resources, many industrial companies outsource machining and specialized welding processes. This is especially common in the field of machining and welding outsourcing for Oil & Gas, where technical and regulatory requirements are highly demanding.
ASIMER has advanced CNC technology, such as Trevisan machining centers, capable of machining large or complex components. Our machining processes are customized for each sector (Oil & Gas, cryogenics, naval, etc.), working with materials such as stainless steels, superalloys, or special castings.
The result is a precise fit that facilitates assembly, optimizes performance, and reduces premature wear—essential in a well-designed predictive maintenance plan.
🔹 Specialized welding (TIG, automatic MIG, PTA) to enhance durability
Welding is much more than a joining technique; in critical applications, it is an active reinforcement against wear, corrosion, or mechanical fatigue.
ASIMER offers:
- TIG welding, ideal for high-quality joints in stainless steels and sensitive alloys.
- Automatic MIG welding, used for large series or repetitive geometries requiring uniformity.
- PTA welding (Plasma Transferred Arc) for hardfacing and regeneration of wear zones in components such as valve seats or pump shafts.
All these processes are supported by qualified procedures (PQR/WPS) and certified operators according to international standards such as ASME IX and ISO 3834-2, ensuring consistent and traceable results.
🔹 Technical coatings for aggressive environments
In high-demand sectors, various coating types for industrial valves in extreme environments are applied to extend the service life of critical components.
In industries such as petrochemicals or cryogenics, parts are exposed to extreme conditions (pressure, temperature, corrosion, abrasion). ASIMER applies technical coatings (e.g., Stellite, Inconel, other hardfacings) that extend component life and reduce the need for corrective interventions.
These coatings are applied through controlled processes, optimizing adhesion and thickness according to the application, and are essential for parts such as cryogenic valves or industrial pumps.
🔹 Added value beyond a standard supplier
Choosing a partner that provides predictive maintenance services allows companies to anticipate failures and optimize intervention cycles.
Unlike a standard supplier that simply performs one-off tasks, a partner like ASIMER:
✅ Provides technical knowledge to anticipate failures and recommend improvements.
✅ Offers flexibility to adapt to drawings, specifications, and tight deadlines.
✅ Ensures compliance with international standards and regulations, including non-destructive testing (PT, UT, MT) by qualified personnel.
✅ Integrates solutions with a comprehensive vision aligned with predictive maintenance objectives.
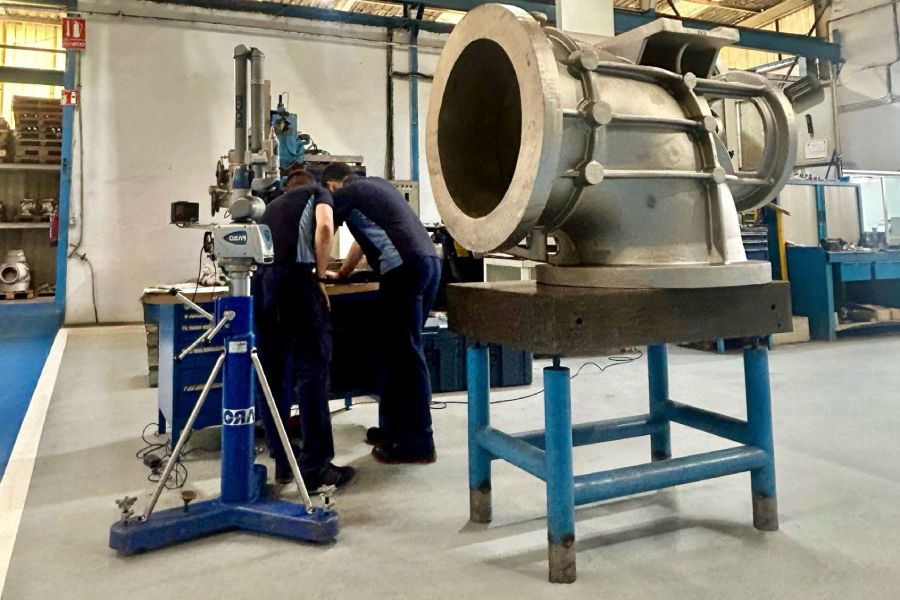
CNC machining solutions for predictive maintenance of critical components
High-precision CNC machining is a key element in ensuring that industrial components—pumps, valves, compressors, and other critical parts—meet the specifications required by predictive maintenance plans and industry quality standards.
In many projects, predictive maintenance and corrective maintenance strategies are compared, evaluating how precision machining helps anticipate failures and reduce unplanned interventions.
At ASIMER, we offer extensive machining capabilities thanks to our advanced technology:
- Trevisan machining centers, ideal for large or complex components such as pump casings, valve bodies, or large shafts.
- Vertical and horizontal CNC lathes, for precise work on cylindrical parts, flanges, or covers.
- State-of-the-art milling machines, providing versatility for flat surfaces, slots, or precision housings.
The result is an exact fit that facilitates assembly, optimizes performance, and reduces premature wear—essential in a well-designed predictive maintenance plan.
Our CNC machining for critical parts ensures components with precise geometries and optimal finishes for integration into complex systems.
We also manage outsourced machining and welding for manufacturers seeking a specialized and flexible partner.
Technical benefits of CNC machining applied to predictive maintenance
✅ Precise geometries for reliable assembly:
CNC machining delivers parts with exact shapes that integrate into equipment without the need for additional on-site adjustments, minimizing the risk of failures due to misalignment or improper assembly.
✅ Optimized surfaces to reduce wear:
The surface quality achieved through advanced machining processes lowers friction coefficients in moving parts and prevents stress concentration points, essential for extending service life in sectors like Oil & Gas or naval industry.
✅ Compatibility with demanding materials:
ASIMER’s processes handle materials such as stainless steels, special castings, corrosion-resistant alloys, or superalloys used in cryogenic or petrochemical applications.
✅ Adaptation to sector specifications:
Our machining aligns with the requirements of high-demand sectors such as cryogenics, desalination, or petrochemicals, adding value to predictive maintenance by ensuring durable and reliable components.
Request more information about our machining and welding solutions
Integration with quality controls
Every machined part undergoes thorough dimensional inspection in our metrology room and with our measuring arm, ensuring compliance with client requirements and applicable standards.
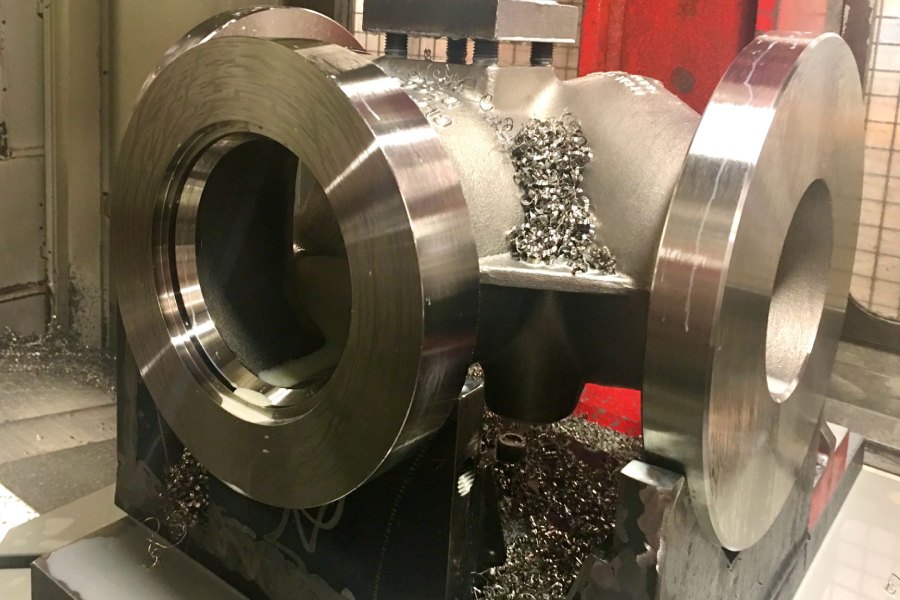
Welding and coating solutions for industrial predictive maintenance
Technical welding solutions and advanced coatings are an essential pillar of predictive maintenance strategies, as they not only repair worn parts but also strengthen and extend their service life before critical failures occur.
At ASIMER Group, we apply welding and coating technologies tailored to each sector’s conditions and requirements:
TIG welding (Gas Tungsten Arc Welding)
TIG welding is ideal for high-precision, high-quality joints, especially in materials sensitive to deformation or corrosion, such as stainless steels and superalloys.
👉 Used for components where structural integrity and bead appearance are critical, such as valve seats, shafts, or parts exposed to severe thermal cycles.
Automatic MIG welding (Metal Inert Gas)
Automatic MIG welding is an efficient solution for components requiring uniform joints in large series or repetitive geometries.
👉 At ASIMER, it is particularly useful for regenerating wear zones in pump casings, valve bodies, or covers subjected to constant mechanical stress.
PTA welding (Plasma Transferred Arc) and hardfacing
PTA welding is a metal deposition coating technique that allows high-hardness materials to be applied to wear- or corrosion-prone areas.
👉 Used, for example, for coating valve sealing surfaces, seats, shafts, or components exposed to cavitation or erosion.
👉 Hardfacing with PTA provides precise control of deposit thickness and quality, ensuring superior adhesion and high resistance under extreme conditions.
Technical coatings with high-performance materials
At ASIMER, we apply coatings with materials such as:
- Stellite®: cobalt-based alloy for reinforcing components against friction and erosion wear.
- Inconel®: nickel-based alloy that provides resistance to corrosion and high temperatures, ideal for petrochemical plants or cryogenic systems.
These coatings are selected based on the application, fluid type, temperature, and operating conditions.
Advantages for predictive maintenance
✅ Extend component life before failures occur.
✅ Reduce corrective intervention cycles.
✅ Ensure compliance with international standards (ASME IX, ISO 3834-2).
✅ Enable full traceability through qualified procedures (PQR/WPS) and certified operators.
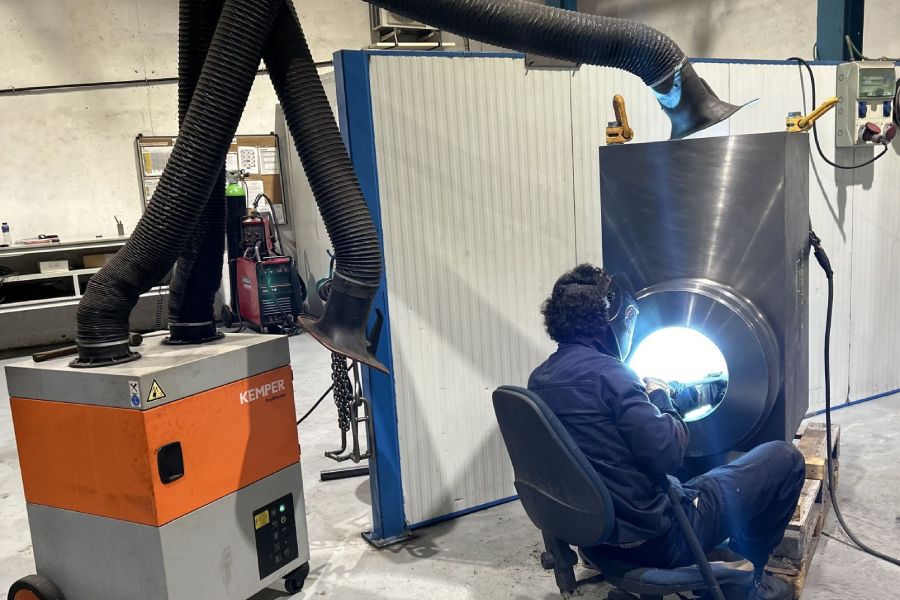
Quality control and metrology in predictive maintenance solutions
Quality control and advanced metrology are essential elements in any effective predictive maintenance strategy. It’s not enough to manufacture or repair a component: precise verification is needed to ensure it meets the exact specifications required for its function in critical industrial environments.
At ASIMER Group, we integrate these capabilities as an essential part of our technical solutions.
High-precision metrology
Our metrology lab is equipped with advanced technology for the dimensional control of machined and welded parts, ensuring compliance with client or standard-specified tolerances.
Our equipment includes:
- Portable, flexible measuring arm, ideal for large or complex parts, providing fast, precise measurements at any process stage.
- CMMs (Coordinate Measuring Machines), measurement instruments, special gauges, and laser inspection systems, ensuring every component meets dimensional and geometric requirements.
The result is a perfect fit during assembly, reducing the risk of failures due to misalignment or undetected deformation.
Non-destructive testing (NDT) to ensure integrity
Non-destructive testing is an integral part of ASIMER’s processes, applied to both new parts and those undergoing repair or regeneration.
👉 Techniques used:
- Liquid penetrant testing (PT): for detecting surface cracks, porosity, or open discontinuities in non-porous materials, essential for valves, pump casings, or seats.
- Ultrasonic testing (UT): for detecting internal defects or structural failures in critical components.
- Magnetic particle testing (MT): in ferromagnetic materials, for locating cracks or subsurface defects.
These tests are performed by personnel certified to international standards, ensuring reliable, documented results.
Added value in predictive maintenance
Quality control and metrology provide:
✅ Full traceability of machined or repaired components.
✅ Safety in subsequent assembly and operation.
✅ Reduced risk of unplanned downtime due to undetected defects.
Through these processes, ASIMER strengthens the reliability of parts used in critical systems in sectors like Oil & Gas, cryogenics, or desalination.
Applications of machining and welding solutions for predictive maintenance in key sectors
The CNC machining, technical welding, and advanced coating solutions offered by ASIMER Group are designed to meet the needs of the most demanding industrial sectors, where predictive maintenance is essential for ensuring operational reliability and continuity.
👉 Oil & Gas:
Pumps and valves in this sector operate under high pressure, variable temperatures, and highly corrosive environments. ASIMER adds value through precision machining of critical components, applying Stellite or Inconel coatings, and regenerating surfaces via PTA welding, extending equipment life and reducing unplanned downtime.
👉 Water treatment and desalination:
Components must withstand constant wear caused by fluids with high concentrations of salts or chemicals. ASIMER’s solutions, such as machining corrosion-resistant parts and applying technical coatings to pumps and valves, ensure greater durability and less frequent interventions.
👉 Cryogenics:
Cryogenic equipment operates in extremely low-temperature environments, requiring parts with coatings that maintain their structural and functional integrity. ASIMER contributes with specialized coatings and high-precision machining of materials suitable for low temperatures, optimizing the performance and reliability of cryogenic valves and pumps.
👉 Naval industry:
Constant exposure to saline environments and extreme conditions demands high-level technical solutions. ASIMER applies CNC machining and anti-corrosion welding to key components, along with protective coatings, to ensure the reliability of critical systems and extend maintenance cycles.
Frequently asked questions (FAQs)
What solutions does ASIMER offer for predictive maintenance?
ASIMER offers a range of technical solutions designed to strengthen predictive maintenance of industrial equipment. This includes high-precision CNC machining, specialized welding (TIG, automatic MIG, PTA), technical coatings like Stellite or Inconel, and a complete non-destructive testing service to verify component integrity.
Can machining or welding be outsourced separately?
Yes, ASIMER provides flexible services tailored to each client’s needs. You can outsource only high-precision machining or choose specialized welding services, depending on the project scope and predictive maintenance plan objectives.
What are the benefits of technical coatings?
Technical coatings protect components against wear, corrosion, and abrasion, significantly increasing their service life and reducing the number of corrective interventions. This results in a lower total cost of ownership and greater operational reliability in critical sectors such as Oil & Gas or cryogenics.
Ready to optimize your equipment’s reliability?
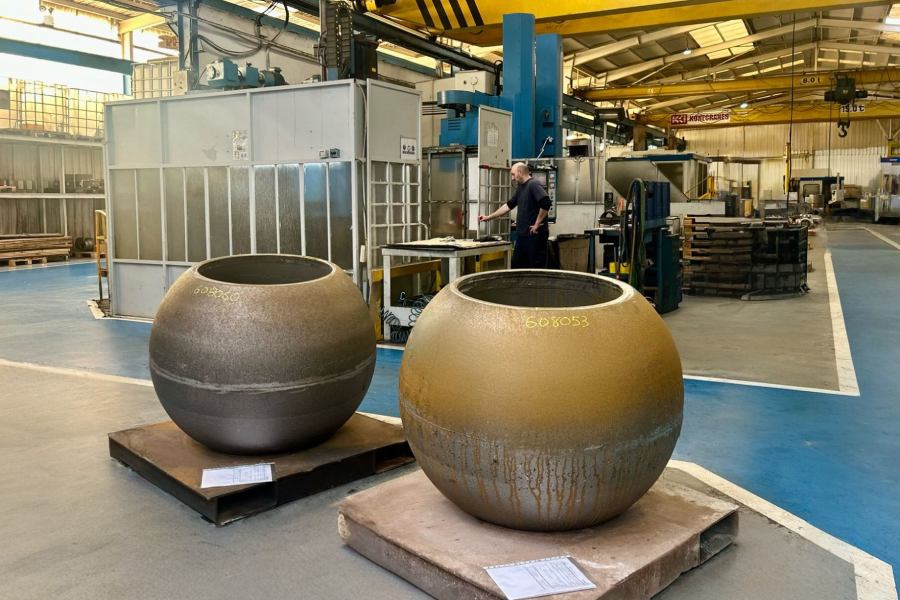